Calcination is a thermal process used to decompose materials or remove volatile components, often applied in metal extraction from ores. The amount of CO₂ released during calcination depends on the material being processed, particularly if it contains carbonates like limestone (CaCO₃). When limestone undergoes calcination, it decomposes into calcium oxide (CaO) and carbon dioxide (CO₂). The chemical reaction is: CaCO₃ → CaO + CO₂. For every ton of limestone calcined, approximately 0.44 tons of CO₂ are released, as CO₂ constitutes 44% of the molecular weight of CaCO₃. This process is a significant source of CO₂ emissions in industries like cement production.
Key Points Explained:
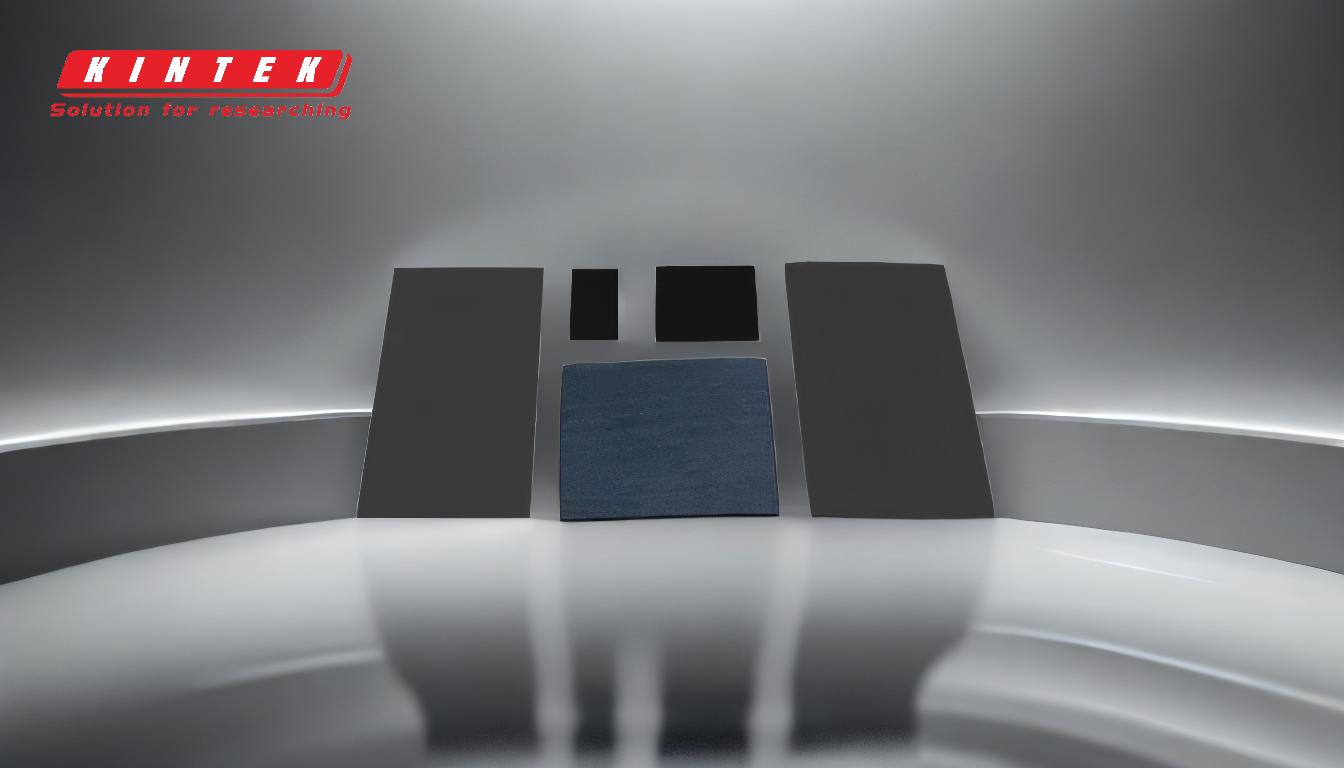
-
Definition of Calcination:
- Calcination is a thermal decomposition process that occurs at high temperatures, typically below the melting point of the material.
- It is used to remove volatile substances or decompose compounds, such as carbonates, hydroxides, or sulfates, into simpler forms.
-
CO₂ Release Mechanism:
- CO₂ is released during calcination when carbonates decompose. For example, limestone (CaCO₃) decomposes into calcium oxide (CaO) and carbon dioxide (CO₂).
- The chemical reaction is:
[ \text{CaCO}_3 \rightarrow \text{CaO} + \text{CO}_2 ] - This reaction is endothermic, requiring significant heat input.
-
Quantifying CO₂ Emissions:
- The molecular weight of CaCO₃ is 100 g/mol (40 g/mol for Ca, 12 g/mol for C, and 48 g/mol for O₃).
- The molecular weight of CO₂ is 44 g/mol (12 g/mol for C and 32 g/mol for O₂).
- Thus, CO₂ constitutes 44% of the weight of CaCO₃.
- For every ton of limestone calcined, approximately 0.44 tons of CO₂ are released.
-
Industrial Significance:
- Calcination is a critical step in cement production, where limestone is a primary raw material.
- The cement industry is one of the largest contributors to global CO₂ emissions, with calcination accounting for about 50-60% of the total emissions from cement production.
-
Environmental Impact:
- The CO₂ released during calcination contributes to greenhouse gas emissions and climate change.
- Efforts are being made to reduce emissions through alternative materials, carbon capture technologies, and energy-efficient processes.
-
Other Materials and CO₂ Release:
- While limestone is the most common example, other carbonates (e.g., magnesium carbonate, MgCO₃) also release CO₂ during calcination.
- The amount of CO₂ released depends on the specific carbonate's molecular composition.
By understanding the calcination process and its chemical basis, industries can better assess and mitigate their CO₂ emissions, contributing to more sustainable practices.
Summary Table:
Key Aspect | Details |
---|---|
Definition of Calcination | Thermal decomposition process at high temperatures, used to remove volatiles or decompose compounds like carbonates. |
CO₂ Release Mechanism | Carbonates (e.g., CaCO₃) decompose into oxides (e.g., CaO) and CO₂. |
Quantifying CO₂ Emissions | 1 ton of limestone releases ~0.44 tons of CO₂ (44% of CaCO₃'s molecular weight). |
Industrial Significance | Cement production relies heavily on calcination, contributing 50-60% of its CO₂ emissions. |
Environmental Impact | CO₂ emissions drive climate change; efforts focus on carbon capture and efficiency. |
Other Materials | Other carbonates (e.g., MgCO₃) also release CO₂ during calcination. |
Discover how to reduce CO₂ emissions in your industry—contact our experts today!