Induction heating is generally more efficient than resistance heating due to its direct energy transfer mechanism, which minimizes energy loss. It can be up to 50% more efficient, significantly reducing power consumption and heating time. Additionally, induction heating does not produce waste emissions, making it environmentally friendly. This method allows for precise temperature control and faster heating, which further enhances its efficiency and cost-effectiveness in industrial applications.
Key Points Explained:
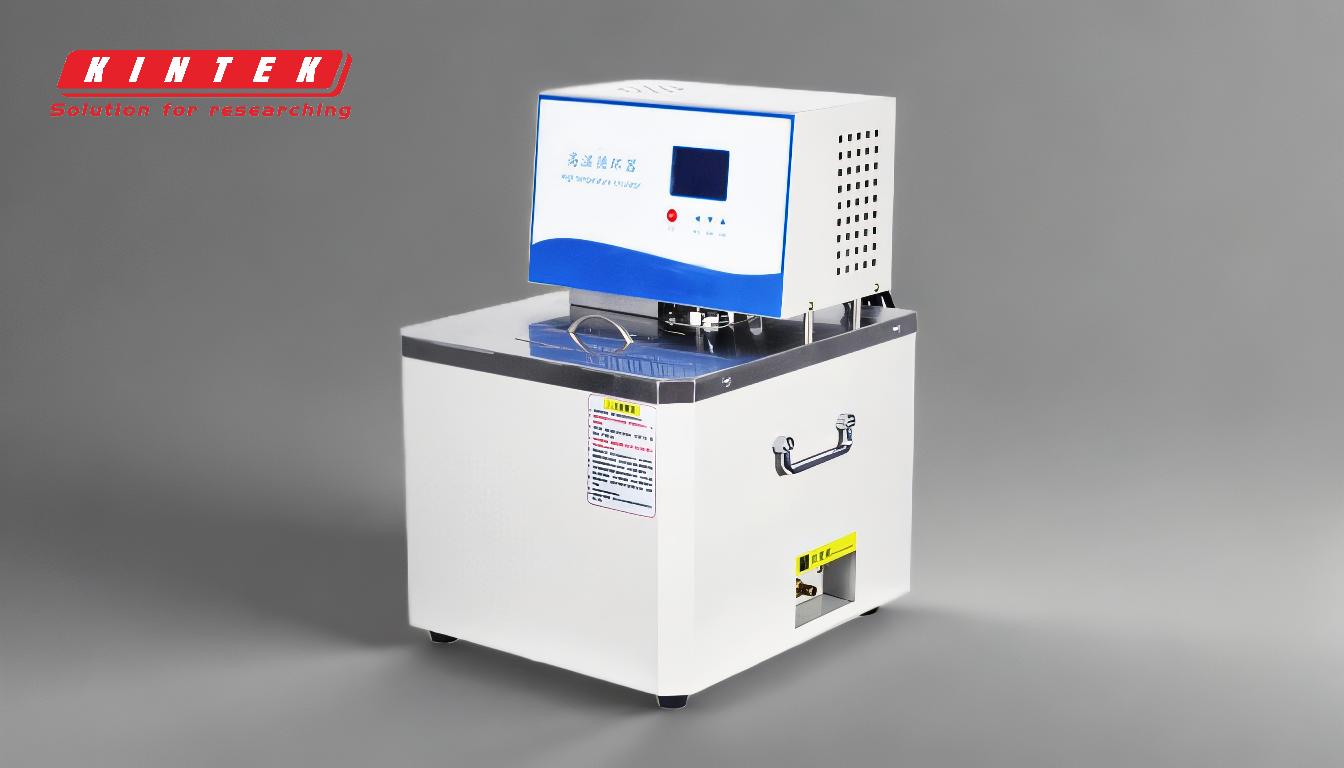
-
Energy Efficiency of Induction Heating:
- Induction heating is more energy-efficient compared to resistance heating because it directly transfers energy to the material being heated, reducing energy loss.
- Studies and practical applications show that induction heating can be up to 50% more efficient than traditional resistance heating methods.
-
Reduction in Heating Time:
- Induction heating can shorten the heating time by more than 50% compared to resistance heating. This is due to the rapid and direct heating mechanism of induction, which allows for quicker temperature rise in the material.
-
Energy Savings:
- The efficiency of induction heating translates into significant energy savings, often achieving at least a 30% reduction in energy consumption. This not only lowers operational costs but also contributes to a smaller carbon footprint.
-
Environmental Benefits:
- Unlike resistance heating, induction heating does not produce any waste emissions. This makes it an environmentally friendly option, addressing both ecological and security concerns effectively.
-
Precision and Control:
- Induction heating offers superior control over the heating process, allowing for precise temperature adjustments. This precision ensures that the material is heated uniformly and efficiently, further enhancing the overall energy efficiency.
-
Cost-Effectiveness:
- The combination of reduced energy consumption, faster heating times, and lower maintenance requirements makes induction heating a cost-effective solution for various industrial applications.
In summary, induction heating surpasses resistance heating in terms of energy efficiency, speed, environmental impact, and cost-effectiveness, making it a superior choice for many heating applications.
Summary Table:
Aspect | Induction Heating | Resistance Heating |
---|---|---|
Energy Efficiency | Up to 50% more efficient | Less efficient |
Heating Time | 50% faster | Slower |
Energy Savings | At least 30% reduction in consumption | Higher energy usage |
Environmental Impact | No waste emissions | Produces waste emissions |
Precision & Control | Superior temperature control | Less precise |
Cost-Effectiveness | Lower operational and maintenance costs | Higher costs |
Upgrade your heating process with induction technology—contact our experts today to learn more!