Quenching and tempering, and annealing are both heat treatment processes used to alter the mechanical properties of metals, but they are not the same. Quenching involves rapidly cooling a metal to increase its hardness and strength, while tempering is a subsequent process that reduces brittleness by reheating the quenched metal to a lower temperature. Annealing, on the other hand, involves heating the metal to a specific temperature and then slowly cooling it to soften the material, improve ductility, and relieve internal stresses. Each process serves different purposes and results in distinct material properties.
Key Points Explained:
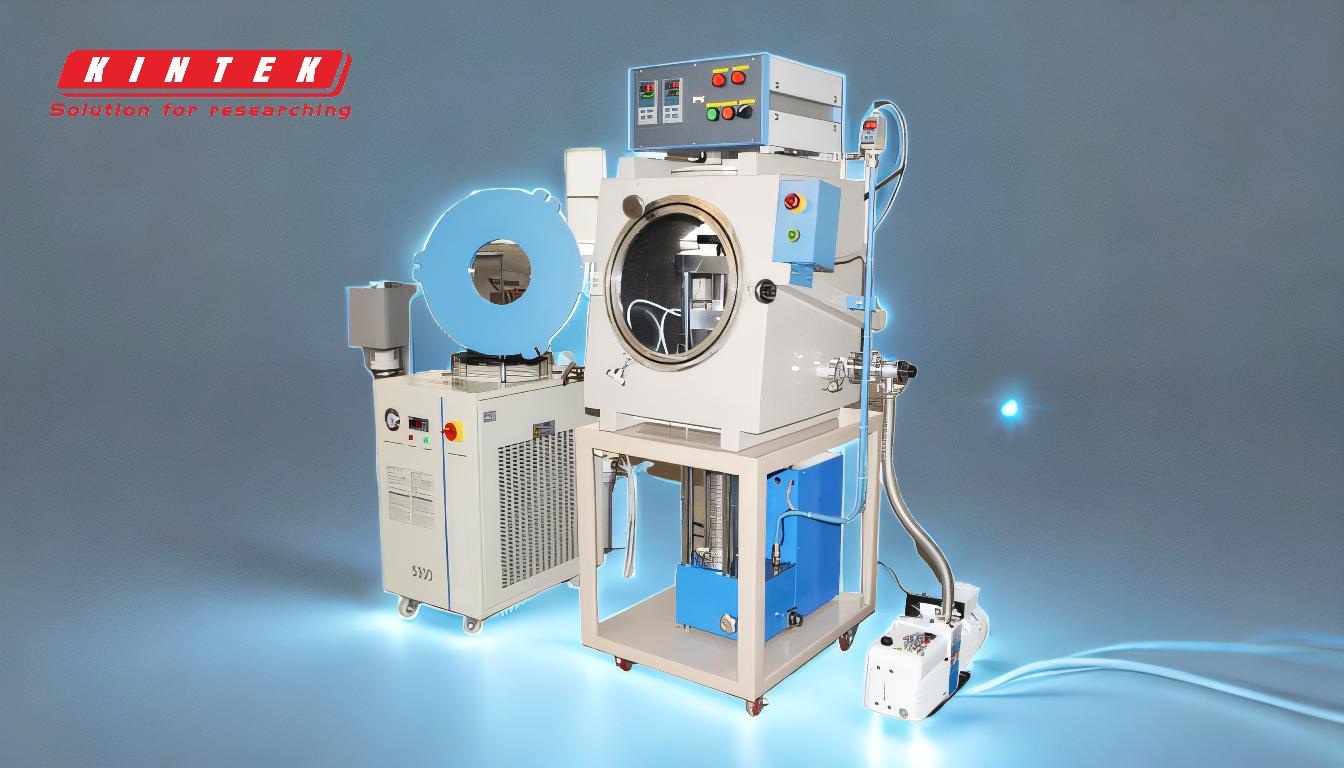
-
Quenching and Tempering Process:
- Quenching: This process involves heating the metal to a high temperature and then rapidly cooling it, usually in water, oil, or air. The rapid cooling locks the metal's microstructure in a harder state, increasing its strength and hardness. However, this also makes the metal more brittle.
- Tempering: After quenching, the metal is often too brittle for practical use. Tempering involves reheating the quenched metal to a temperature below its critical point and then cooling it slowly. This process reduces brittleness while maintaining much of the hardness and strength gained from quenching.
-
Annealing Process:
- Heating: The metal is heated to a specific temperature, which varies depending on the type of metal and the desired properties. This temperature is typically above the metal's recrystallization temperature but below its melting point.
- Soaking: The metal is held at this temperature for a period of time to allow the microstructure to fully transform.
- Slow Cooling: The metal is then slowly cooled, often in the furnace itself, to room temperature. This slow cooling allows the metal to soften, improve ductility, and relieve internal stresses.
-
Purpose and Outcomes:
- Quenching and Tempering: The primary goal is to increase the hardness and strength of the metal while reducing brittleness. This process is commonly used for tools, gears, and other components that require high strength and wear resistance.
- Annealing: The main objective is to soften the metal, improve its ductility, and relieve internal stresses. This makes the metal easier to machine, form, or weld. Annealing is often used for materials that will undergo further processing or for components that need to withstand deformation without cracking.
-
Microstructural Changes:
- Quenching and Tempering: Quenching results in a martensitic structure, which is very hard but brittle. Tempering then transforms some of the martensite into tempered martensite, which is less brittle but still strong.
- Annealing: Annealing results in a more refined and uniform grain structure, which improves the metal's ductility and reduces hardness. The process can also lead to the formation of pearlite or spheroidite, depending on the cooling rate and the type of metal.
-
Applications:
- Quenching and Tempering: This process is typically used for high-strength applications such as automotive parts, construction equipment, and cutting tools.
- Annealing: Annealing is used for applications where ductility and ease of machining are more important than hardness, such as in the production of sheet metal, wires, and components that will be cold-worked or welded.
In summary, while both quenching and tempering and annealing are heat treatment processes, they serve different purposes and result in different material properties. Quenching and tempering are used to increase hardness and strength while reducing brittleness, whereas annealing is used to soften the metal, improve ductility, and relieve internal stresses.
Summary Table:
Aspect | Quenching and Tempering | Annealing |
---|---|---|
Process | Rapid cooling (quenching) followed by reheating (tempering) to reduce brittleness. | Heating to a specific temperature followed by slow cooling. |
Purpose | Increases hardness and strength while reducing brittleness. | Softens metal, improves ductility, and relieves internal stresses. |
Microstructure | Forms martensite (hard but brittle), tempered to tempered martensite (less brittle). | Refines grain structure, forming pearlite or spheroidite. |
Applications | Automotive parts, construction equipment, cutting tools. | Sheet metal, wires, components for cold-working or welding. |
Need help choosing the right heat treatment process for your materials? Contact our experts today!