Batch furnaces are versatile tools widely used in industries and laboratories for various high-temperature processes. They are particularly well-suited for applications requiring precise temperature control, uniform heating, and specific atmospheric conditions. Common uses include annealing, sintering, heat treatment, and material synthesis. Batch furnaces are ideal for processes where samples or materials need to be processed in controlled environments, such as inert or vacuum atmospheres, to prevent oxidation or contamination. Their design allows for efficient handling of small to medium-sized batches, making them a preferred choice for research, development, and production in fields like materials science, metallurgy, and electronics.
Key Points Explained:
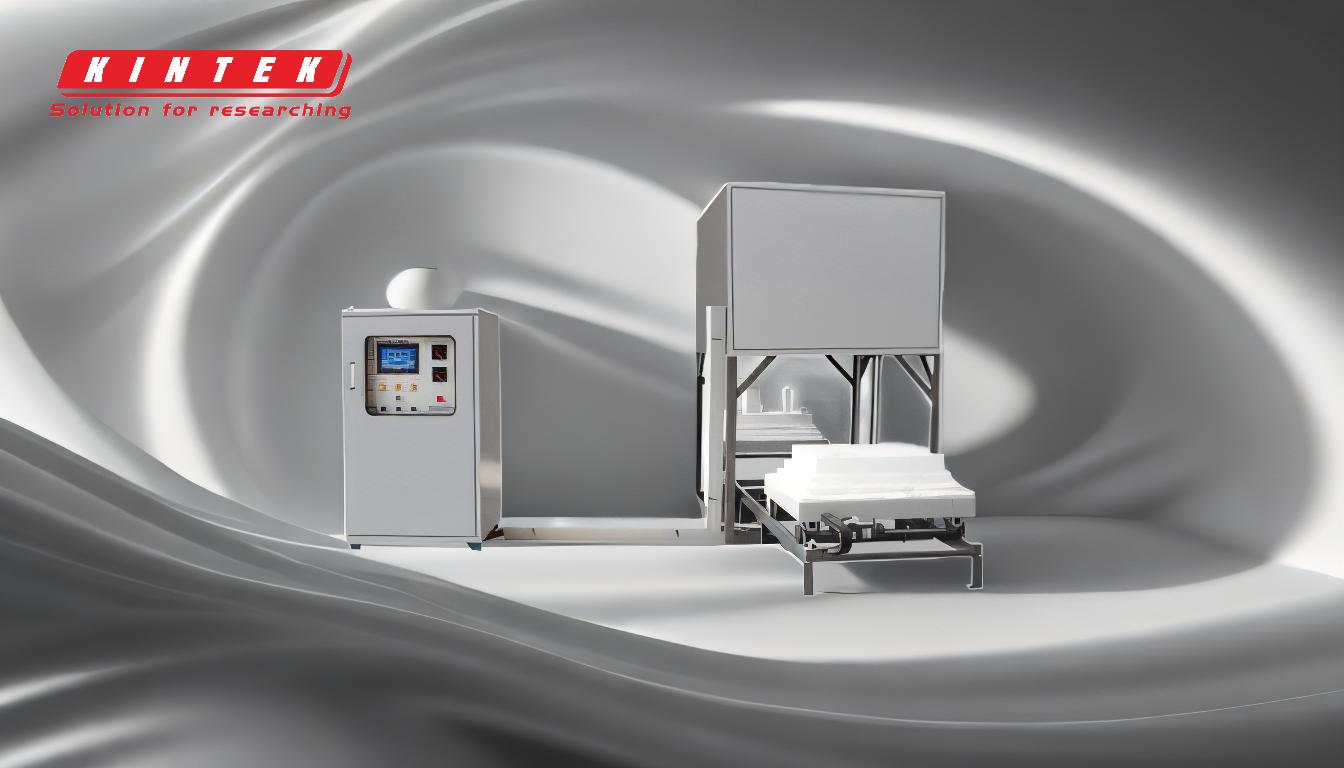
-
Versatility in Applications:
- Batch furnaces are used for a wide range of processes, including annealing, sintering, hardening, and heat treatment. These processes are essential in industries like materials science, metallurgy, and electronics manufacturing.
- They are also employed in specialized tasks such as thermal decomposition, pyrolysis, and chemical vapor deposition (CVD), which are critical in nanotechnology and materials research.
-
Precise Temperature Control:
- One of the key advantages of batch furnaces is their ability to maintain precise and uniform temperatures. This is crucial for processes like annealing and sintering, where consistent heating is required to achieve desired material properties.
- The ability to control temperature gradients ensures that samples are heated evenly, reducing the risk of defects or inconsistencies in the final product.
-
Controlled Atmospheres:
- Batch furnaces can operate in various atmospheres, including inert, vacuum, and reactive environments. This flexibility is vital for processes that require protection from oxidation or contamination.
- For example, in vacuum metallurgy, batch furnaces are used to melt alloys and special steels, ensuring high-quality results in aerospace and electronics applications.
-
Batch Processing Efficiency:
- Batch furnaces are designed to handle small to medium-sized batches, making them ideal for laboratory settings and small-scale production. This allows for efficient processing of multiple samples or materials simultaneously.
- The batch design also facilitates easy loading and unloading of materials, reducing downtime and increasing productivity.
-
Material Compatibility:
- Batch furnaces are compatible with a wide range of materials, including metals, ceramics, and composites. This makes them suitable for diverse applications, from heat-treating steel to sintering ceramic components.
- Their ability to process different materials under controlled conditions makes batch furnaces a valuable tool in research and development.
-
Industry-Specific Applications:
- In the electronics industry, batch furnaces are used for processes like thin film deposition and crystal growth, which are essential for manufacturing semiconductors and other electronic components.
- In materials science, they are employed for tasks such as calcining and heat treatment, enabling the development of advanced materials with tailored properties.
By combining precise temperature control, versatile atmospheric conditions, and efficient batch processing, batch furnaces are indispensable tools in both industrial and laboratory settings. Their ability to handle a wide range of materials and processes makes them a preferred choice for high-temperature applications requiring accuracy and reliability.
Summary Table:
Key Feature | Application |
---|---|
Versatility | Annealing, sintering, hardening, heat treatment, material synthesis |
Precise Temperature | Uniform heating for consistent material properties |
Controlled Atmospheres | Inert, vacuum, or reactive environments for oxidation-free processes |
Batch Processing | Efficient handling of small to medium-sized batches for labs and production |
Material Compatibility | Metals, ceramics, composites for diverse applications |
Industry-Specific Uses | Electronics (thin film deposition), materials science (calcining, heat treatment) |
Ready to enhance your high-temperature processes? Contact us today to find the perfect batch furnace for your needs!