Isostatic compaction, also known as isostatic pressing, offers numerous advantages over traditional molding methods. It is particularly valued for its ability to produce components with uniform density and strength in all directions, making it ideal for complex shapes and high-performance applications. The process uses flexible molds, such as rubber or elastomeric molds, which allow for greater shape flexibility compared to rigid steel molds used in traditional methods. Additionally, isostatic pressing, especially hot isostatic pressing (HIP), enhances material properties by eliminating internal porosity, improving mechanical properties, and enabling the production of lighter, more durable components. While it may be less efficient and more costly than traditional methods, the superior quality and performance of the final product often justify the investment.
Key Points Explained:
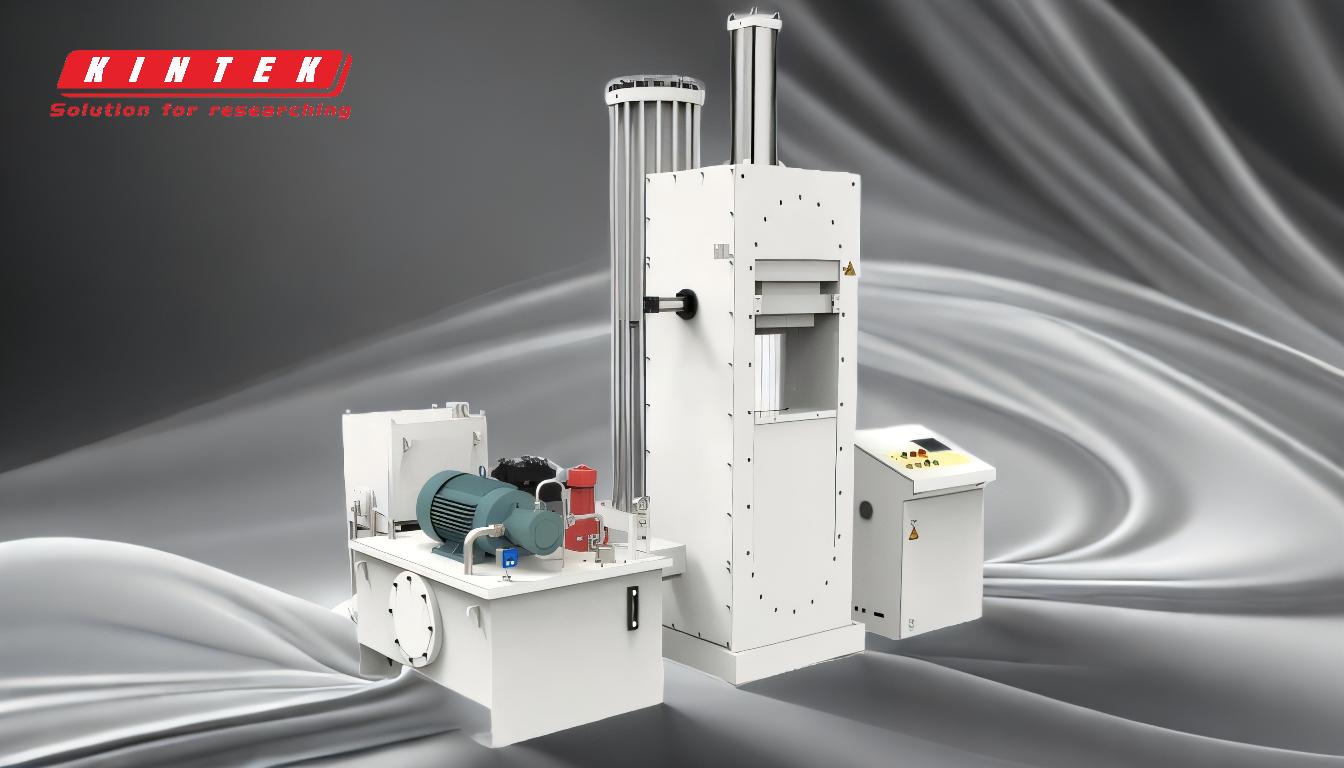
-
Uniform Density and Strength:
- Isostatic pressing ensures uniform density and strength in all directions, which is critical for high-performance applications. This uniformity is achieved because the pressure is applied equally from all sides, unlike uniaxial pressing where pressure is applied from one or two directions.
-
Shape Flexibility:
- The use of flexible molds, such as rubber or elastomeric molds, allows for the production of complex shapes that are difficult or impossible to achieve with traditional steel molds. This makes isostatic molding particularly suitable for components with intricate geometries.
-
Improved Material Properties:
- Hot isostatic pressing (HIP) significantly enhances material properties by eliminating internal microporosity and densifying powders in the solid state. This results in materials with fine, uniform grain size and isotropic structure, leading to superior mechanical properties such as improved fatigue life, ductility, impact strength, and toughness.
-
High Compact Densities:
- Isostatic pressing can achieve high compact densities, which are essential for producing strong and durable components. This is particularly beneficial for materials that require high density for optimal performance.
-
Versatility in Applications:
- The process is versatile and can be used for a wide range of materials, including metals, ceramics, and composites. It is also suitable for both small and large components, making it a flexible option for various industries.
-
Longer Service Life:
- Components produced using isostatic pressing, such as silicon carbide crucibles, exhibit a longer service life compared to those made with traditional methods. For example, silicon carbide crucibles produced via isostatic molding have a service life that is 3-5 times longer than clay graphite crucibles.
-
Energy Efficiency and Safety:
- Isostatic presses are known for their low energy consumption, low failure rates, and stable operation. They are also easy to use and maintain, and they offer a high level of safety, making them a reliable choice for industrial applications.
-
Repair of Internal Defects:
- HIP can repair internal porosity defects in materials, which is particularly useful for components that have been cast or sintered. This capability not only improves the quality of the final product but also reduces scrap and losses.
-
Lighter Designs:
- The ability to produce components with uniform density and improved mechanical properties allows for the design of lighter components without compromising strength or durability. This is particularly advantageous in industries such as aerospace and automotive, where weight reduction is critical.
-
Formation of Metallurgical Bonds:
- HIP can form metallurgical bonds between different materials, enabling the production of composite components with unique properties. This is useful for applications requiring materials with specific combinations of properties, such as high strength and corrosion resistance.
In summary, isostatic compaction offers a range of advantages that make it a preferred method for producing high-quality, complex, and durable components. While it may involve higher costs and lower efficiency compared to traditional methods, the benefits in terms of material properties, shape flexibility, and component performance often outweigh these drawbacks.
Summary Table:
Advantage | Description |
---|---|
Uniform Density and Strength | Ensures consistent density and strength in all directions, ideal for high-performance components. |
Shape Flexibility | Flexible molds enable production of complex shapes not achievable with traditional methods. |
Improved Material Properties | Eliminates internal porosity, enhances mechanical properties, and improves durability. |
High Compact Densities | Produces strong, durable components with high density for optimal performance. |
Versatility in Applications | Suitable for metals, ceramics, composites, and components of varying sizes. |
Longer Service Life | Components like silicon carbide crucibles last 3-5 times longer than traditional alternatives. |
Energy Efficiency and Safety | Low energy consumption, low failure rates, and stable, safe operation. |
Repair of Internal Defects | HIP repairs internal porosity, improving quality and reducing scrap. |
Lighter Designs | Enables lighter components without compromising strength or durability. |
Formation of Metallurgical Bonds | Creates composite components with unique properties for specialized applications. |
Unlock the full potential of isostatic compaction for your applications—contact our experts today!