Brazing stainless steel is a precise process that involves joining metal components using a filler metal with a lower melting point than the base metals. The process can be performed using flame, induction, or furnace heating methods. Proper preparation, including thorough cleaning to remove grease and oil, is essential to ensure a strong bond. After brazing, it is crucial to clean any residual flux and, if necessary, perform post-brazing heat treatment to enhance the joint's properties. The vacuum brazing process, in particular, involves careful preparation, assembly with filler metal, and post-brazing inspection to ensure quality.
Key Points Explained:
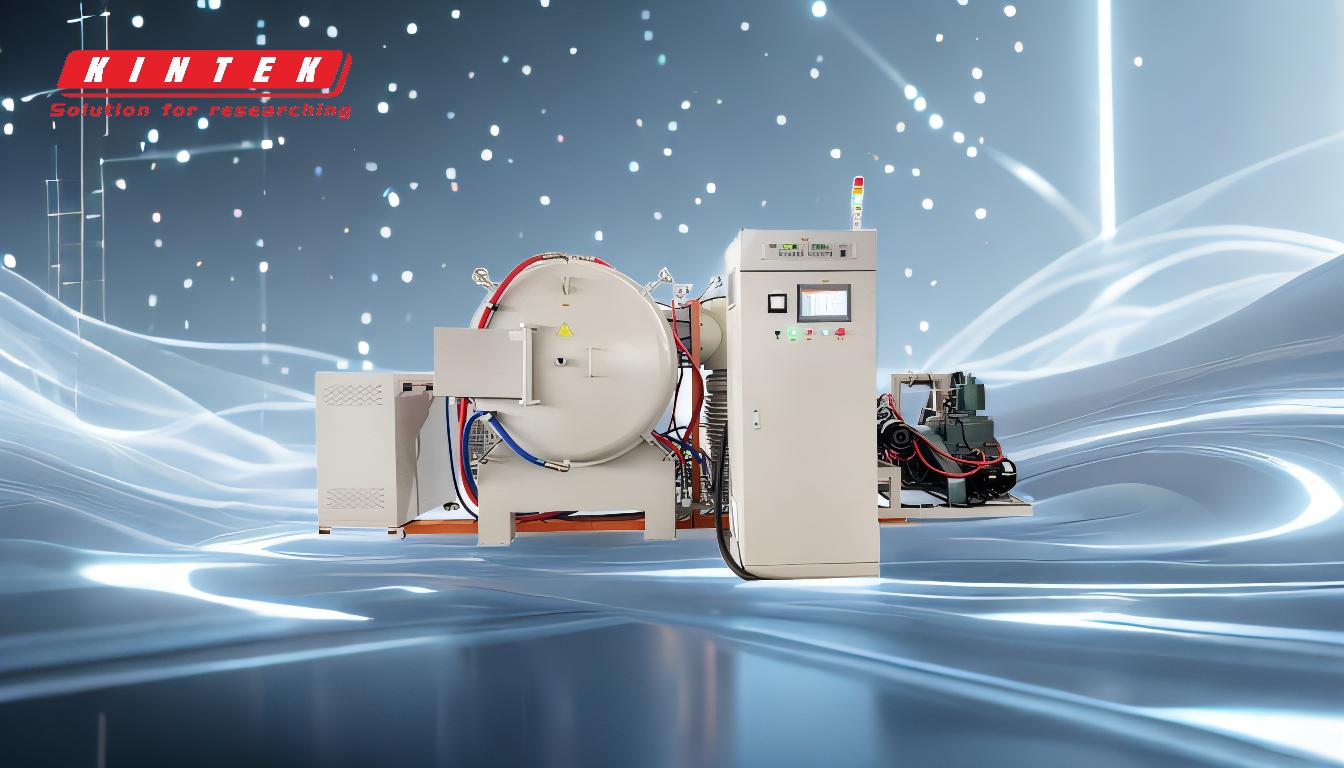
-
Heating Methods for Brazing Stainless Steel:
- Flame Brazing: This method uses a gas torch to heat the joint and filler metal. It is suitable for small-scale or manual operations.
- Induction Brazing: Induction heating is used to generate heat directly in the workpiece, making it efficient for high-volume production.
- Furnace Brazing: This method involves heating the entire assembly in a furnace, ensuring uniform heating and is ideal for complex or large components.
-
Pre-Brazing Preparation:
- Cleaning: Stainless steel must be thoroughly cleaned to remove grease, oil, and other contaminants. This ensures proper wetting of the filler metal and a strong bond.
- Immediate Brazing: After cleaning, brazing should be performed promptly to prevent recontamination of the surfaces.
-
Vacuum Brazing Process:
- Preparation: This includes cleaning and preparing the surfaces to be joined.
- Assembly and Filler Metal Placement: The components are assembled with the filler metal placed at the joint.
- Inspection: After the furnace process, the brazed joint is inspected to ensure it meets quality standards.
-
Post-Brazing Procedures:
- Cleaning Residual Flux: Any remaining flux must be removed to prevent corrosion and ensure the joint's integrity.
- Post-Brazing Heat Treatment: If required, heat treatment can be performed to relieve stresses and improve the mechanical properties of the joint.
By following these steps and methods, brazing stainless steel can be successfully accomplished, resulting in strong and durable joints suitable for various applications.
Summary Table:
Step | Details |
---|---|
Heating Methods | Flame, Induction, or Furnace Brazing for precise and uniform heating. |
Pre-Brazing Prep | Clean surfaces thoroughly to remove grease, oil, and contaminants. |
Vacuum Brazing Process | Prepare, assemble with filler metal, and inspect for quality. |
Post-Brazing Steps | Clean residual flux and perform heat treatment if needed for joint strength. |
Need expert guidance for brazing stainless steel? Contact us today for tailored solutions!