Transfer molding is a manufacturing process used primarily for thermosetting plastics and rubber, where material is preheated and then forced into a heated mold cavity under pressure. This method is widely used in industries requiring high precision and complex shapes, such as electronics, automotive, and aerospace. The process offers several advantages, such as high production rates, excellent surface finish, and the ability to produce intricate parts. However, it also has drawbacks, including higher initial tooling costs, limitations in material selection, and potential for material waste. Understanding the pros and cons of transfer molding is essential for manufacturers to make informed decisions about its suitability for specific applications.
Key Points Explained:
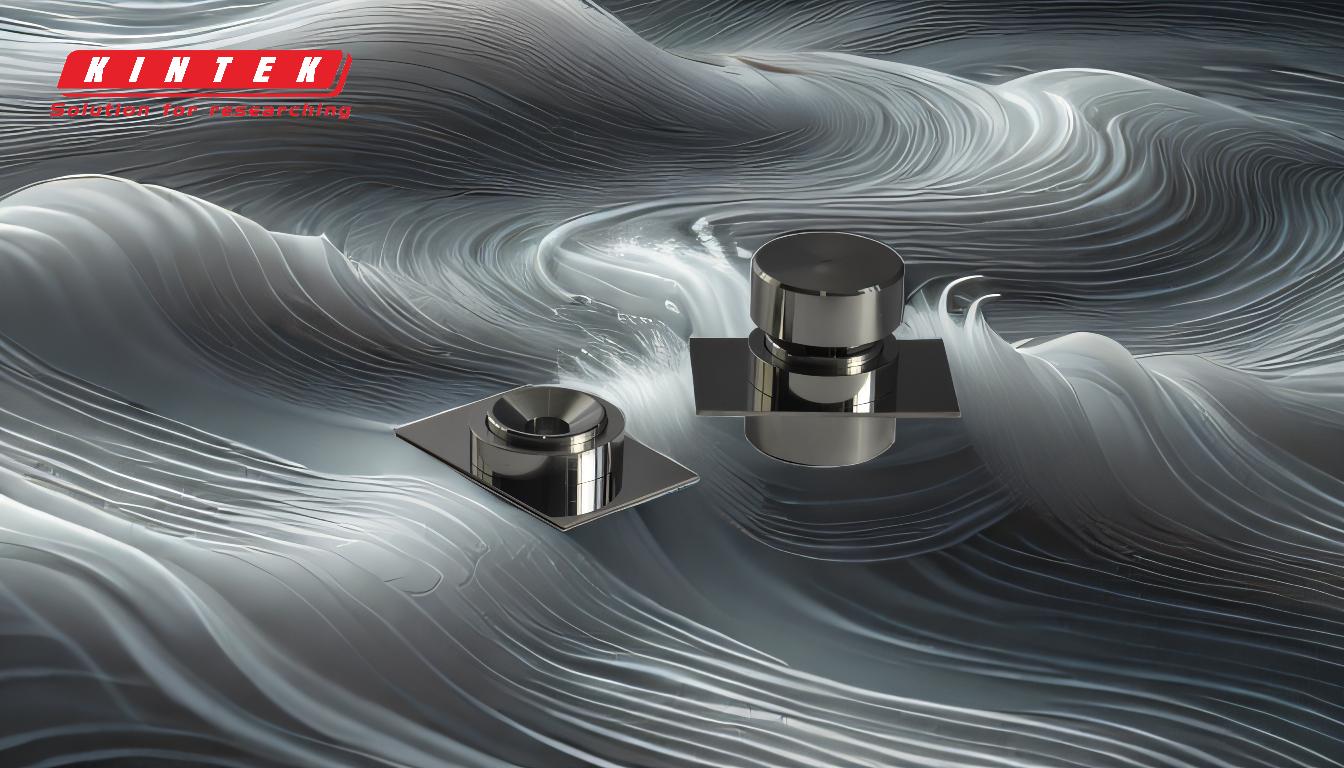
-
Advantages of Transfer Molding:
- High Production Rates: Transfer molding allows for rapid production cycles, making it suitable for high-volume manufacturing. The preheated material flows quickly into the mold, reducing cycle times compared to other methods like compression molding.
- Excellent Surface Finish: The process produces parts with smooth surfaces and fine details, which is ideal for applications requiring aesthetic appeal or precision, such as electrical connectors or automotive components.
- Ability to Produce Complex Shapes: Transfer molding is capable of creating intricate geometries and thin-walled parts that might be challenging with other molding techniques.
- Reduced Flash: The controlled pressure and flow of material minimize excess material (flash) around the edges of the molded part, reducing post-processing requirements.
-
Disadvantages of Transfer Molding:
- High Initial Tooling Costs: The molds used in transfer molding are typically more expensive than those in compression molding due to their complexity and the need for precise alignment.
- Material Limitations: Transfer molding is primarily suited for thermosetting materials, which cannot be remelted or reshaped after curing. This limits the range of materials that can be used compared to injection molding.
- Material Waste: The process can generate waste material, particularly in the form of sprues and runners, which are not always reusable.
- Longer Setup Time: Preparing the mold and material for transfer molding can be more time-consuming compared to simpler processes like compression molding.
-
Comparison with Other Molding Techniques:
- Compression Molding: Transfer molding offers better control over material flow and part detail than compression molding but at a higher cost and complexity.
- Injection Molding: While injection molding is more versatile in terms of material selection and can handle larger production volumes, transfer molding is better suited for thermosetting materials and smaller, intricate parts.
-
Applications of Transfer Molding:
- Electronics: Used for encapsulating electronic components, such as integrated circuits and connectors, due to its precision and ability to protect delicate parts.
- Automotive: Ideal for producing gaskets, seals, and other components requiring high durability and resistance to heat and chemicals.
- Aerospace: Suitable for manufacturing lightweight, high-strength parts with complex geometries.
-
Factors to Consider When Choosing Transfer Molding:
- Part Complexity: Transfer molding is best suited for parts with intricate designs or thin walls.
- Material Requirements: Ensure the material is compatible with the thermosetting process.
- Production Volume: Evaluate whether the production volume justifies the higher tooling costs.
- Cost-Benefit Analysis: Weigh the advantages of precision and surface finish against the disadvantages of material waste and setup time.
In summary, transfer molding is a versatile and efficient manufacturing process with distinct advantages in precision and surface finish. However, its suitability depends on factors such as material compatibility, part complexity, and production volume. By carefully evaluating these aspects, manufacturers can determine whether transfer molding is the right choice for their specific needs.
Summary Table:
Aspect | Advantages | Disadvantages |
---|---|---|
Production Rates | High production rates, suitable for high-volume manufacturing. | Longer setup time compared to simpler processes. |
Surface Finish | Excellent surface finish with smooth surfaces and fine details. | Material waste in the form of sprues and runners. |
Complex Shapes | Capable of creating intricate geometries and thin-walled parts. | High initial tooling costs due to complex molds. |
Material Compatibility | Ideal for thermosetting materials. | Limited to thermosetting materials, restricting material selection. |
Want to know if transfer moulding is right for your project? Contact our experts today for a consultation!