Chemical vapor deposition (CVD) is a versatile and widely used technique for depositing thin films of materials onto substrates. The process involves several key steps, including the vaporization of a precursor material, its decomposition or reaction on the substrate surface, and the formation of a solid film. CVD is highly adaptable, allowing for the deposition of a wide range of materials, including metals, semiconductors, and insulators. The process is controlled by parameters such as chamber pressure, substrate temperature, and the choice of precursor materials. CVD offers numerous advantages, including the ability to produce high-purity, dense films with excellent conformality over complex surfaces. It is used in various applications, from semiconductor manufacturing to the production of protective coatings.
Key Points Explained:
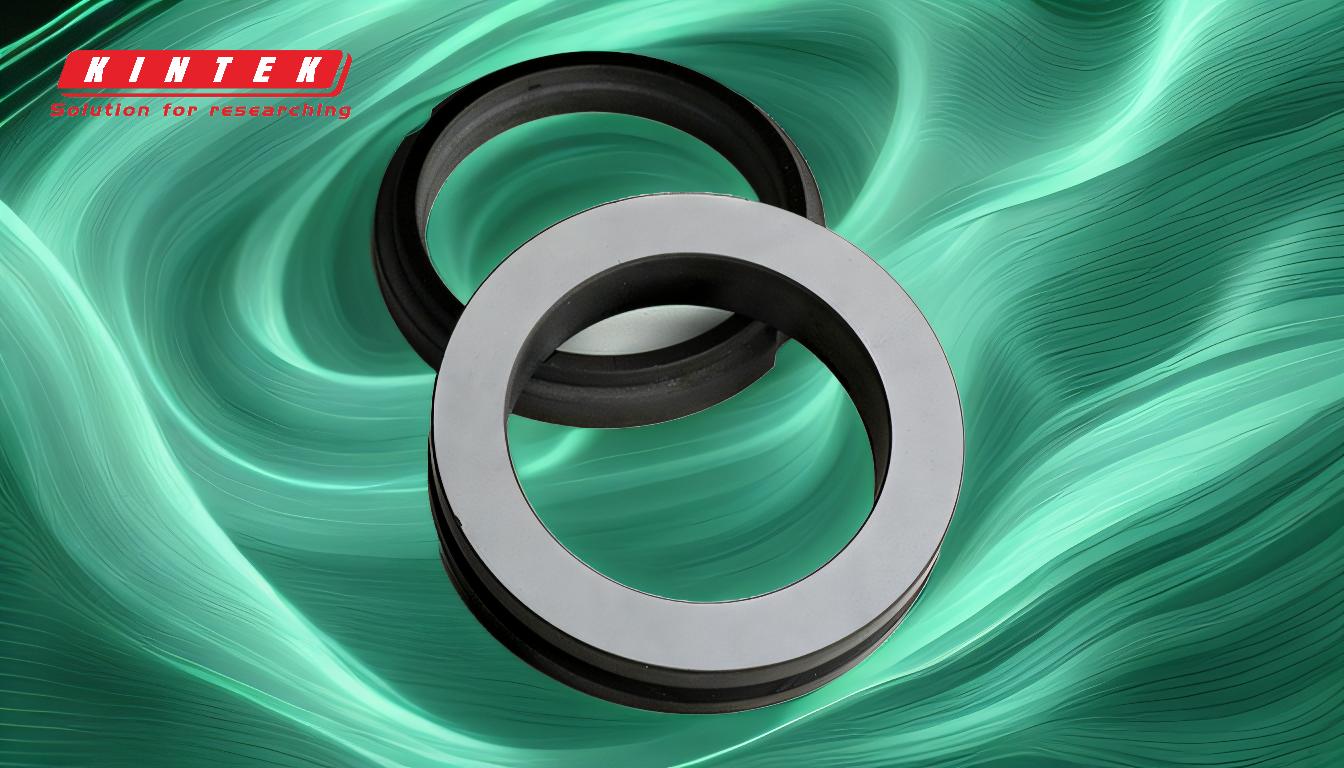
-
Overview of CVD Process:
- CVD involves the deposition of thin films through chemical reactions in the vapor phase. The process begins with the vaporization of a precursor material, which is then transported to the substrate surface.
- The precursor undergoes decomposition or reacts with other gases, vapors, or liquids at the substrate surface, forming a solid film and releasing gaseous by-products.
-
Key Steps in CVD:
- Transport of Reacting Species: The precursor gas is transported to the substrate surface, often facilitated by a carrier gas.
- Adsorption: The gas molecules adsorb onto the substrate surface.
- Surface Reactions: Chemical reactions occur on the substrate surface, leading to the formation of a solid film.
- Desorption and Removal of By-products: Gaseous reaction products are desorbed from the surface and removed from the chamber.
-
Types of CVD Methods:
- Chemical Transport Method: Involves the transport of a solid material in the form of a volatile compound, which decomposes on the substrate.
- Pyrolysis Method: The precursor is thermally decomposed on the substrate surface without the need for additional reactants.
- Synthesis Reaction Method: Involves the reaction of two or more precursor gases to form the desired material on the substrate.
-
Key Parameters in CVD:
- Chamber Pressure: Affects the rate of deposition and the quality of the film. Low-pressure CVD (LPCVD) and atmospheric pressure CVD (APCVD) are common variants.
- Substrate Temperature: Influences the rate of chemical reactions and the crystallinity of the deposited film.
- Precursor Materials: The choice of precursor determines the type of material that can be deposited, ranging from metals to semiconductors.
-
Advantages of CVD:
- Versatility: CVD can deposit a wide variety of materials, including metals, ceramics, and polymers.
- Conformality: The process provides excellent step coverage, making it suitable for coating complex geometries.
- High Purity and Density: CVD films are typically of high purity and density, with low residual stress.
- Controlled Properties: By adjusting deposition parameters, the properties of the deposited film, such as thickness and composition, can be precisely controlled.
-
Applications of CVD:
- Semiconductor Manufacturing: CVD is widely used in the production of integrated circuits, where it is used to deposit thin films of silicon, silicon dioxide, and other materials.
- Protective Coatings: CVD is used to apply protective coatings to tools and components, enhancing their durability and resistance to wear and corrosion.
- Optoelectronics: CVD is employed in the production of optoelectronic devices, such as LEDs and solar cells, where it is used to deposit thin films of materials like gallium nitride and indium tin oxide.
-
Equipment and Maintenance:
- CVD equipment is relatively simple and easy to operate, with minimal maintenance requirements. The process can be automated, allowing for consistent and repeatable results.
In summary, chemical vapor deposition is a highly versatile and controllable process for depositing thin films of materials onto substrates. By understanding the key steps, parameters, and advantages of CVD, one can effectively utilize this technique for a wide range of applications, from semiconductor manufacturing to protective coatings.
Summary Table:
Aspect | Details |
---|---|
Key Steps | Transport, Adsorption, Surface Reactions, Desorption & By-product Removal |
Types of CVD | Chemical Transport, Pyrolysis, Synthesis Reaction |
Key Parameters | Chamber Pressure, Substrate Temperature, Precursor Materials |
Advantages | Versatility, Conformality, High Purity & Density, Controlled Properties |
Applications | Semiconductor Manufacturing, Protective Coatings, Optoelectronics |
Ready to optimize your thin film deposition process? Contact our experts today for tailored CVD solutions!