Hot pressing is a manufacturing technique that combines heat and pressure to create materials with superior properties. This method is particularly advantageous for producing high-performance components with minimal defects. The process involves applying both thermal energy and mechanical pressure simultaneously, which leads to enhanced material properties such as increased density, reduced porosity, and improved mechanical strength. Hot pressing is widely used in industries requiring high precision and performance, such as aerospace, automotive, and electronics. The ability to control heat and pressure precisely allows for the production of complex shapes with excellent dimensional accuracy and mechanical properties.
Key Points Explained:
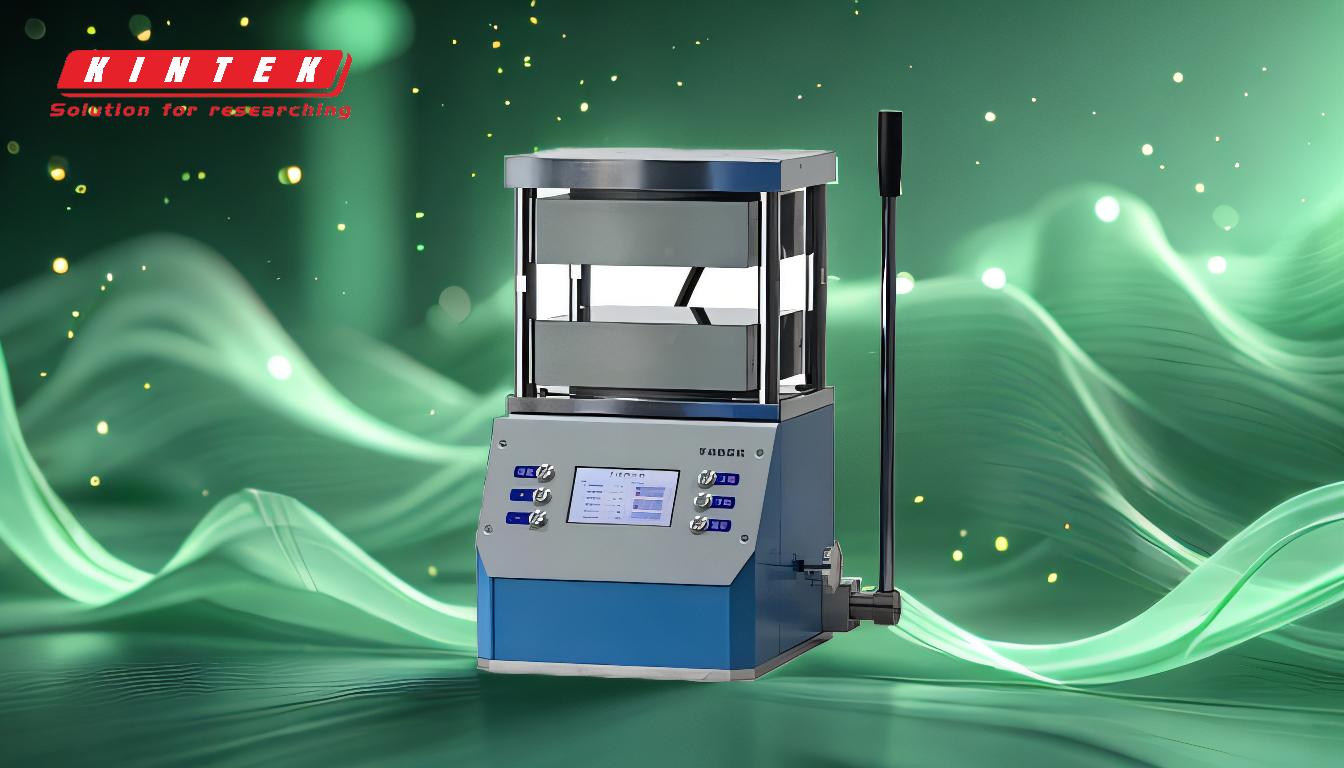
-
No Oxidation and Low Porosity:
- Hot pressing sintering ensures that the final product has no oxidation and low porosity. This is crucial for materials that need to maintain their structural integrity and performance under harsh conditions. The absence of oxidation means that the material retains its original properties, while low porosity ensures that the material is dense and free from voids, which can weaken the structure.
