Vacuum heat treatment is a highly effective method for improving the quality and performance of metal alloys. One of its key advantages is the significant reduction in scaling and decarburization, which are common issues in traditional heat treatment processes. By conducting the heat treatment in a vacuum environment, the process eliminates exposure to air, preventing oxidation and chemical reactions that lead to scaling and decarburization. This results in superior surface quality, enhanced mechanical properties, and longer-lasting materials. Additionally, vacuum heat treatment offers benefits such as improved safety, reduced deformation, and better overall control over the treatment process, making it a preferred choice for industries requiring high precision and durability.
Key Points Explained:
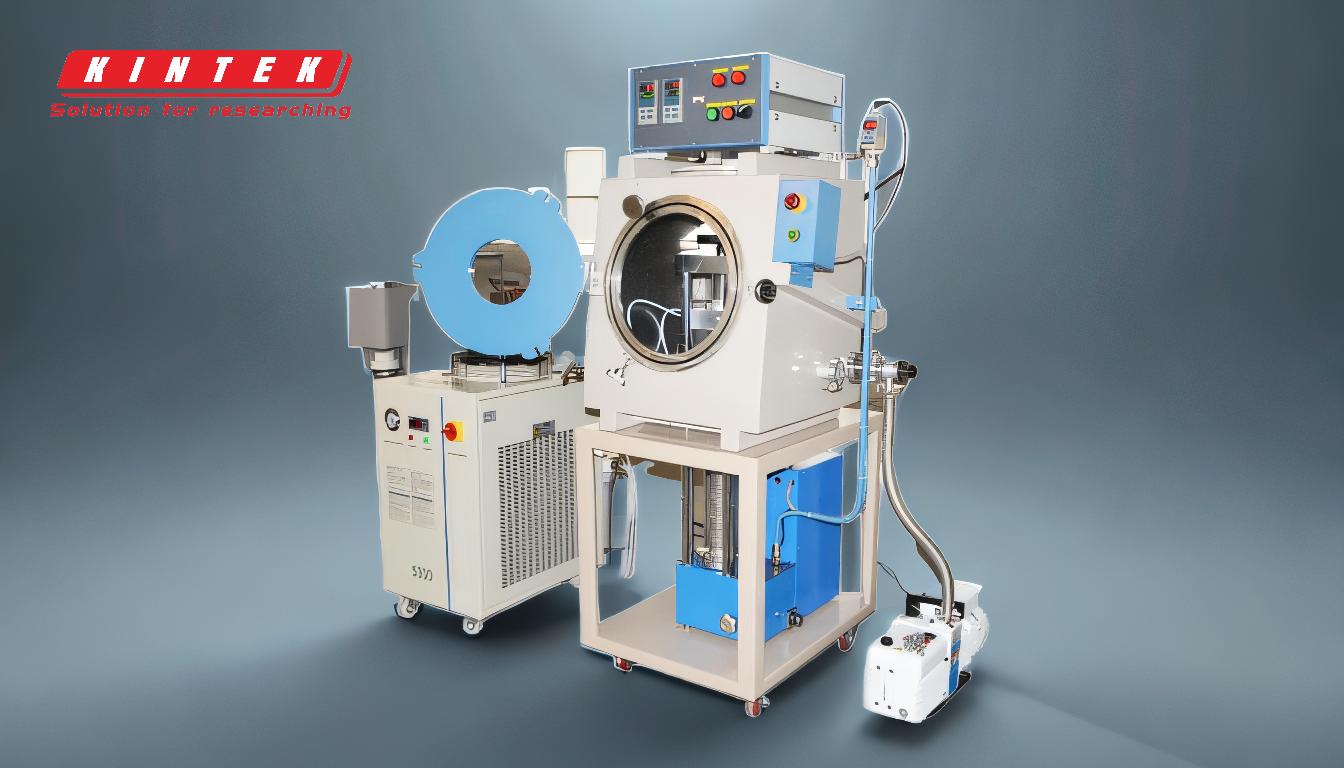
-
Reduced Scaling and Decarburization:
- Scaling and decarburization occur when metal surfaces react with oxygen or other reactive elements during heat treatment, leading to surface degradation and loss of carbon content. In vacuum heat treatment, the absence of air in the vacuum chamber prevents these reactions, ensuring that the metal retains its surface integrity and carbon content. This results in a bright, purified surface and preserves the mechanical properties of the material.
-
Prevention of Oxidation:
- Oxidation is a common issue in traditional heat treatment methods, where metal surfaces react with oxygen, leading to discoloration and surface damage. Vacuum heat treatment eliminates this problem by creating an oxygen-free environment. This ensures that the metal retains its desired finish and avoids unsightly marks or damage.
-
Improved Mechanical Properties:
- By preventing oxidation and decarburization, vacuum heat treatment enhances the hardness, strength, and wear resistance of metals. The process also minimizes thermal stress and deformation, resulting in materials with superior dimensional stability and durability. This makes vacuum heat-treated metals ideal for applications requiring high performance and longevity.
-
Enhanced Surface Quality:
- The vacuum environment not only prevents scaling and decarburization but also removes impurities such as phosphorus chips and degreases the surface. This leads to a bright, purified finish that is free from contaminants, improving the overall surface quality of the workpiece.
-
Safety and Environmental Benefits:
- Vacuum heat treatment is safer than traditional methods because it does not use flammable gases or produce harmful contaminants. The process is pollution-free and complies with OSHA standards, ensuring a safer working environment for employees.
-
Controlled Heating and Cooling:
- The slow and controlled heating process in a vacuum furnace minimizes internal thermal differences and reduces thermal stress. This results in smaller deformations and higher-quality products, making vacuum heat treatment ideal for precision components.
-
Versatility and Efficiency:
- Vacuum heat treatment is suitable for a wide range of metals and alloys, offering consistent and predictable results. The process also eliminates the need for additional cleaning or surface treatment, saving time and resources in manufacturing.
In summary, vacuum heat treatment provides a comprehensive solution for reducing scaling and decarburization while improving the overall quality and performance of metal alloys. Its ability to prevent oxidation, enhance mechanical properties, and ensure safety makes it a superior choice for industries requiring high precision and durability.
Summary Table:
Advantages of Vacuum Heat Treatment | Key Benefits |
---|---|
Reduced Scaling and Decarburization | Prevents surface degradation and carbon loss |
Prevention of Oxidation | Eliminates discoloration and surface damage |
Improved Mechanical Properties | Enhances hardness, strength, and wear resistance |
Enhanced Surface Quality | Bright, purified finish free from contaminants |
Safety and Environmental Benefits | Pollution-free and OSHA-compliant process |
Controlled Heating and Cooling | Minimizes thermal stress and deformation |
Versatility and Efficiency | Suitable for a wide range of metals and alloys |
Unlock the full potential of vacuum heat treatment for your materials—contact our experts today!