Vacuum deposition is a versatile and widely used process across various industries due to its ability to create thin, uniform, and high-performance coatings on different substrates. It is employed in applications ranging from enhancing the functionality of electronic devices to improving the durability and aesthetics of consumer products. Key industries utilizing vacuum deposition include semiconductor manufacturing, solar energy, medical devices, aerospace, automotive, and packaging. The process is essential for creating coatings such as optical, mirror, decorative, wear-resistant, and corrosion-protective layers, as well as for producing functional films like conductive layers and permeation barriers. Its applications are critical in advancing technologies such as thin-film solar cells, flexible displays, and energy-efficient devices.
Key Points Explained:
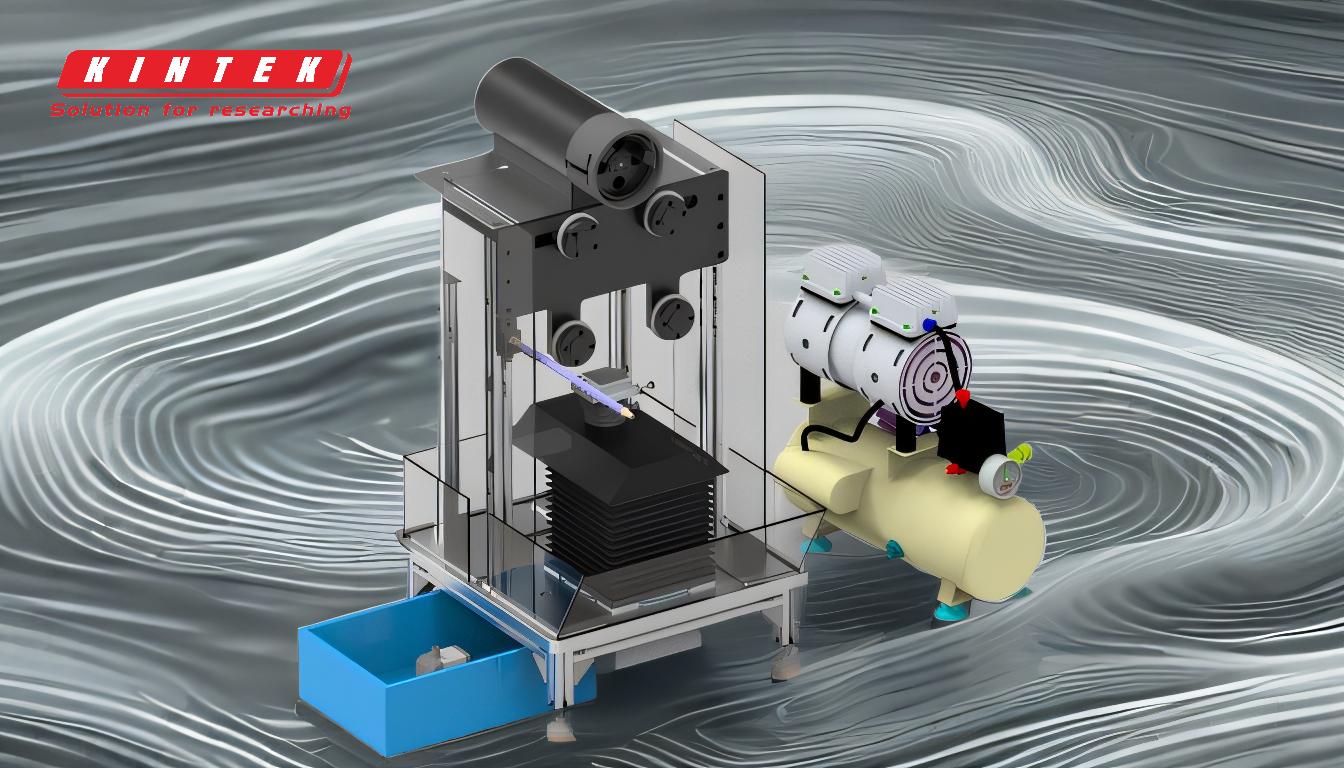
-
Semiconductor and Electronics Manufacturing:
- Vacuum deposition is crucial in the production of microchips, LEDs, and thin-film transistors. It is used to deposit conductive metal patterns and insulating layers, which are essential for the functionality of electronic devices.