-
Fewer Impurities and Higher Degree of Alloying:
- The process of hot pressing results in fewer impurities within the material. This is because the combination of heat and pressure helps to eliminate contaminants that might be present in the raw powder. Additionally, hot pressing allows for a higher degree of alloying, which means that different metals can be more uniformly mixed, leading to improved material properties such as strength, hardness, and resistance to wear and corrosion.
-
Improved Mechanical Properties:
- Hot pressing significantly enhances the mechanical properties of the material. The simultaneous application of heat and pressure ensures that the material is densified, leading to increased strength and toughness. This is particularly important for components that are subjected to high stress or need to withstand extreme conditions. The improved mechanical properties make hot-pressed materials suitable for critical applications in industries like aerospace and automotive.
-
Dimensional Accuracy:
- One of the key advantages of hot pressing is the ability to achieve high dimensional accuracy in a single step. The precise control of heat and pressure allows for the production of components with tight tolerances and complex geometries. This reduces the need for additional machining or finishing processes, saving time and costs in the manufacturing process.
-
Tailored Heat and Pressure Control:
- Hot pressing allows for the precise control of heat and pressure, which can be tailored to the specific requirements of the powder material being processed. This customization ensures that the material properties are optimized for the intended application. For example, different materials may require different temperature and pressure profiles to achieve the desired density and mechanical properties.
-
Use of Specialized Mold Materials:
- The use of specialized mold materials, such as super alloys or graphite, is another advantage of hot pressing. These materials can withstand the extreme conditions of high temperature and pressure, ensuring the integrity of the process. The choice of mold material can also influence the final properties of the product, such as surface finish and dimensional stability.
-
Elimination of Porosity and Increased Density:
- Hot isostatic pressing (a variant of hot pressing) combines high temperatures with isostatic pressure, which eliminates porosity and increases the density of the material. This results in a more homogeneous microstructure, which improves mechanical properties such as tensile strength, fatigue resistance, and fracture toughness. The elimination of porosity also reduces the risk of microshrinkage, which can lead to defects in the final product.
-
Enhanced Performance in Critical Applications:
- The combination of improved mechanical properties, dimensional accuracy, and material integrity makes hot-pressed materials ideal for critical applications. For instance, in the aerospace industry, components made through hot pressing can withstand the extreme conditions of high altitude and temperature fluctuations. Similarly, in the automotive industry, hot-pressed parts can endure the stresses of high-speed operation and heavy loads.
In summary, hot pressing offers a range of advantages that make it a preferred method for producing high-performance materials. The ability to control heat and pressure precisely, combined with the use of specialized mold materials, results in products with superior mechanical properties, dimensional accuracy, and material integrity. These benefits make hot pressing an essential technique in industries that demand high precision and reliability.
Summary Table:
Advantage | Description |
---|---|
No Oxidation and Low Porosity | Ensures structural integrity and material density, free from voids and oxidation. |
Fewer Impurities | Eliminates contaminants, enhancing alloying and material uniformity. |
Improved Mechanical Properties | Increases strength, toughness, and resistance to wear and corrosion. |
Dimensional Accuracy | Produces complex shapes with tight tolerances in a single step. |
Tailored Heat and Pressure Control | Customizes temperature and pressure for optimal material properties. |
Specialized Mold Materials | Uses durable materials like super alloys or graphite for high-temperature use. |
Elimination of Porosity | Increases density and homogeneity, reducing defects like microshrinkage. |
Enhanced Performance | Ideal for critical applications in aerospace, automotive, and electronics. |
Ready to elevate your material performance? Contact us today to learn how hot pressing can benefit your applications!