Liquid phase sintering (LPS) is a specialized sintering technique that offers several advantages, particularly for materials that are difficult to sinter using conventional methods. By introducing a sintering aid that forms a transient liquid phase during the process, LPS significantly lowers the sintering temperature, enhances material densification, and improves the mechanical properties of the final product. This method is particularly useful for materials with high melting points or those that are challenging to sinter due to their composition. The process also allows for better control over porosity, grain rearrangement, and the overall microstructure of the material, making it a versatile and efficient option for various industrial applications.
Key Points Explained:
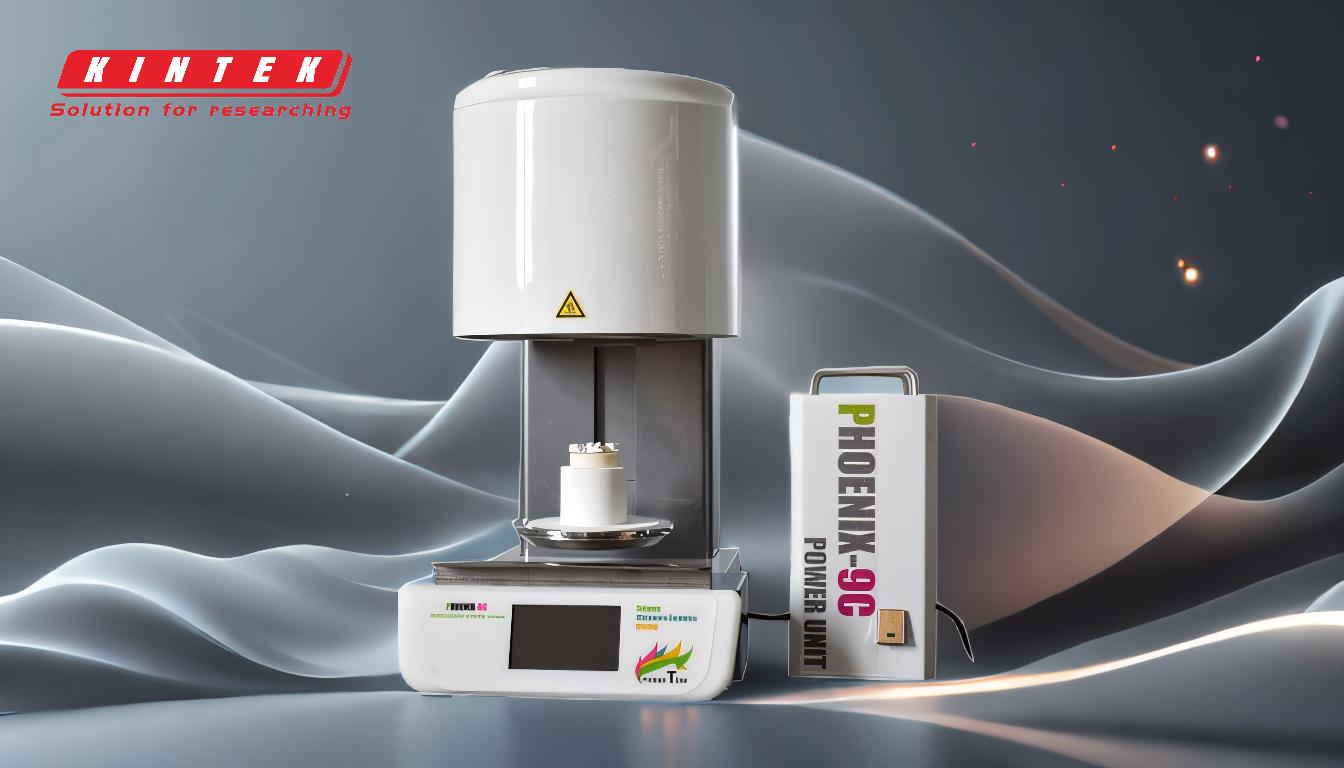
-
Lower Sintering Temperature:
- Explanation: Liquid phase sintering involves the addition of a sintering aid that melts at a lower temperature than the base material. This creates a transient liquid phase at the particle contact surfaces, which significantly reduces the overall sintering temperature required.
