Vacuum firing, particularly using a vacuum furnace, offers numerous advantages that make it a preferred method for heat treatment processes in various industries. These benefits include precise temperature control, uniform heating, low contamination, rapid cooling, and enhanced material properties. Additionally, vacuum firing ensures a clean and controlled environment, leading to high-quality, ultra-clean components with improved mechanical properties. The process is versatile, energy-efficient, and environmentally friendly, making it suitable for applications like annealing, brazing, sintering, and hardening. Below, the key advantages of vacuum firing are explained in detail.
Key Points Explained:
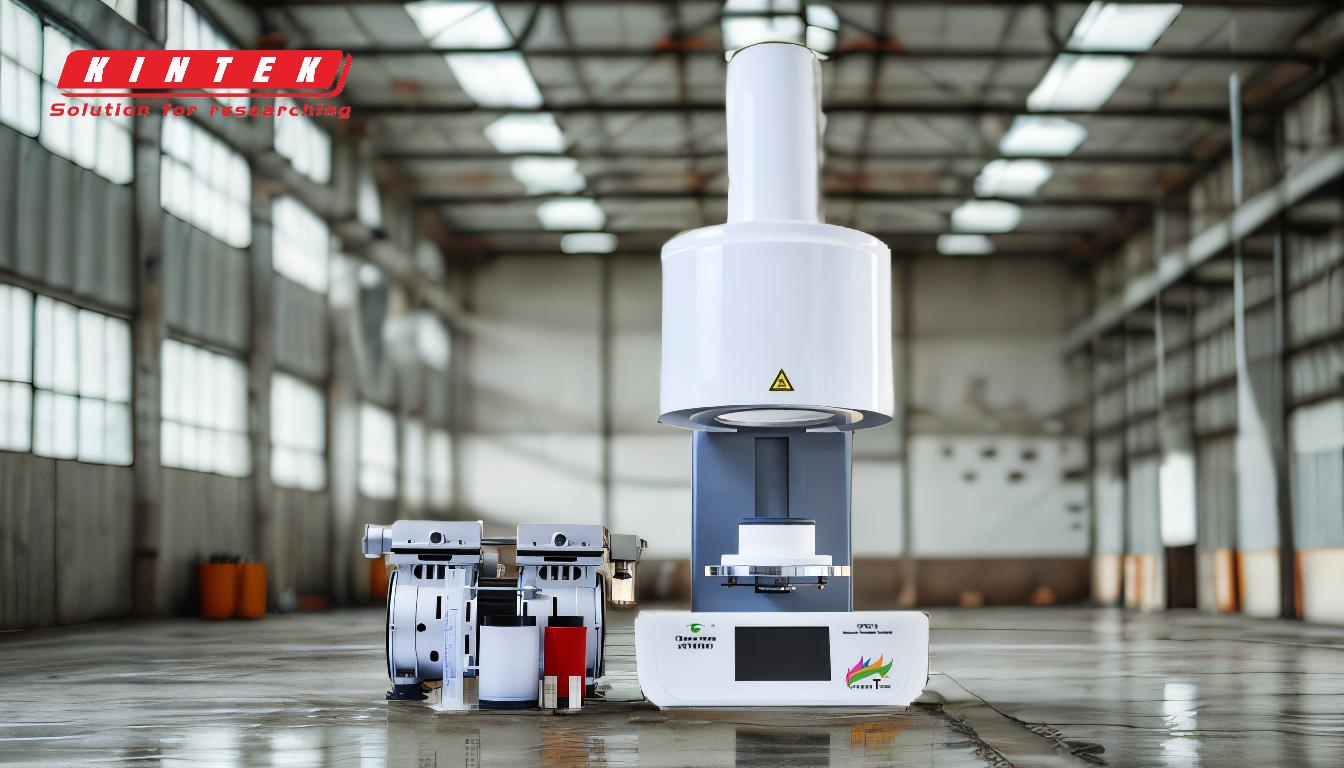
-
Precise Temperature Control and Uniform Heating
- Vacuum furnaces provide excellent temperature control, allowing for precise regulation within a wide range (800–3,000°C or 1,500–5,400°F). This ensures uniform temperature distribution across the heating zone, which is critical for consistent and repeatable results.
- Uniform heating minimizes thermal stress and deformation, leading to higher product pass rates and improved dimensional stability.
-
Low Contamination and High Purity
- The vacuum environment eliminates exposure to reactive gases like oxygen and carbon, reducing contamination of the workpiece. This results in higher purity and cleaner surfaces, free from oxidation, decarburization, or carburization.
- Vacuum pumping systems remove byproducts and impurities, further enhancing the quality of the treated materials.
-
Rapid Cooling (Quenching)
- Vacuum furnaces enable rapid cooling or quenching, which shortens process cycle times and improves the mechanical properties of materials. This is particularly beneficial for achieving desired hardness, strength, and wear resistance in treated components.
-
Computer-Controlled Processes for Repeatability
- Advanced vacuum furnaces are equipped with computer-controlled systems that ensure precise and repeatable heat treatment processes. This is essential for metallurgical applications requiring consistent results across multiple batches.
-
No Oxidation and Surface Purification
- The absence of oxygen in the vacuum environment prevents oxidation during high-temperature heating. This results in bright surface purification, degreasing, and degassing, which are crucial for achieving high-quality finishes.
- Surface impurities like phosphorus chips are also removed, enhancing the material's performance and longevity.
-
Energy Efficiency and Environmental Benefits
- Vacuum furnaces are designed with advanced insulation materials and control systems that minimize heat loss and optimize energy consumption. This makes the process energy-efficient and cost-effective.
- The vacuum firing process produces little to no pollution, ensuring a safe and environmentally friendly working environment.
-
Versatility in Heat Treatment Applications
- Vacuum furnaces support a wide range of heat treatment processes, including annealing, brazing, sintering, tempering, and hardening. This versatility makes them suitable for various industries, from aerospace to electronics.
-
Improved Mechanical Properties and Service Life
- Materials treated in a vacuum furnace exhibit enhanced mechanical properties, such as increased hardness, strength, and wear resistance. These improvements extend the service life of components and reduce maintenance costs.
- The process also prevents hydrogen embrittlement, which can compromise the integrity of certain materials.
In summary, vacuum firing using a vacuum furnace provides a clean, controlled, and efficient method for heat treatment. Its ability to deliver precise temperature control, low contamination, rapid cooling, and improved material properties makes it an indispensable tool for industries requiring high-quality and durable components. The process is not only versatile and repeatable but also environmentally friendly, aligning with modern sustainability goals.
Summary Table:
Advantage | Description |
---|---|
Precise Temperature Control | Ensures uniform heating and minimizes thermal stress for consistent results. |
Low Contamination | Eliminates reactive gases, resulting in high-purity, oxidation-free surfaces. |
Rapid Cooling (Quenching) | Shortens cycle times and enhances hardness, strength, and wear resistance. |
Computer-Controlled Processes | Delivers repeatable and precise heat treatment for consistent outcomes. |
No Oxidation and Surface Purification | Prevents oxidation and removes impurities for high-quality finishes. |
Energy Efficiency | Minimizes heat loss and reduces energy consumption for cost-effective operations. |
Versatility | Supports annealing, brazing, sintering, tempering, and hardening applications. |
Improved Mechanical Properties | Enhances hardness, strength, and service life of treated materials. |
Unlock the full potential of vacuum firing for your heat treatment needs—contact our experts today!