Calcination and roasting are high-temperature processes used in industrial and laboratory settings, primarily carried out in specific types of furnaces. The reverberatory furnace is the most commonly used furnace for these processes, as it is designed to handle the high temperatures and uniform heating required for calcination and roasting. Other furnace types, such as muffle, shaft, and kiln furnaces, are also used depending on the specific application and temperature requirements. These furnaces can be powered by electricity, gas, or oil, depending on the operational needs. The choice of furnace depends on factors such as the material being processed, temperature uniformity, and the scale of the operation.
Key Points Explained:
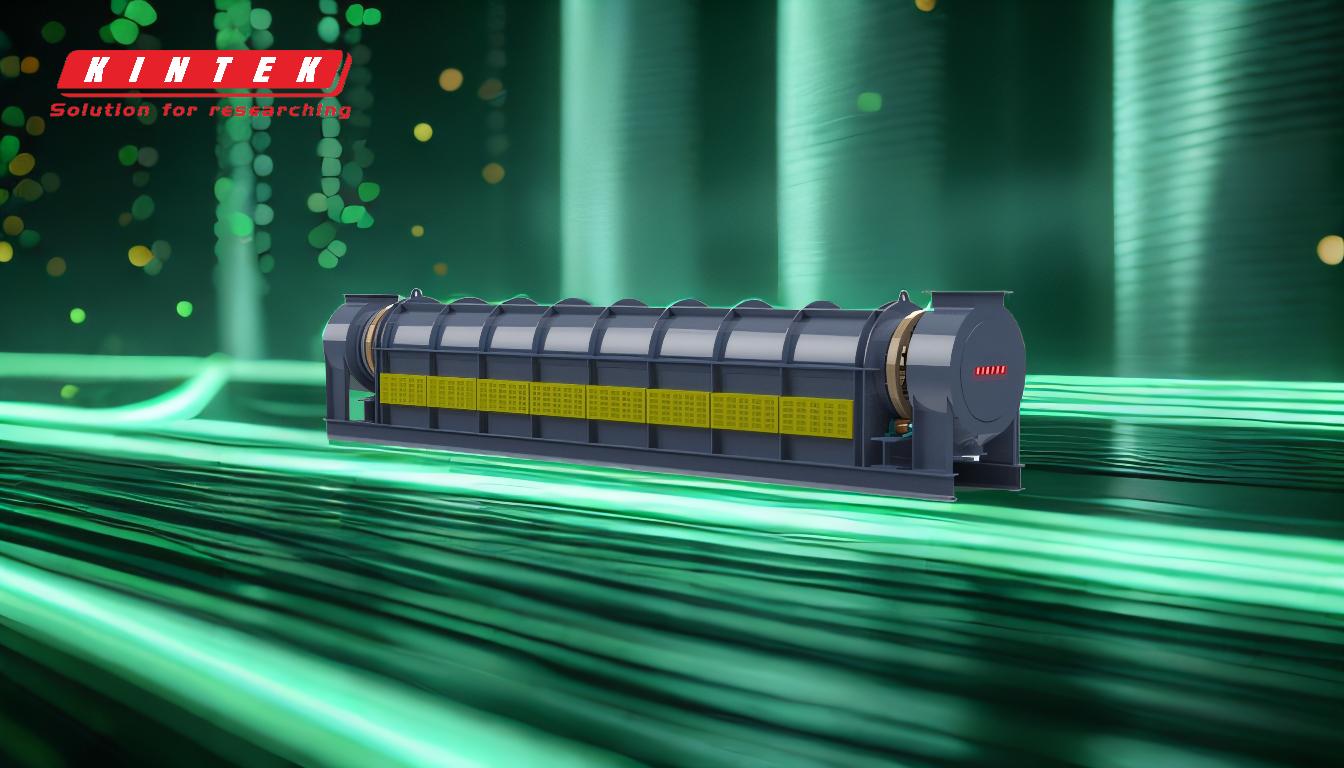
-
Reverberatory Furnace for Calcination and Roasting:
- The reverberatory furnace is the primary furnace used for calcination and roasting. It is designed to provide uniform heating and can withstand the high temperatures required for these processes.
- Calcination involves heating a substance to high temperatures in the absence or limited supply of air to induce thermal decomposition, while roasting involves heating in the presence of excess air to oxidize or reduce the material.
-
Other Types of Furnaces Used:
- Muffle Furnaces: These are enclosed furnaces that isolate the material from direct contact with the heating elements, making them suitable for processes requiring controlled atmospheres.
- Shaft Furnaces and Kilns: These are vertical furnaces used for continuous processing of materials, often in large-scale industrial applications.
- Tube Furnaces and Vacuum Furnaces: These are used for specialized high-temperature applications, such as sintering or melting, where precise temperature control is required.
-
Fuel Sources for Calcination Furnaces:
- Calcination furnaces can be powered by electricity, gas, or oil, depending on the specific requirements of the application. The choice of fuel source affects the furnace's efficiency, cost, and environmental impact.
-
Temperature Uniformity and Heating Elements:
- High-temperature furnaces, including those used for calcination and roasting, are equipped with strategically positioned heating elements to ensure temperature uniformity. This is critical for achieving consistent results in processes like fusion, sintering, and melting.
-
Industrial vs. Laboratory Furnaces:
- Industrial furnaces are typically larger and designed for continuous operation, while laboratory furnaces are smaller and used for research and development purposes. Both types must meet specific temperature and application requirements.
-
Applications of Calcination and Roasting:
- Calcination is commonly used in the production of cement, lime, and ceramics, while roasting is used in metallurgy to extract metals from ores. The choice of furnace depends on the material being processed and the desired outcome.
By understanding the types of furnaces and their applications, purchasers can make informed decisions based on the specific needs of their processes, such as temperature requirements, scale, and fuel efficiency.
Summary Table:
Furnace Type | Key Features | Applications |
---|---|---|
Reverberatory Furnace | Uniform heating, high-temperature resistance | Calcination, roasting, cement, lime, and ceramics production |
Muffle Furnace | Controlled atmosphere, isolation from heating elements | Processes requiring precise temperature control and contamination-free environments |
Shaft Furnace/Kiln | Vertical design, continuous processing | Large-scale industrial applications like metal extraction and material processing |
Tube/Vacuum Furnace | Precise temperature control, specialized high-temperature applications | Sintering, melting, and advanced material research |
Need help choosing the right furnace for your calcination or roasting process? Contact our experts today for personalized advice!