Sintered products are materials that have undergone the sintering process, a method of compacting and forming a solid mass by applying heat or pressure without melting the material to the point of liquefaction. This process allows the atoms in the material to diffuse across particle boundaries, fusing them into a single, dense piece. Sintering is widely used across various industries due to its ability to produce complex shapes, maintain material purity, and offer cost-effective production with minimal waste. It is particularly beneficial for materials with high melting points, such as tungsten and molybdenum, as well as for ceramics, metals, and polymers. The resulting sintered products exhibit excellent surface finishes, good performance properties, and precise tolerance control, making them suitable for applications ranging from small components like gears and pulleys to high-temperature components like bearings and filters.
Key Points Explained:
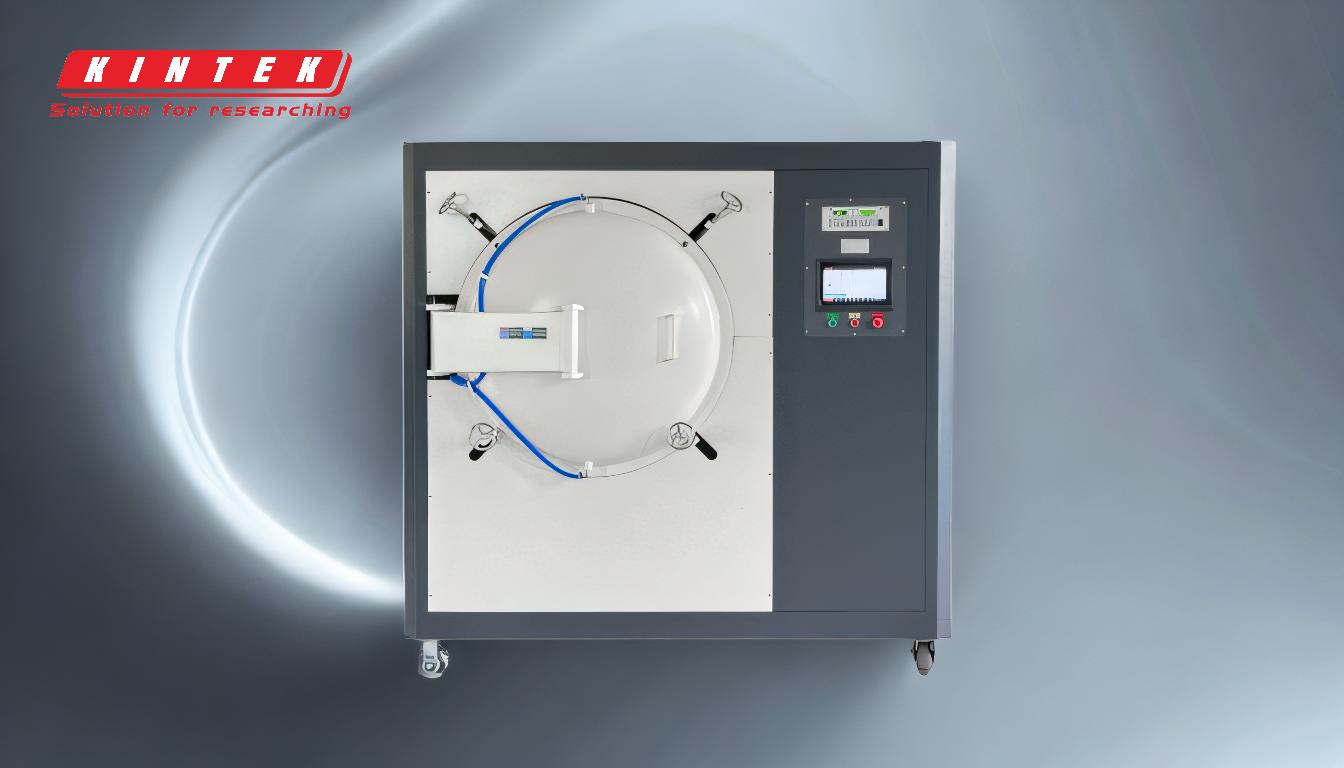
-
Definition of Sintering:
- Sintering is a process that compacts and forms solid materials by applying heat or pressure without melting the material to its liquefaction point. This allows atoms to diffuse across particle boundaries, creating a single, dense piece.
-
Materials Used in Sintering:
- Sintering is applicable to a wide range of materials, including:
- Metals: Stainless steel, aluminum, nickel, copper, titanium alloy, iron, carbon steels, iron-copper, copper steels, iron-nickel, and nickel steels.
- Ceramics: Porcelain, alumina, and other high-temperature components.
- Polymers: Used in rapid prototyping and filter manufacturing.
- These materials are chosen based on their properties and the desired characteristics of the final product.
- Sintering is applicable to a wide range of materials, including:
-
Applications of Sintered Products:
- Sintered products are used in various industries for:
- Small Components: Gears, pulleys, and bearings.
- High-Temperature Components: Components that require durability under extreme conditions.
- Complex Shapes: Parts that are difficult to produce using traditional manufacturing methods.
- Additive Manufacturing: Advanced sintering technologies are increasingly used in 3D printing and additive manufacturing.
- Sintered products are used in various industries for:
-
Benefits of Sintering:
- Material Versatility: Ability to use a wide range of materials, including those with high melting points.
- Cost Efficiency: Reduced material waste and lower production costs.
- Complexity and Precision: Capability to produce highly complex parts with excellent surface finishes and tight tolerance control.
- Environmental Friendliness: Minimal waste and energy-efficient process compared to traditional melting methods.
- Performance Properties: Sintered products often exhibit superior mechanical and thermal properties.
-
Types of Sintering Processes:
- Solid-State Sintering: Commonly used for ceramics and metals, where the chemical composition and purity of the material are preserved.
- Powder Metallurgy: Involves sintering metal powders under atmospheric pressure with protective gases, often used for iron-based materials.
- Liquid-Phase Sintering: Used when a small amount of liquid phase aids in the densification process, typically for certain ceramics and metals.
-
Advancements in Sintering Technology:
- As sintering technologies advance, materials are refined and improved, making them more suitable for modern manufacturing techniques like additive manufacturing. This has expanded the range of applications and improved the quality of sintered products.
-
Industries Utilizing Sintered Products:
- Automotive: For gears, bearings, and other components.
- Aerospace: High-temperature and lightweight components.
- Electronics: Heat sinks, connectors, and other precision parts.
- Medical: Implants and surgical instruments.
- Industrial: Filters, cutting tools, and wear-resistant parts.
In summary, sintered products are versatile, cost-effective, and high-performance materials produced through a process that compacts and fuses particles without melting. They are used across a wide range of industries and applications, benefiting from advancements in sintering technology and the ability to produce complex, high-quality components.
Summary Table:
Aspect | Details |
---|---|
Definition | Compacting and forming materials using heat/pressure without melting. |
Materials Used | Metals (e.g., stainless steel, titanium), ceramics, polymers. |
Applications | Gears, bearings, high-temperature components, additive manufacturing. |
Benefits | Cost efficiency, material versatility, precision, environmental friendliness. |
Industries | Automotive, aerospace, electronics, medical, industrial. |
Interested in high-performance sintered products for your industry? Contact us today to learn more!