- The process enables the creation of high-precision coatings required for semiconductor devices, ensuring optimal performance and miniaturization.
-
Solar Energy Applications:
- In thin-film solar cell manufacturing, vacuum deposition is used to enhance conductivity and light absorption properties. This improves the efficiency and durability of solar cells.
- The process allows for the deposition of multiple layers with precise thicknesses, optimizing the energy conversion capabilities of solar panels.
-
Optical and Decorative Coatings:
- Vacuum deposition is widely used to create optical coatings, such as anti-reflective, mirror, and interference coatings, which are essential for lenses, mirrors, and displays.
- Decorative coatings are applied to products like automotive parts, jewelry, and consumer electronics to enhance their appearance and durability.
-
Wear-Resistant and Corrosion-Protective Coatings:
- The process is employed to deposit wear-resistant coatings on tools, machinery, and automotive components, extending their lifespan and performance.
- Corrosion-protective coatings are applied to metals and other materials used in harsh environments, such as aerospace and marine applications, to prevent degradation.
-
Flexible Packaging and Permeation Barriers:
- Vacuum deposition is used to create thin, flexible films that act as permeation barriers in packaging materials. These films protect products from moisture, oxygen, and other contaminants, extending shelf life.
- This application is particularly important in the food and pharmaceutical industries.
-
Medical Devices and In-Home Healthcare Products:
- The process is used to coat medical tools and devices, enhancing their functionality, biocompatibility, and resistance to wear and corrosion.
- In-home medical devices, such as sensors and diagnostic tools, benefit from vacuum-deposited coatings that improve accuracy and durability.
-
Aerospace and Automotive Industries:
- Vacuum deposition is used to apply coatings that improve the performance and longevity of aerospace components, such as turbine blades and sensors.
- In the automotive industry, it is used for decorative finishes, corrosion protection, and functional coatings on parts like mirrors and sensors.
-
Energy Conservation and Generation:
- The process is employed in the production of energy-efficient coatings for windows and other surfaces, reducing heat loss and improving insulation.
- It is also used in the manufacturing of magnetic films and diffusion barriers, which are critical for energy storage and conversion technologies.
-
Flexible Displays and Sensors:
- Vacuum deposition is essential for producing thin-film transistors used in flexible displays and sensors, enabling the development of bendable and lightweight electronic devices.
- This technology is driving innovation in wearable electronics, foldable smartphones, and other advanced consumer products.
By leveraging the precision and versatility of vacuum deposition, industries can achieve enhanced performance, durability, and functionality in their products, making it a cornerstone of modern manufacturing and technology development.
Summary Table:
Industry | Applications |
---|---|
Semiconductor Manufacturing | Microchips, LEDs, thin-film transistors, conductive patterns, insulating layers |
Solar Energy | Thin-film solar cells, light absorption, energy conversion optimization |
Optical Coatings | Anti-reflective, mirror, and interference coatings for lenses and displays |
Wear-Resistant Coatings | Tools, machinery, automotive components for extended lifespan |
Flexible Packaging | Permeation barriers for food and pharmaceutical packaging |
Medical Devices | Biocompatible coatings for tools, sensors, and diagnostic devices |
Aerospace & Automotive | Corrosion protection, decorative finishes, functional coatings |
Energy Conservation | Energy-efficient coatings for windows, magnetic films, diffusion barriers |
Flexible Displays | Thin-film transistors for wearable electronics, foldable smartphones |
Interested in how vacuum deposition can elevate your industry? Contact us today to learn more!