Injection molding can be highly profitable, but its profitability depends heavily on the scale of production. For large-volume orders, the initial costs of mold design and tooling are spread across many units, making the process cost-effective and profitable. However, for small-volume orders, the high upfront costs of press mold creation can significantly reduce profitability. The key to profitability lies in balancing production volume, mold costs, and material expenses. Below, we explore the factors influencing profitability in injection molding and how businesses can optimize their operations to maximize returns.
Key Points Explained:
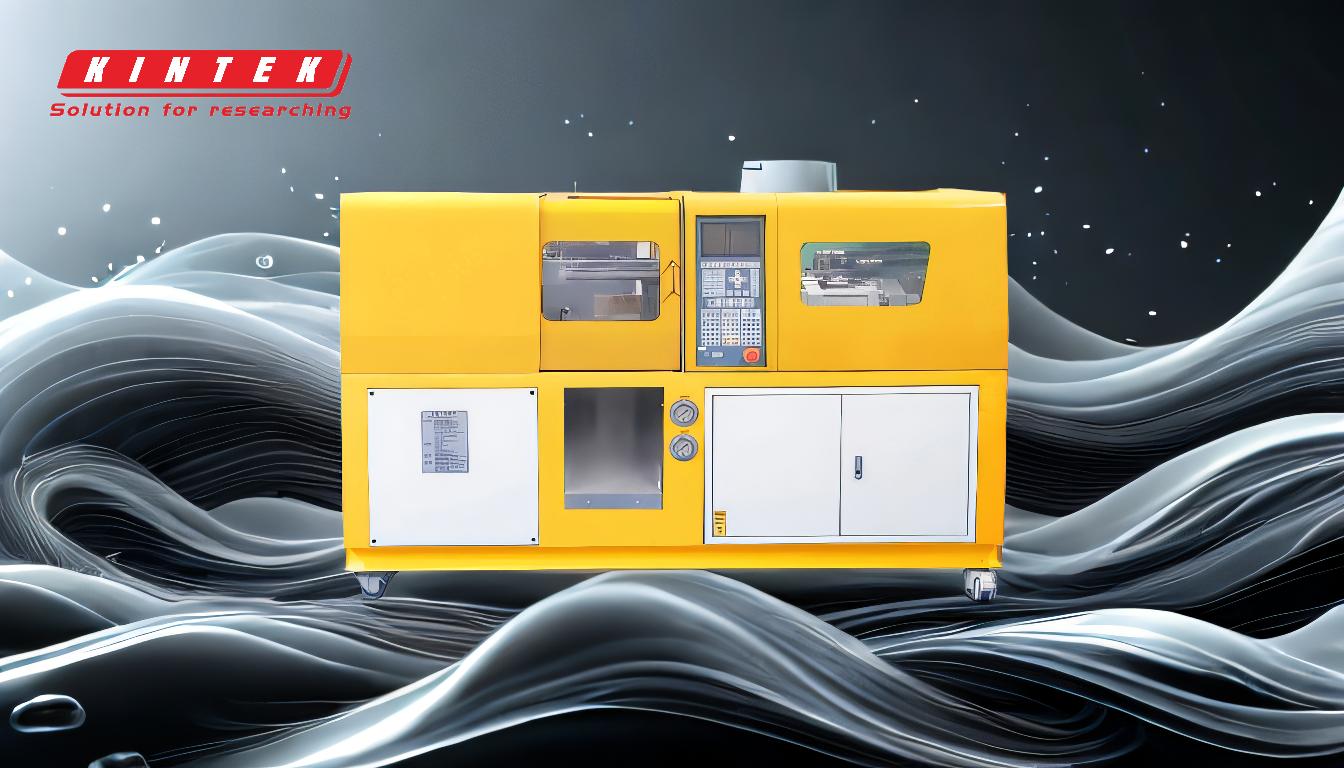
-
Dependence on Production Volume:
- Large-Volume Production: Injection molding becomes highly profitable when producing large quantities of parts. The initial costs of mold design and tooling are amortized over a high number of units, reducing the per-unit cost. This makes it ideal for industries like automotive, consumer goods, and electronics, where mass production is common.
- Small-Volume Production: For small orders, the high upfront costs of mold creation can make the process less profitable. The cost per unit remains high, as the fixed costs are not distributed over a large number of parts. This makes injection molding less suitable for prototyping or niche markets with low demand.
-
Mold Design and Tooling Costs:
- Upfront Investment: Mold design and tooling are the most significant expenses in injection molding. These costs can range from a few thousand to hundreds of thousands of dollars, depending on the complexity of the mold and the materials used.
- Cost Recovery: For large-volume orders, the cost of the mold is recovered quickly as production scales up. However, for small orders, the mold cost may never be fully recovered, leading to lower profitability.
-
Material Costs:
- Raw Materials: The choice of materials (e.g., thermoplastics, resins) impacts profitability. High-quality or specialized materials increase costs, but they may be necessary for certain applications.
- Material Efficiency: Efficient use of materials, such as minimizing waste and optimizing part design, can reduce costs and improve profitability.
-
Operational Efficiency:
- Cycle Time: Reducing the cycle time (the time it takes to produce one part) increases throughput and profitability. Automation and advanced machinery can help achieve faster cycle times.
- Labor Costs: Skilled labor is required for mold design, machine operation, and quality control. Reducing labor costs through automation or training can improve profitability.
-
Market Demand and Competition:
- High Demand: Industries with high demand for injection-molded parts (e.g., medical devices, packaging) offer more opportunities for profitability.
- Competition: In highly competitive markets, businesses must focus on cost efficiency and quality to maintain profitability.
-
Customization and Niche Markets:
- Custom Molds: Offering custom molds for niche markets can be profitable if the demand justifies the upfront costs. However, this requires careful market analysis to ensure a return on investment.
- Prototyping: While injection molding is not ideal for prototyping due to high costs, some businesses offer rapid prototyping services using less expensive molds or alternative methods.
-
Long-Term Profitability:
- Mold Lifespan: High-quality molds can be used for hundreds of thousands of cycles, making them a long-term investment. Proper maintenance and storage extend mold life, improving profitability over time.
- Repeat Orders: Building long-term relationships with clients who place repeat orders can ensure steady revenue and profitability.
-
Sustainability and Cost Savings:
- Recycling: Using recycled materials or recycling waste from the molding process can reduce costs and appeal to environmentally conscious clients.
- Energy Efficiency: Investing in energy-efficient machinery reduces operational costs and improves profitability.
In conclusion, injection molding is most profitable in large-volume production scenarios where the high initial costs of mold design and tooling can be spread across many units. For small-volume orders, profitability is limited due to these upfront costs. However, by optimizing production processes, reducing material waste, and targeting high-demand markets, businesses can improve their profitability in injection molding.
Summary Table:
Key Factor | Impact on Profitability |
---|---|
Production Volume | Large volumes reduce per-unit costs; small volumes increase per-unit costs. |
Mold Design & Tooling | High upfront costs; recovered faster in large-volume production. |
Material Costs | Specialized materials increase costs; efficient use reduces expenses. |
Operational Efficiency | Faster cycle times and automation improve throughput and reduce labor costs. |
Market Demand | High-demand industries (e.g., medical, packaging) offer better profitability opportunities. |
Customization | Profitable for niche markets if demand justifies upfront costs. |
Sustainability | Recycling and energy-efficient machinery reduce costs and appeal to eco-conscious clients. |
Ready to optimize your injection molding process? Contact us today to learn how we can help maximize your profitability!