- Advantages: Lowering the sintering temperature reduces energy consumption, making the process more cost-effective and environmentally friendly. It also minimizes the risk of thermal degradation or unwanted phase transformations in the material.
-
Enhanced Densification:
- Explanation: The liquid phase formed during sintering fills the pores between particles and facilitates grain rearrangement. This leads to a more favorable packing arrangement and higher densification of the material.
- Advantages: Enhanced densification results in materials with lower porosity, which improves their mechanical properties such as strength, durability, and wear resistance. This is particularly beneficial for applications requiring high-performance materials.
-
Improved Microstructure Control:
- Explanation: The liquid phase helps in rearranging grains and controlling the microstructure of the material. This leads to a more uniform and controlled porosity, as well as a finer grain structure.
- Advantages: Improved microstructure control allows for the production of materials with consistent properties, which is crucial for applications where uniformity and repeatability are essential. It also enables the creation of nearly net-shaped objects, reducing the need for extensive post-processing.
-
Ability to Sinter Difficult Materials:
- Explanation: Liquid phase sintering is particularly effective for materials that are difficult to sinter using conventional methods, such as those with very high melting points or complex compositions.
- Advantages: This method expands the range of materials that can be effectively sintered, enabling the production of advanced materials like high-strength alloys, ceramics, and composites. It also allows for the sintering of materials that would otherwise require extremely high temperatures or specialized equipment.
-
Environmental and Economic Benefits:
- Explanation: The lower sintering temperatures and reduced energy requirements of liquid phase sintering make it a more sustainable and cost-effective option compared to traditional sintering methods.
- Advantages: The process is more environmentally friendly due to reduced energy consumption and lower emissions. Additionally, the cost savings associated with lower energy use and reduced material waste make it an economically attractive option for manufacturers.
-
High Levels of Purity and Uniformity:
- Explanation: Liquid phase sintering allows for high levels of purity and uniformity in the starting materials, as the process is highly controlled and repeatable.
- Advantages: The resulting materials have consistent properties, which is critical for applications requiring high precision and reliability. This is particularly important in industries such as aerospace, automotive, and medical devices, where material performance is paramount.
-
Creation of High-Strength Materials:
- Explanation: The enhanced densification and improved microstructure control achieved through liquid phase sintering result in materials with superior mechanical properties, such as high strength and durability.
- Advantages: This makes liquid phase sintering an ideal method for producing high-strength components, such as turbine blades, cutting tools, and structural parts, which are required to withstand extreme conditions.
In summary, liquid phase sintering offers a range of advantages, including lower sintering temperatures, enhanced densification, improved microstructure control, and the ability to sinter difficult materials. These benefits make it a highly efficient and versatile sintering method, suitable for a wide range of industrial applications.
Summary Table:
Advantage | Explanation | Key Benefit |
---|---|---|
Lower Sintering Temperature | Uses a sintering aid to create a transient liquid phase, reducing energy needs. | Cost-effective, eco-friendly, and minimizes thermal degradation. |
Enhanced Densification | Liquid phase fills pores, improving packing and material density. | Higher strength, durability, and wear resistance. |
Improved Microstructure Control | Liquid phase aids grain rearrangement for uniform porosity and finer grains. | Consistent material properties, reduced post-processing, and near-net-shape production. |
Ability to Sinter Difficult Materials | Effective for high-melting-point or complex materials. | Expands material options, including alloys, ceramics, and composites. |
Environmental & Economic Benefits | Lower energy use and reduced emissions. | Sustainable, cost-effective, and reduces material waste. |
High Purity & Uniformity | Controlled process ensures consistent material properties. | Ideal for precision applications in aerospace, automotive, and medical industries. |
Creation of High-Strength Materials | Enhanced densification and microstructure control improve mechanical properties. | Produces durable components like turbine blades, cutting tools, and structural parts. |
Ready to enhance your material processing? Contact us today to learn how liquid phase sintering can benefit your applications!