Heating steel involves a complex process that depends on various factors, including the size and shape of the workpiece, the type of heat treatment required, and the desired properties of the final product. The holding time, which is a critical part of the heat treatment process, is influenced by the heating temperature, furnace charging, and workpiece placement. Uniform temperature distribution, proper gas circulation, and careful selection of cycle times and temperatures are essential to ensure high-quality results. Additionally, understanding the specific application and property requirements of the steel part helps determine the appropriate heat treatment method. Below, we break down the key factors and considerations that determine how long it takes to heat treat steel.
Key Points Explained:
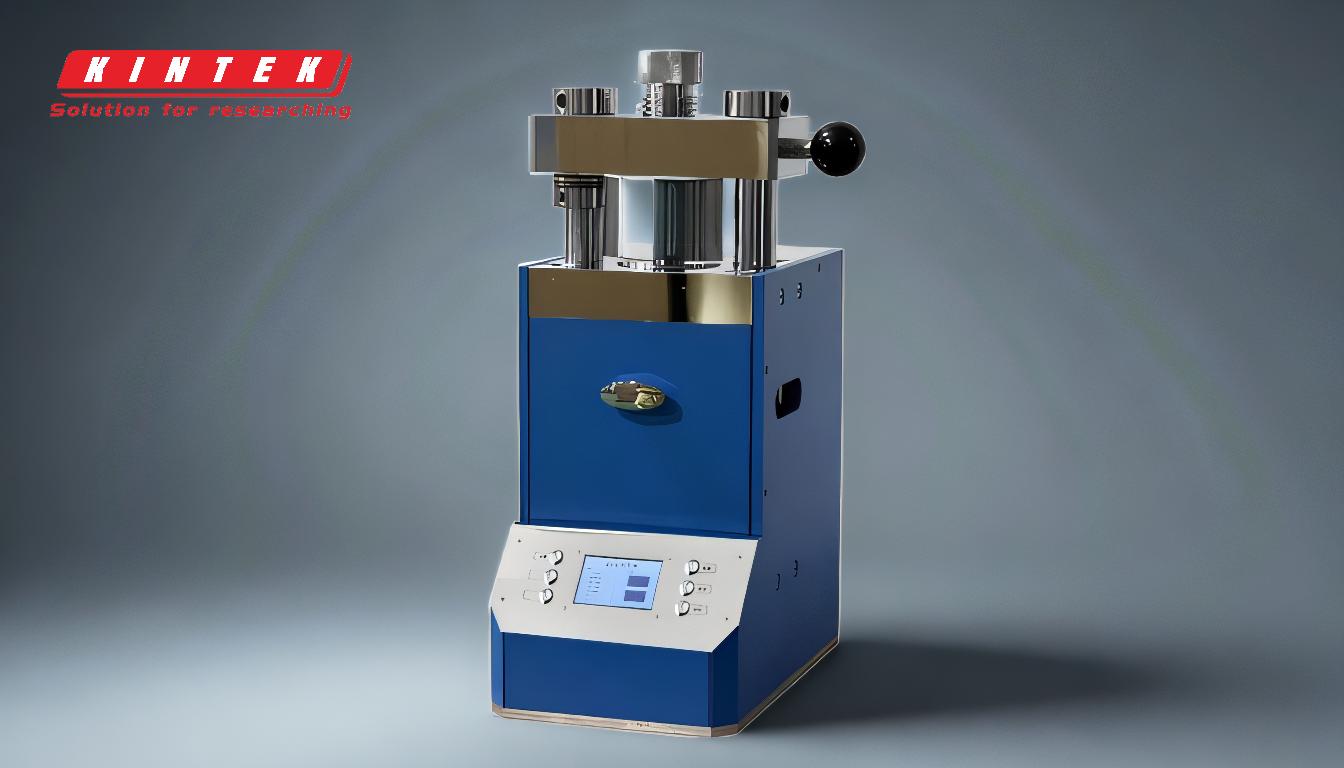
-
Factors Influencing Heat Treatment Time:
- Size and Shape of the Workpiece: Larger or more complex-shaped workpieces require longer heating times to ensure uniform temperature distribution throughout the material.
- Furnace Charging: The amount of material loaded into the furnace affects the heating time. Overloading the furnace can lead to uneven heating and longer cycle times.
- Workpiece Placement: Proper placement ensures efficient heat transfer and uniform heating. Poor placement can create hot or cold spots, extending the process time.
- Heating Temperature: Higher temperatures may reduce the time needed to reach the desired hardness or strength, but they must be carefully controlled to avoid material degradation.
-
Heat Treatment Processes and Their Time Requirements:
- Annealing: This process involves heating the steel to a specific temperature, holding it for a set period, and then slowly cooling it. The holding time can range from a few hours to several days, depending on the material and desired properties.
- Quenching: After heating, the steel is rapidly cooled to achieve high hardness. The heating time is relatively short, but the cooling process must be carefully managed to avoid cracking or distortion.
- Tempering: This process follows quenching and involves reheating the steel to a lower temperature to reduce brittleness. Tempering times are typically shorter, ranging from 30 minutes to a few hours.
- Case Hardening: Only the surface of the steel is hardened, which can reduce the overall heat treatment time compared to processes that treat the entire workpiece.
-
Importance of Uniform Temperature Distribution:
- Uniform heating ensures consistent material properties throughout the workpiece. Uneven heating can lead to weak spots or structural failures.
- Advanced furnaces with precise temperature control and proper gas circulation help achieve uniform heating, reducing the risk of defects.
-
Cycle Times and Temperature Selection:
- The choice of cycle times and temperatures depends on the steel grade and the desired mechanical properties. For example, high-carbon steels may require longer holding times at lower temperatures compared to low-carbon steels.
- Anticipating potential issues, such as furnace malfunctions or improper gas flow, can prevent delays and ensure efficient heat treatment.
-
End Application and Property Requirements:
- The intended use of the steel part determines the heat treatment method and duration. For example, parts requiring high wear resistance may undergo longer heat treatment processes compared to those needing only moderate strength.
- Selective heat treatment, where only specific areas of the part are treated, can save time and resources while meeting performance requirements.
-
Maintenance and Downtime Considerations:
- Regular maintenance of heat treatment equipment ensures consistent performance and reduces the risk of unexpected downtime.
- Planning for potential issues, such as furnace wear or gas system failures, can minimize disruptions and keep the heat treatment process on schedule.
By carefully considering these factors, manufacturers can optimize the heat treatment process to achieve the desired material properties while minimizing time and resource expenditure.
Summary Table:
Factor | Impact on Heat Treatment Time |
---|---|
Size and Shape of Workpiece | Larger or complex shapes require longer heating for uniform temperature distribution. |
Furnace Charging | Overloading the furnace leads to uneven heating and extended cycle times. |
Workpiece Placement | Proper placement ensures efficient heat transfer; poor placement causes hot/cold spots. |
Heating Temperature | Higher temperatures reduce time but must be controlled to avoid material degradation. |
Heat Treatment Process | Annealing: hours to days; Quenching: short heating, rapid cooling; Tempering: 30 mins to hours. |
Uniform Heating | Ensures consistent material properties; advanced furnaces reduce defects. |
Cycle Times & Temperatures | Depends on steel grade and desired properties; high-carbon steels require longer holding times. |
End Application | Determines heat treatment method and duration; selective treatment saves time and resources. |
Maintenance | Regular maintenance prevents downtime and ensures consistent performance. |
Need help optimizing your steel heat treatment process? Contact our experts today for tailored solutions!