Physical vapor deposition (PVD) is a highly advantageous coating technology widely used across various industries due to its ability to produce durable, high-quality, and environmentally friendly coatings. PVD coatings are known for their corrosion resistance, high hardness, and ability to withstand high temperatures. They offer a wide range of colors and finishes, making them suitable for applications in jewelry, watches, and industrial tools. Additionally, PVD is performed under vacuum conditions, ensuring precise deposition of thin films with minimal distortion. Compared to other coating methods, PVD is more environmentally friendly, reduces production costs, and enhances the lifespan and performance of coated products.
Key Points Explained:
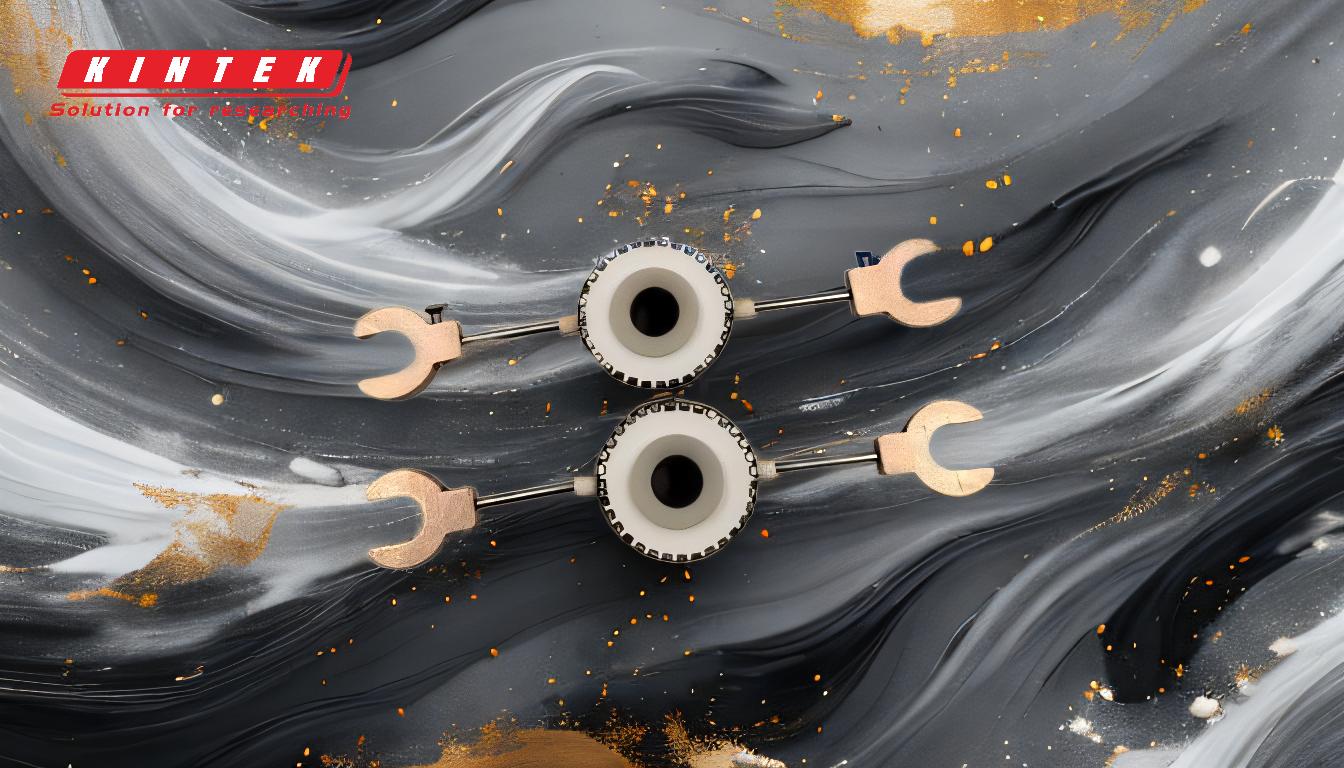
-
Durability and Performance:
- PVD coatings are highly durable, offering excellent resistance to corrosion, wear, and high temperatures. This makes them ideal for applications in harsh environments, such as cutting tools, industrial machinery, and automotive components.
- The molecular-scale application of PVD ensures a superior finish, enhancing the longevity and performance of the coated products.
-
Versatility in Appearance:
- PVD can replicate the appearance of expensive metals like gold, brass, bronze, and copper without the risk of patina. This makes it a popular choice in the jewelry and watchmaking industries for creating finishes such as rose gold, black, or gunmetal.
- The process allows for a wide range of colors and finishes, providing flexibility in design and aesthetics.
-
Environmental Benefits:
- PVD is an environmentally friendly process that reduces the use, management, and disposal of toxic substances. Unlike other coating methods that rely on chemical reactions, PVD minimizes environmental impact.
- The process is performed under vacuum conditions, preventing the release of harmful byproducts into the atmosphere.
-
Precision and Efficiency:
- PVD coatings are deposited with high accuracy, with average thicknesses ranging from 0.02 to 5 microns. This precision makes PVD suitable for applications requiring tight tolerances, such as optical coatings and fine blanking tools.
- The lower process temperatures used in PVD result in minimal distortion, ensuring the integrity of the coated materials.
-
Cost-Effectiveness:
- PVD coating machines are computer-controlled, enabling operators to multitask and reducing production costs and turnaround time. This makes PVD suitable for both high-volume manufacturing and small batch production.
- The ability to recreate expensive metal finishes at a lower cost provides significant savings in industries like jewelry and consumer electronics.
-
Applications in Various Industries:
- PVD is widely used in industries such as semiconductors, optoelectronics, and tool manufacturing due to its ability to produce high-purity, high-quality coatings.
- It is particularly beneficial for high-speed steel (HSS) and carbide cutting tools, plastic injection molding components, and optical coatings, where durability and precision are critical.
In summary, PVD offers a combination of durability, versatility, environmental sustainability, precision, and cost-effectiveness, making it a preferred choice for a wide range of industrial and decorative applications.
Summary Table:
Advantage | Description |
---|---|
Durability & Performance | High resistance to corrosion, wear, and high temperatures; superior finish. |
Versatility in Appearance | Wide range of colors and finishes; replicates expensive metals without patina. |
Environmental Benefits | Eco-friendly process; reduces toxic substances and harmful byproducts. |
Precision & Efficiency | High-accuracy deposition; minimal distortion; suitable for tight tolerances. |
Cost-Effectiveness | Reduces production costs; ideal for high-volume and small batch production. |
Applications | Used in semiconductors, optoelectronics, tool manufacturing, and more. |
Ready to enhance your products with PVD coatings? Contact us today to learn more!