Low temperature brazing alloys are specialized materials used to join metals at temperatures significantly lower than those required for traditional brazing. These alloys typically melt at temperatures below 450°C (842°F), making them ideal for applications where high heat could damage sensitive components. They are commonly used in industries such as electronics, automotive, and HVAC systems. The alloys often contain elements like tin, lead, cadmium, zinc, and indium, which contribute to their low melting points and good wetting properties. Understanding their composition, properties, and applications is crucial for selecting the right alloy for specific joining tasks.
Key Points Explained:
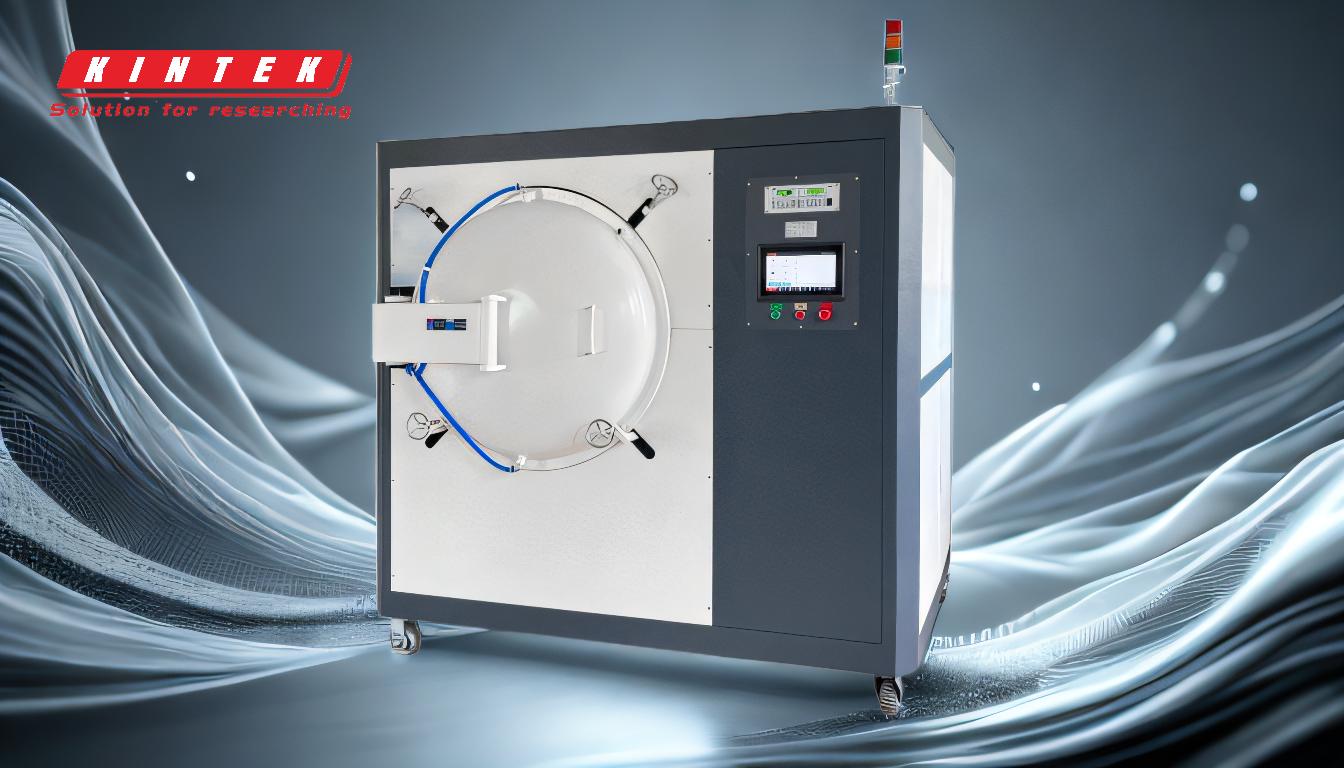
-
Definition and Characteristics of Low Temperature Brazing Alloys:
- Low temperature brazing alloys are designed to melt at temperatures below 450°C (842°F), which is significantly lower than traditional brazing alloys that often require temperatures above 600°C (1112°F).
- These alloys are typically composed of metals like tin, lead, cadmium, zinc, and indium, which have relatively low melting points.
