Heat treatment of steel is a critical process that involves heating and cooling the metal to alter its physical and mechanical properties without changing its shape. The duration of heat treatment varies significantly depending on the type of steel, the desired properties, and the specific heat treatment process being used. Common heat treatment processes include annealing, normalizing, hardening, and tempering, each with its own time requirements. For instance, annealing can take several hours to days, while hardening and tempering might take a few hours. The thickness and size of the steel also play a role in determining the duration, as thicker sections require longer heating and cooling times to ensure uniform treatment.
Key Points Explained:
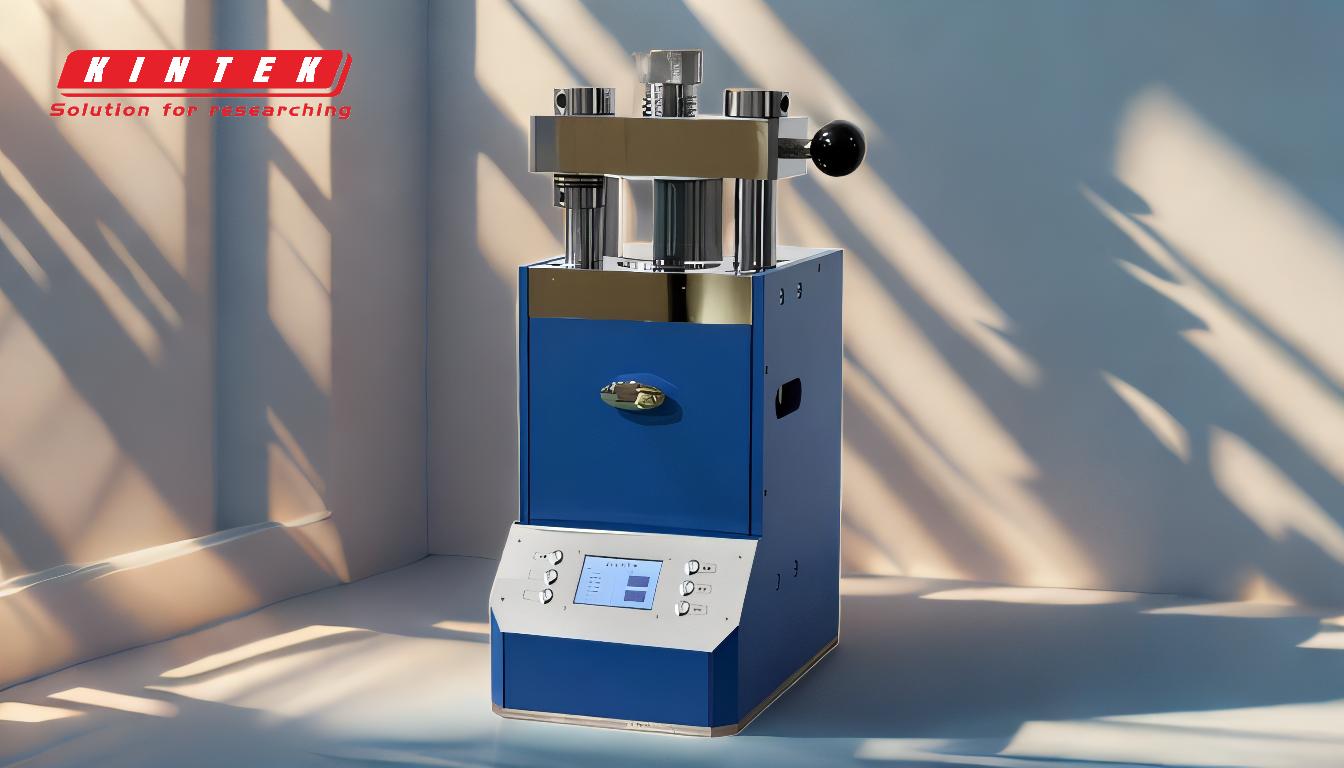
-
Types of Heat Treatment Processes:
- Annealing: This process involves heating steel to a specific temperature and then allowing it to cool slowly, often in a furnace. The goal is to soften the steel, improve its machinability, and relieve internal stresses. Annealing can take several hours to days, depending on the size and type of steel.
- Normalizing: Similar to annealing, but the cooling process is faster, usually in still air. This process refines the grain structure and improves mechanical properties. It typically takes less time than annealing, often a few hours.
- Hardening: Steel is heated to a high temperature and then rapidly cooled, usually by quenching in water, oil, or air. This process increases hardness and strength but can make the steel brittle. The heating phase can take a few hours, while quenching is almost instantaneous.
- Tempering: After hardening, steel is often tempered by reheating it to a lower temperature to reduce brittleness and improve toughness. Tempering can take a few hours, depending on the desired properties.
-
Factors Influencing Heat Treatment Duration:
- Steel Composition: Different alloys require different heat treatment times. For example, high-carbon steels may need longer annealing times compared to low-carbon steels.
- Thickness and Size of the Steel: Thicker and larger sections take longer to heat uniformly and cool properly. This is because heat must penetrate through the entire cross-section of the material.
- Desired Properties: The specific mechanical properties required (e.g., hardness, toughness) will influence the duration of the heat treatment process. For instance, achieving a high level of hardness may require longer hardening and tempering times.
-
Typical Timeframes for Common Processes:
- Annealing: 4-24 hours or more, depending on the steel type and size.
- Normalizing: 1-4 hours, depending on the steel type and size.
- Hardening: 1-2 hours for heating, with quenching taking only a few seconds.
- Tempering: 1-4 hours, depending on the temperature and desired properties.
-
Importance of Cooling Rates:
- The rate at which steel is cooled after heating is crucial in determining the final properties. Slow cooling, as in annealing, results in softer steel, while rapid cooling, as in hardening, increases hardness but may also increase brittleness.
-
Equipment and Environmental Factors:
- The type of furnace used, the atmosphere within the furnace (e.g., controlled atmosphere), and the cooling medium (e.g., water, oil, air) all influence the heat treatment duration. For example, a muffle furnace can provide precise temperature control, which may reduce the overall time needed for certain processes.
In summary, the duration of heat treatment for steel is highly variable and depends on the specific process, the type of steel, and the desired outcomes. Understanding these factors is crucial for achieving the desired mechanical properties and ensuring the quality of the final product.
Summary Table:
Heat Treatment Process | Typical Duration | Key Factors |
---|---|---|
Annealing | 4-24 hours or more | Steel type, size, cooling rate |
Normalizing | 1-4 hours | Steel type, size, cooling rate |
Hardening | 1-2 hours (heating) | Steel composition, quenching medium |
Tempering | 1-4 hours | Desired properties, temperature |
Need help optimizing your steel heat treatment process? Contact our experts today for tailored solutions!