PVD (Physical Vapor Deposition) coating is renowned for its durability and scratch resistance, making it a popular choice for various industries, including jewelry, watches, and cutting tools. The coating process involves depositing a thin layer of material onto a substrate, typically ranging from 0.25 to 5 microns in thickness. This thin yet robust layer provides excellent resistance to scratches, wear, and corrosion. While PVD-coated products may develop minor scratches over time, they generally maintain their appearance and functionality far longer than non-coated counterparts. With proper care, PVD-coated items can remain in excellent condition for over a decade, making them a cost-effective and long-lasting solution for many applications.
Key Points Explained:
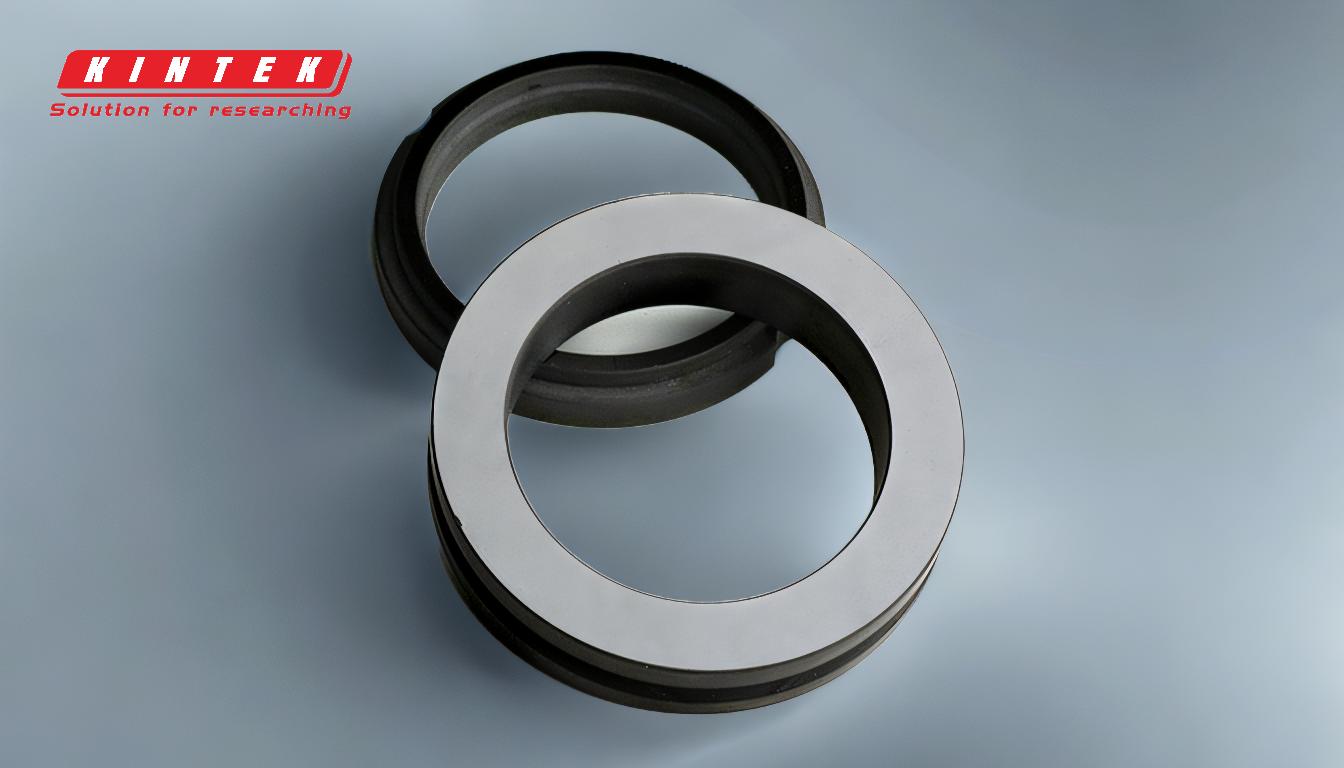
-
Thin Yet Durable Coating:
- PVD coatings are extremely thin, ranging from 0.25 to 5 microns. Despite their thinness, these coatings are highly durable and resistant to scratches. The molecular-level changes to the metal surface result in a hard, wear-resistant layer that can withstand significant mechanical stress.
-
Longevity and Maintenance:
- PVD-coated products are designed to last for many years, often exceeding a decade with proper care. While minor scratches may occur over time, the overall appearance and functionality of the coating remain intact. Simple cleaning routines can help maintain the original color and finish of the coating.
-
Versatility in Applications:
- PVD coatings are used in a wide range of industries, including jewelry, watches, and cutting tools. In jewelry, PVD can replicate the appearance of more expensive metals like gold and bronze, providing a cost-effective alternative. In cutting tools, the coating enhances wear resistance and reduces cutting force, making it ideal for high-performance applications.
-
Advantages Over Traditional Coatings:
- PVD coatings offer several advantages over traditional coating methods. They operate at lower temperatures (around 500 °C), reducing the risk of thermal damage to the substrate. The coatings are also thinner, preserving the sharpness of tools and reducing cutting force and heat. Additionally, PVD coatings form compressive stress during cooling, which helps prevent crack formation and expansion.
-
Resistance to Corrosion and Oxidation:
- One of the key benefits of PVD coatings is their high resistance to corrosion and oxidation. This makes them suitable for use in harsh environments where exposure to moisture and chemicals is common. The coating's ability to protect the underlying metal ensures long-term durability and performance.
-
Economic and Production Benefits:
- PVD coating machines are computer-controlled, allowing for precise and efficient deposition of thin films. This reduces production costs and turnaround time, making PVD coating a cost-effective solution for both large-scale manufacturing and small batch production. The ability to multitask further enhances the efficiency of the coating process.
In summary, PVD coatings are highly scratch-resistant and offer numerous advantages, including durability, versatility, and cost-effectiveness. With proper care, PVD-coated products can maintain their appearance and functionality for many years, making them an excellent choice for a wide range of applications.
Summary Table:
Key Features | Details |
---|---|
Coating Thickness | 0.25 to 5 microns |
Scratch Resistance | Highly resistant, with minor scratches over time |
Durability | Lasts over a decade with proper care |
Applications | Jewelry, watches, cutting tools, and more |
Corrosion Resistance | Excellent resistance to moisture and chemicals |
Economic Benefits | Cost-effective, reduces production costs, and enhances efficiency |
Want to learn more about PVD coating benefits? Contact us today for expert advice!