- They exhibit excellent wetting properties, meaning they can spread evenly over the surfaces to be joined, ensuring strong and reliable bonds.
-
Common Types of Low Temperature Brazing Alloys:
- Tin-Lead Alloys: These are among the most widely used low temperature brazing alloys. They offer good wetting properties and are relatively easy to work with. However, due to environmental and health concerns, the use of lead is being phased out in many applications.
- Cadmium-Based Alloys: Cadmium alloys are known for their excellent strength and corrosion resistance. However, cadmium is toxic, and its use is increasingly restricted.
- Indium-Based Alloys: Indium alloys are used in applications requiring very low melting points and excellent thermal conductivity. They are often used in electronics and cryogenic applications.
- Zinc-Based Alloys: These alloys are used in applications where higher strength is required, and they are often used in the automotive industry.
-
Applications of Low Temperature Brazing Alloys:
- Electronics: In the electronics industry, low temperature brazing alloys are used to join components without damaging sensitive parts. They are particularly useful in the assembly of printed circuit boards (PCBs) and semiconductor devices.
- Automotive: These alloys are used in the assembly of various automotive components, including radiators, air conditioning systems, and fuel lines, where high heat could damage plastic or rubber parts.
- HVAC Systems: In heating, ventilation, and air conditioning systems, low temperature brazing alloys are used to join copper and aluminum components, ensuring leak-free connections.
- Medical Devices: The medical industry uses these alloys in the assembly of devices where biocompatibility and precision are critical.
-
Advantages of Low Temperature Brazing Alloys:
- Reduced Thermal Stress: By operating at lower temperatures, these alloys minimize the risk of thermal damage to the components being joined, which is particularly important for delicate or heat-sensitive materials.
- Energy Efficiency: Lower brazing temperatures translate to lower energy consumption, making the process more cost-effective and environmentally friendly.
- Versatility: Low temperature brazing alloys can be used with a wide range of materials, including dissimilar metals, which is not always possible with traditional brazing methods.
- Ease of Use: These alloys often require less sophisticated equipment and can be applied using simpler techniques, making them accessible for a variety of applications.
-
Considerations for Selecting Low Temperature Brazing Alloys:
- Material Compatibility: It is essential to choose an alloy that is compatible with the materials being joined. For example, some alloys may not adhere well to certain metals or may cause galvanic corrosion.
- Environmental and Health Concerns: The presence of toxic elements like lead and cadmium in some alloys necessitates careful handling and disposal. Regulatory restrictions may also limit the use of certain alloys.
- Mechanical Properties: The strength, ductility, and thermal conductivity of the alloy should match the requirements of the application. For instance, indium-based alloys are preferred in cryogenic applications due to their excellent thermal properties.
- Cost: The cost of the alloy and the brazing process should be considered, especially for large-scale applications. While some alloys may be more expensive, their performance benefits may justify the higher cost.
-
Future Trends in Low Temperature Brazing Alloys:
- Development of Lead-Free Alloys: As environmental regulations become stricter, there is a growing demand for lead-free brazing alloys. Research is focused on developing alloys with comparable performance using safer materials.
- Nanotechnology: The incorporation of nanoparticles into brazing alloys is being explored to enhance their properties, such as strength and thermal conductivity, without increasing the melting temperature.
- Sustainability: There is an increasing emphasis on developing sustainable brazing alloys that are not only environmentally friendly but also derived from renewable or recycled materials.
In conclusion, low temperature brazing alloys play a crucial role in modern manufacturing and assembly processes, offering a combination of low melting points, excellent wetting properties, and versatility. Understanding their composition, properties, and applications is essential for selecting the right alloy for specific joining tasks, ensuring strong, reliable, and efficient bonds.
Summary Table:
Aspect | Details |
---|---|
Melting Point | Below 450°C (842°F) |
Common Elements | Tin, lead, cadmium, zinc, indium |
Key Applications | Electronics, automotive, HVAC systems, medical devices |
Advantages | Reduced thermal stress, energy efficiency, versatility, ease of use |
Selection Considerations | Material compatibility, environmental concerns, mechanical properties, cost |
Need the perfect low temperature brazing alloy for your project? Contact our experts today for tailored solutions!