PVD (Physical Vapor Deposition) coatings are indeed strong and durable, making them highly suitable for a wide range of industrial applications. They are characterized by their high hardness, wear resistance, corrosion resistance, and low friction properties. These coatings are typically very thin, ranging from 0.5 to 5 microns, yet they provide excellent adhesion to the substrate and can replicate the original finish of materials with minimal effort. PVD coatings are harder and more corrosion-resistant than many other coating methods, such as electroplating, and they often eliminate the need for additional protective topcoats. Their high temperature and impact strength, along with excellent abrasion resistance, make them ideal for use in demanding environments, including automotive, aerospace, and medical industries.
Key Points Explained:
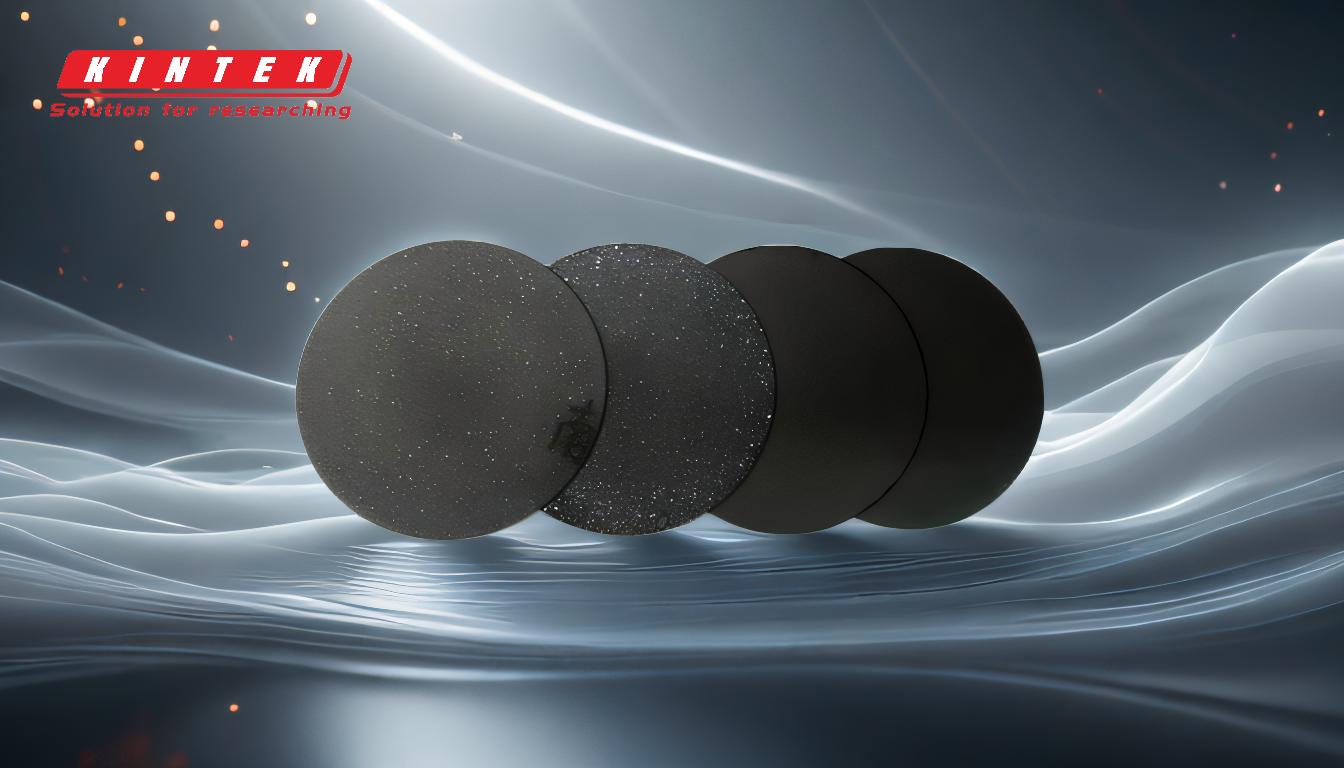
-
High Hardness and Wear Resistance:
- PVD coatings are known for their exceptional hardness, which significantly enhances their wear resistance. This makes them ideal for applications where durability and longevity are critical, such as cutting tools, molds, and automotive components.
- The hardness of PVD coatings often exceeds that of traditional coatings like electroplating, making them more durable under high-stress conditions.
-
Corrosion and Oxidation Resistance:
- PVD coatings provide excellent resistance to corrosion and oxidation, which is crucial for components exposed to harsh environments, such as those in the aerospace and marine industries.
- This resistance helps in maintaining the integrity and functionality of the coated parts over extended periods, even in corrosive or high-temperature environments.
-
Low Friction Properties:
- The low friction characteristics of PVD coatings reduce wear and tear on moving parts, leading to improved efficiency and longer service life for components like bearings, gears, and sliding parts.
- This property is particularly beneficial in reducing energy consumption and minimizing maintenance requirements.
-
Thin and Uniform Coatings:
- PVD coatings are very thin, typically ranging from 0.5 to 5 microns, which allows them to replicate the original finish of materials with minimal effort.
- Despite their thinness, these coatings are difficult to remove and provide excellent adhesion to the substrate, ensuring long-lasting performance.
-
High Temperature and Impact Strength:
- PVD coatings exhibit high temperature and impact strength, making them suitable for applications that involve extreme thermal and mechanical stresses.
- This property is particularly valuable in industries like aerospace and automotive, where components are often subjected to high temperatures and mechanical impacts.
-
Aesthetic and Functional Benefits:
- PVD coatings not only enhance the functional properties of materials but also improve their aesthetic appearance. They can provide a metallic luster without the need for additional polishing.
- This dual benefit makes PVD coatings attractive for both industrial and decorative applications.
-
Substrate-Dependent Properties:
- The performance of PVD coatings can vary depending on the underlying substrate material. For example, a TiN coating on Ti-6Al-4V alloy can increase the fatigue limit by 22% and endurance by 7%.
- This substrate dependency allows for tailored solutions that meet specific performance requirements in different applications.
-
Limitations and Considerations:
- While PVD coatings offer numerous advantages, they do have some limitations. For instance, they may have poor coating performance on the back and sides of tools due to low air pressure during the coating process.
- Additionally, the high cleaning requirements and relatively low temperatures used in PVD processes can be challenging in certain applications.
In summary, PVD coatings are strong and durable, offering a combination of high hardness, wear resistance, corrosion resistance, and low friction properties. These characteristics make them highly suitable for a wide range of industrial applications, particularly in demanding environments. However, it is important to consider the specific requirements and limitations of PVD coatings to ensure optimal performance in each application.
Summary Table:
Property | Description |
---|---|
High Hardness | Exceptional hardness enhances wear resistance, ideal for cutting tools and molds. |
Corrosion Resistance | Excellent resistance to harsh environments, ensuring long-term functionality. |
Low Friction | Reduces wear on moving parts, improving efficiency and reducing maintenance. |
Thin & Uniform Coatings | 0.5 to 5 microns thick, replicates original finish with excellent adhesion. |
High Temp & Impact Strength | Withstands extreme thermal and mechanical stresses, ideal for aerospace and automotive. |
Aesthetic Benefits | Provides metallic luster without additional polishing, enhancing appearance. |
Substrate-Dependent | Performance varies with substrate material, allowing tailored solutions. |
Limitations | Poor coating on tool backs/sides, high cleaning requirements, and low temps. |
Unlock the full potential of PVD coatings for your industry—contact our experts today to learn more!