Induction casting is a modern and efficient method of melting metals using electromagnetic induction. This process offers several advantages, particularly in improving the quality of finished products. By leveraging induced currents, induction casting ensures a uniform distribution of elements within the alloy, leading to higher-quality outputs. Below, we will explore the key advantages of induction casting in detail.
Key Points Explained:
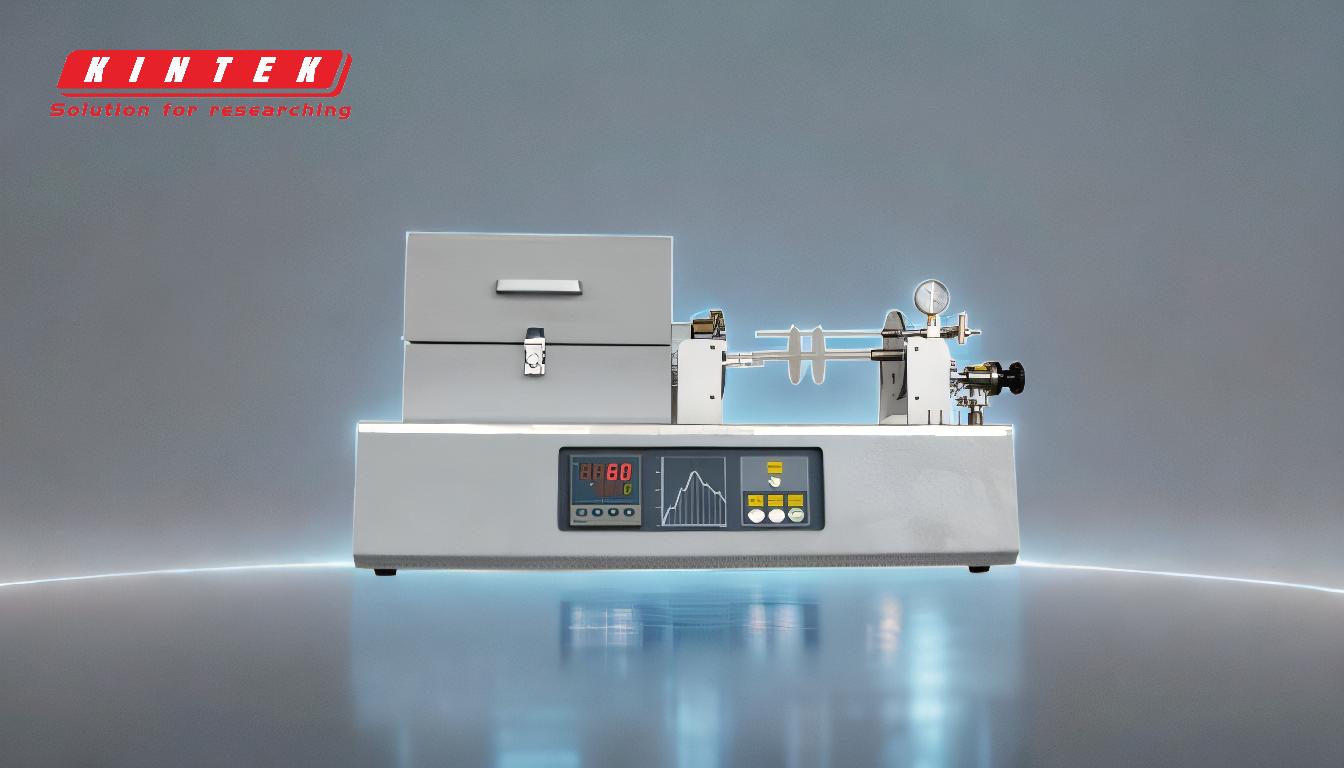
-
Improved Quality of Finished Products
- Induction casting enhances the quality of finished products by remixing the elements present in the melting alloy. The induced currents create a stirring effect, ensuring an even dispersion of all elements within the alloy.
- This uniformity eliminates inconsistencies, such as segregation or uneven composition, which are common in traditional melting methods. As a result, the final product exhibits superior mechanical properties, such as strength, durability, and resistance to wear and tear.
-
Energy Efficiency
- Induction casting is highly energy-efficient compared to traditional methods like gas or coal-fired furnaces. The process directly heats the metal using electromagnetic fields, minimizing heat loss and reducing energy consumption.
- This efficiency not only lowers operational costs but also contributes to a more sustainable manufacturing process by reducing carbon emissions.
-
Precision and Control
- The induction casting process allows for precise temperature control, which is critical for achieving the desired material properties. Operators can fine-tune the heating process to match specific alloy requirements.
- This level of control ensures consistent results, reduces the likelihood of defects, and enables the production of complex or high-precision components.
-
Faster Melting Rates
- Induction casting heats metals rapidly, significantly reducing melting times compared to conventional methods. This speed increases production throughput and allows manufacturers to meet tight deadlines without compromising quality.
- The quick heating process also minimizes the risk of oxidation or contamination, further enhancing the quality of the final product.
-
Cleaner and Safer Process
- Unlike traditional methods that rely on combustion, induction casting produces no flames, smoke, or harmful emissions. This creates a cleaner working environment and reduces the risk of workplace hazards.
- Additionally, the absence of open flames minimizes the risk of accidents, making induction casting a safer option for operators.
-
Versatility in Applications
- Induction casting is suitable for a wide range of metals and alloys, including steel, aluminum, copper, and precious metals. This versatility makes it an ideal choice for industries such as aerospace, automotive, jewelry, and electronics.
- The ability to handle different materials with consistent results makes induction casting a valuable tool for manufacturers with diverse production needs.
-
Reduced Waste and Material Loss
- The precise heating and stirring action of induction casting minimize material loss due to oxidation or evaporation. This efficiency reduces waste and ensures that more of the raw material is utilized in the final product.
- Lower material loss translates to cost savings and a more sustainable production process.
In conclusion, induction casting offers numerous advantages, including improved product quality, energy efficiency, precise control, faster melting rates, and a cleaner, safer process. Its versatility and ability to reduce waste make it a preferred choice for modern manufacturing across various industries. By leveraging the benefits of induction casting, manufacturers can achieve higher-quality outputs while optimizing their production processes.
Summary Table:
Advantage | Description |
---|---|
Improved Quality | Uniform element distribution ensures superior mechanical properties. |
Energy Efficiency | Direct heating minimizes heat loss, reducing energy consumption and costs. |
Precision and Control | Fine-tuned temperature control ensures consistent, defect-free results. |
Faster Melting Rates | Rapid heating increases production throughput and minimizes contamination. |
Cleaner and Safer Process | No flames or harmful emissions, creating a safer and cleaner work environment. |
Versatility | Suitable for steel, aluminum, copper, and precious metals across industries. |
Reduced Waste | Minimizes material loss, ensuring cost savings and sustainable production. |
Ready to enhance your manufacturing process with induction casting? Contact us today to learn more!