Rotary kiln incineration is a widely used method for thermal processing and waste treatment, offering several advantages such as high efficiency, versatility in processing various materials, and advanced technological features. However, it also has notable disadvantages, including the production of off-gases requiring treatment, higher maintenance requirements, and significant installation and operational costs. Below, the key advantages and disadvantages are explored in detail to provide a comprehensive understanding of rotary kiln incineration.
Key Points Explained:
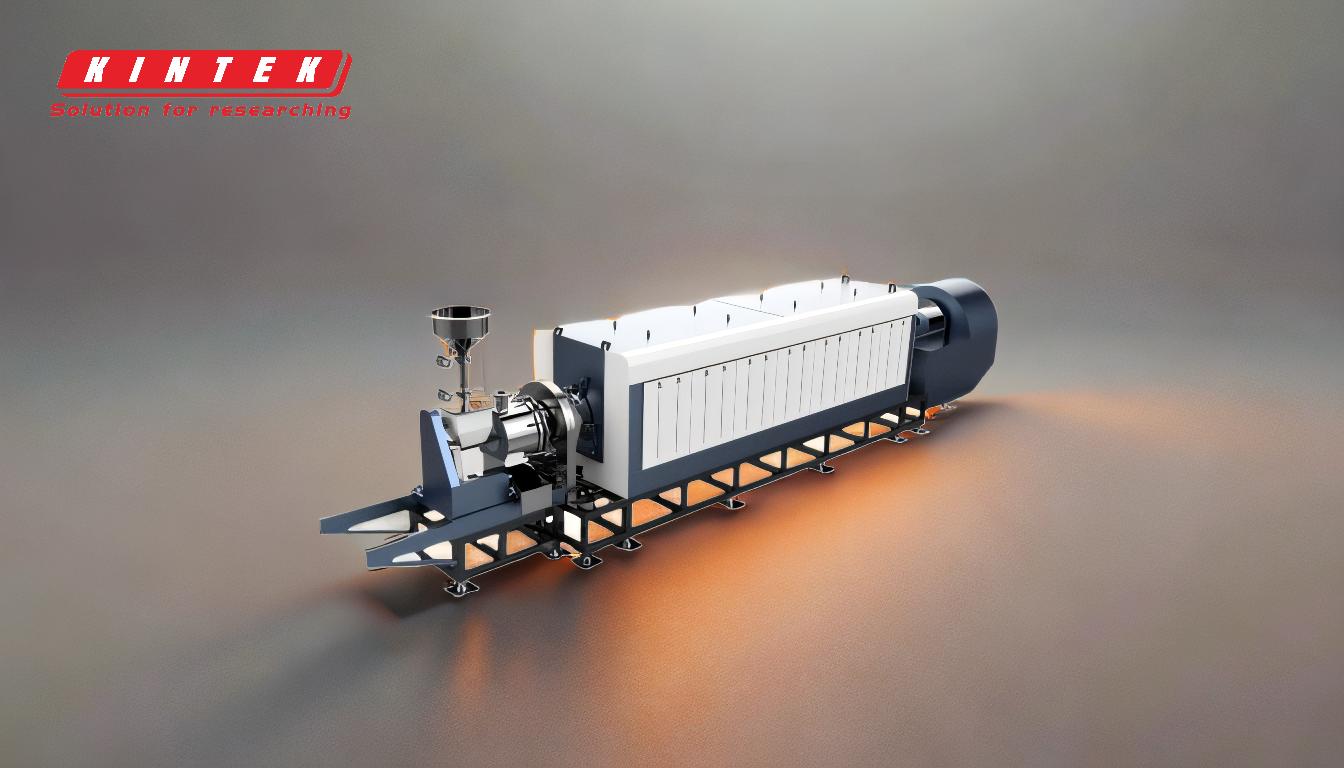
-
Advantages of Rotary Kiln Incineration:
-
High Efficiency in Thermal Processing:
- Direct-fired rotary kilns are particularly efficient for thermal processing, making them a preferred choice for many industrial applications. Their ability to handle high temperatures and large volumes of materials ensures consistent and effective processing.
-
Versatility in Material Processing:
- Rotary kilns can process a wide range of materials, including dross and low-grade scrap, which are difficult to handle in other types of furnaces. This versatility makes them suitable for industries dealing with diverse waste streams.
-
Advanced Technological Features:
- Modern rotary kilns incorporate advanced technologies such as hydraulic block wheel devices, high-precision metering piston pumps, and contact graphite block sealing devices. These features enhance performance, ensure stable operation, and reduce energy consumption.
-
Effective Waste Treatment:
- Indirect-fired rotary kilns have gained popularity for waste treatment due to their economic benefits and ability to prevent secondary pollution. They ensure thorough and harmless treatment of waste, making them a promising option for sustainable waste disposal.
-
High Efficiency in Thermal Processing:
-
Disadvantages of Rotary Kiln Incineration:
-
Production of Off-Gases:
- One of the primary disadvantages of direct-fired rotary kilns is the production of significant amounts of off-gases. These gases require extensive treatment to meet environmental regulations, increasing operational complexity and costs.
-
Higher Maintenance Requirements:
- Rotary kilns, especially those processing challenging materials, often require more frequent maintenance. This can lead to increased downtime and higher operational costs.
-
Salt Cake Production:
- The processing of certain materials in rotary kilns can result in the production of salt cake, which is classified as hazardous waste. Proper disposal of this byproduct adds to the operational challenges and costs.
-
High Installation and Operational Costs:
- The installation of rotary kiln incinerators, particularly those requiring secondary chambers for efficient combustion and emission control, involves significant capital investment. Additionally, the operational costs, including energy consumption and maintenance, can be substantial.
-
Potential for Heat Loss:
- While the hot end expansion type rotary kiln improves heating capacity and output, excessive enlargement of the combustion zone can lead to insufficient pre-burning ability and increased heat loss. This can reduce overall efficiency and increase energy consumption.
-
Production of Off-Gases:
In summary, rotary kiln incineration offers numerous benefits, including high efficiency, versatility, and advanced technological features, making it a valuable tool for thermal processing and waste treatment. However, the associated challenges, such as off-gas treatment, higher maintenance, and significant costs, must be carefully managed to maximize the advantages and minimize the disadvantages.
Summary Table:
Aspect | Advantages | Disadvantages |
---|---|---|
Efficiency | High efficiency in thermal processing, handles high temperatures and volumes. | Potential heat loss due to excessive combustion zone enlargement. |
Versatility | Processes diverse materials like dross and low-grade scrap. | Higher maintenance requirements, especially for challenging materials. |
Technological Features | Advanced features like hydraulic block wheels and graphite sealing devices. | Production of off-gases requiring treatment, increasing operational costs. |
Waste Treatment | Effective waste treatment, prevents secondary pollution. | Salt cake production, classified as hazardous waste, adding disposal challenges. |
Cost | Economic benefits in waste treatment with indirect-fired kilns. | High installation and operational costs, including energy and maintenance. |
Discover how rotary kiln incineration can optimize your thermal processing—contact our experts today for tailored solutions!