Heat treatment is a critical process in metallurgy and materials science, used to alter the physical and mechanical properties of metals and alloys. The five primary types of heat treatment are annealing, hardening, quenching, tempering, and case hardening. Each method serves a specific purpose, such as improving ductility, increasing hardness, or relieving internal stresses. These processes involve controlled heating and cooling to achieve desired material properties, making them essential in industries like manufacturing, automotive, and aerospace.
Key Points Explained:
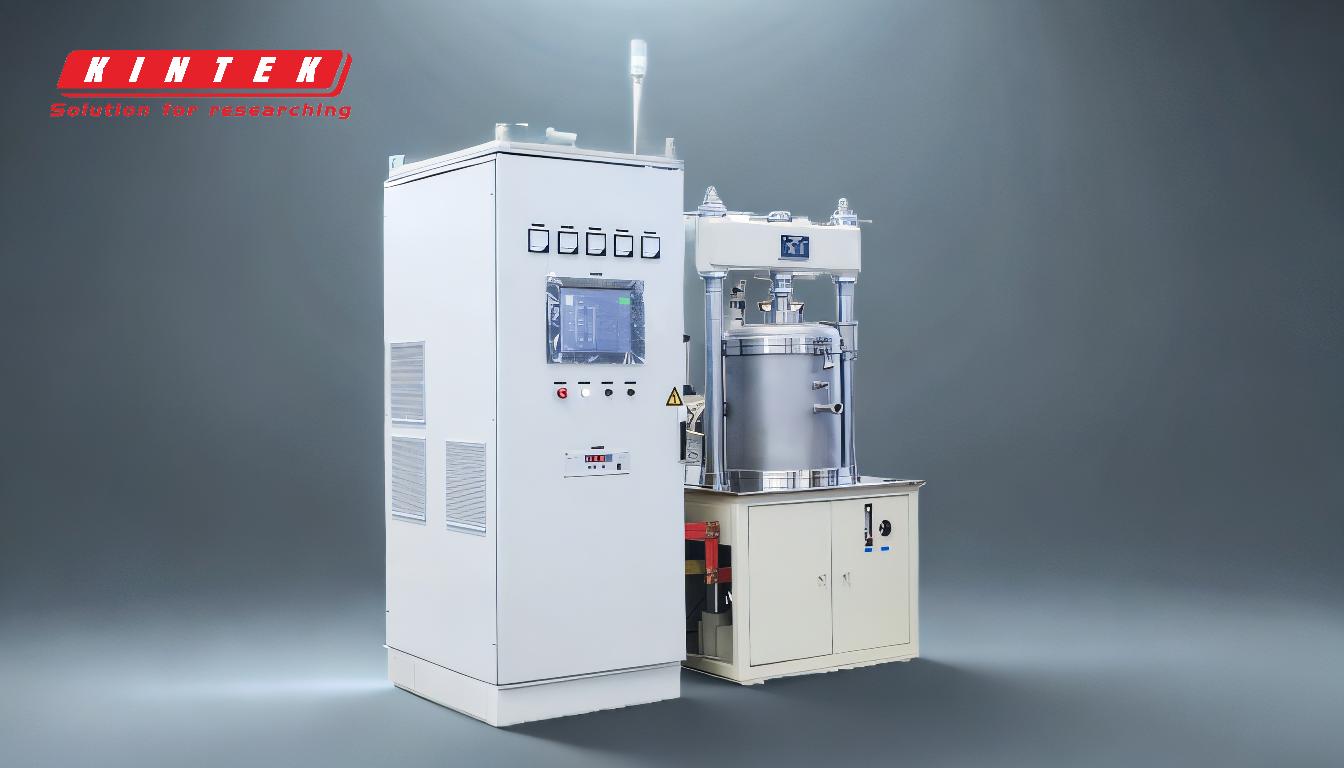
-
Annealing:
- Purpose: Annealing is used to soften metals, improve ductility, and relieve internal stresses. It also refines the grain structure, making the material more workable.
- Process: The metal is heated to a specific temperature (above its recrystallization temperature) and then cooled slowly, often in a furnace. This slow cooling allows the microstructure to stabilize.
- Applications: Commonly used in steel manufacturing, wire drawing, and sheet metal fabrication to enhance machinability and formability.
-
Hardening:
- Purpose: Hardening increases the hardness and strength of the metal, making it more resistant to wear and deformation.
- Process: The metal is heated to a high temperature and then rapidly cooled (quenched) in water, oil, or air. This rapid cooling traps carbon atoms, creating a hard, martensitic structure.
- Applications: Used in tools, gears, and components that require high wear resistance, such as cutting tools and automotive parts.
-
Quenching:
- Purpose: Quenching is a rapid cooling process used to lock the microstructure of the metal in a hardened state, typically after heating.
- Process: After heating the metal to a high temperature, it is quickly submerged in a quenching medium (water, oil, or air) to achieve a hard, brittle structure.
- Applications: Essential in the production of high-strength components like springs, blades, and structural parts.
-
Tempering:
- Purpose: Tempering reduces the brittleness caused by hardening and quenching, while maintaining the desired hardness and strength.
- Process: The metal is reheated to a temperature below its critical point and then cooled at a controlled rate. This process allows some of the martensite to transform into softer structures like bainite or pearlite.
- Applications: Used in tools, knives, and structural components to achieve a balance between hardness and toughness.
-
Case Hardening:
- Purpose: Case hardening increases the surface hardness of the metal while maintaining a softer, more ductile core. This is particularly useful for components that require a hard surface for wear resistance and a tough core for impact resistance.
- Process: The surface of the metal is infused with carbon or nitrogen (through processes like carburizing or nitriding) and then heat-treated to harden the surface layer.
- Applications: Commonly used in gears, camshafts, and other components that experience high surface wear but need to withstand impact.
These five types of heat treatment are fundamental in tailoring the properties of metals to meet specific industrial requirements. By understanding and applying these processes, manufacturers can produce materials with optimized strength, hardness, and durability for a wide range of applications.
Summary Table:
Heat Treatment | Purpose | Process | Applications |
---|---|---|---|
Annealing | Soften metals, improve ductility, relieve internal stresses | Heated above recrystallization temperature, then cooled slowly | Steel manufacturing, wire drawing, sheet metal fabrication |
Hardening | Increase hardness and strength, resist wear and deformation | Heated to high temperature, then rapidly cooled (quenched) | Tools, gears, automotive parts |
Quenching | Lock microstructure in a hardened state | Heated to high temperature, then rapidly submerged in quenching medium | Springs, blades, structural parts |
Tempering | Reduce brittleness while maintaining hardness and strength | Reheated below critical point, then cooled at a controlled rate | Tools, knives, structural components |
Case Hardening | Increase surface hardness while maintaining a ductile core | Surface infused with carbon/nitrogen, then heat-treated | Gears, camshafts, components requiring wear resistance and impact toughness |
Need help selecting the right heat treatment for your materials? Contact our experts today to optimize your processes!