Carbon nanotubes (CNTs) are manufactured using a variety of techniques, each with its own advantages and limitations. The primary methods include chemical vapor deposition (CVD), catalytic chemical vapor deposition (CCVD), laser ablation, and arc discharge. Among these, CVD and CCVD are the most widely used due to their cost-effectiveness, structural controllability, and scalability. Emerging methods are also being explored, such as using green or waste feedstocks to reduce environmental impact. The choice of manufacturing technique depends on the desired properties of the CNTs, their intended applications, and environmental considerations.
Key Points Explained:
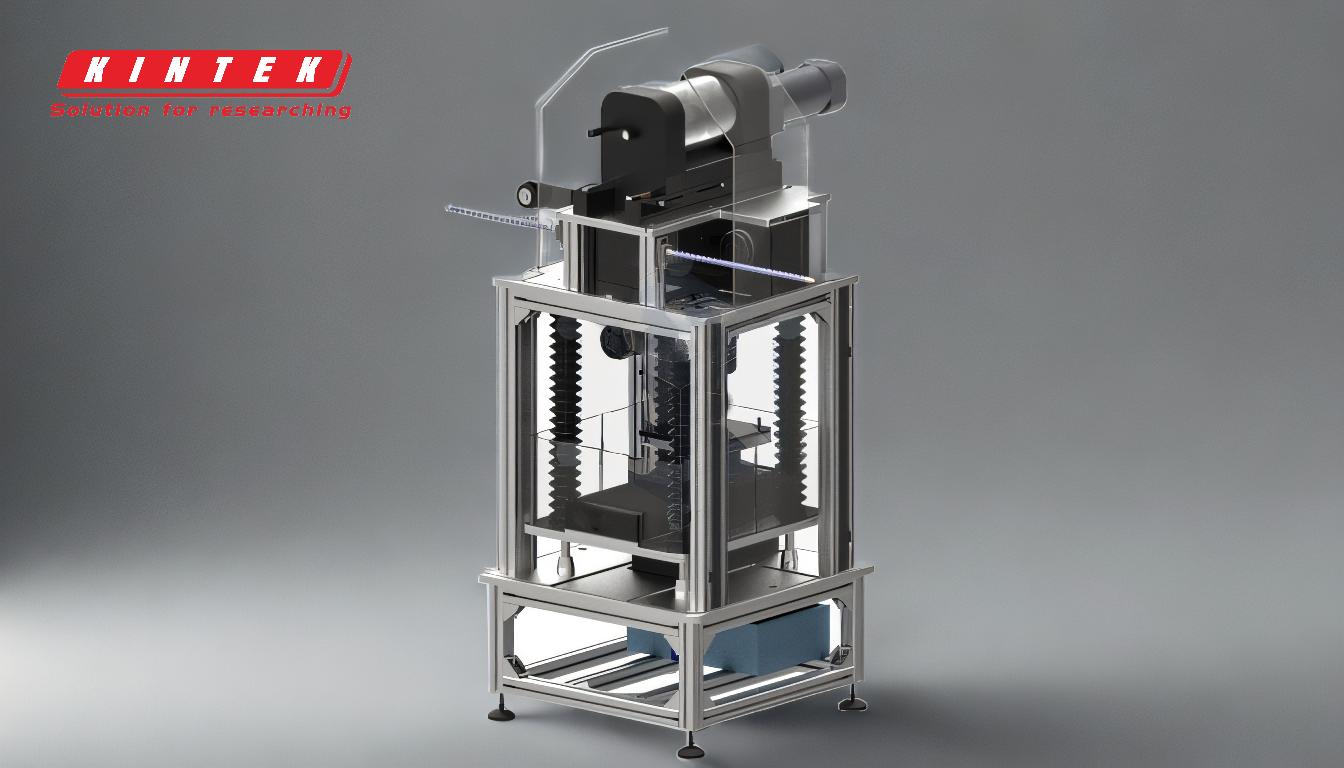
-
Chemical Vapor Deposition (CVD):
- CVD is the most dominant commercial process for CNT production today.
- It involves the decomposition of hydrocarbon gases at high temperatures in the presence of a catalyst, leading to the growth of CNTs on a substrate.
- Advantages include high yield, scalability, and the ability to control the structure and properties of the CNTs.
- The process is cost-effective and suitable for large-scale production, making it ideal for applications like lithium-ion batteries and composite materials.
-
Catalytic Chemical Vapor Deposition (CCVD):
- CCVD is a refined version of CVD and is considered the mainstream synthesis method.
- It offers better structural controllability and is more cost-effective than traditional CVD.
- The process involves thermal treatments and gas-phase rearrangement, which are critical for achieving high-quality CNTs.
- CCVD is particularly advantageous for applications requiring precise control over CNT properties, such as in conductive polymers and thermal interface materials.
-
Laser Ablation:
- This method involves using a high-power laser to vaporize a carbon target in the presence of a catalyst.
- It produces high-quality CNTs with fewer defects compared to other methods.
- However, it is less cost-effective and scalable than CVD, making it less suitable for large-scale commercial production.
- Laser ablation is often used in research settings where high-quality CNTs are required.
-
Arc Discharge:
- Arc discharge involves creating an electric arc between two graphite electrodes in an inert gas atmosphere.
- This method produces CNTs with a high degree of crystallinity but is less controllable and scalable than CVD.
- It is also more energy-intensive and less cost-effective, limiting its use in commercial applications.
- Arc discharge is typically used for producing small quantities of high-quality CNTs for specialized applications.
-
Emerging Methods:
- New techniques are being developed to reduce the environmental impact of CNT production.
- These include using green or waste feedstocks, such as carbon dioxide captured by electrolysis in molten salts and methane pyrolysis.
- These methods aim to make CNT production more sustainable by reducing material consumption, energy consumption, and greenhouse gas emissions.
- Emerging methods are particularly relevant for applications where environmental impact is a critical consideration, such as in transparent conductive films and sensors.
-
Environmental Considerations:
- The synthesis process is a major contributor to the life cycle ecotoxicity of CNTs.
- Efforts are being made to limit material consumption, energy consumption, and greenhouse gas emissions during production.
- Techniques like CCVD and emerging methods using green feedstocks are at the forefront of these efforts.
- Reducing the environmental impact of CNT production is crucial for their sustainable integration into various applications, including composite materials and energy storage devices.
In summary, the choice of CNT manufacturing technique depends on the specific requirements of the application, including the desired properties of the CNTs, production scale, and environmental considerations. CVD and CCVD are the most widely used methods due to their cost-effectiveness and scalability, while emerging methods are being developed to make CNT production more sustainable.
Summary Table:
Technique | Advantages | Limitations | Applications |
---|---|---|---|
CVD | High yield, scalable, cost-effective, controllable structure | Requires high temperatures and catalysts | Lithium-ion batteries, composite materials |
CCVD | Better structural controllability, cost-effective | Requires precise thermal and gas-phase treatments | Conductive polymers, thermal interface materials |
Laser Ablation | High-quality CNTs with fewer defects | Less cost-effective, limited scalability | Research settings requiring high-quality CNTs |
Arc Discharge | High crystallinity, produces high-quality CNTs | Energy-intensive, less scalable, limited commercial use | Specialized applications requiring small quantities |
Emerging Methods | Reduced environmental impact, sustainable feedstocks | Still under development, limited commercial adoption | Transparent conductive films, sensors, eco-friendly applications |
Ready to choose the right CNT manufacturing technique for your needs? Contact our experts today for personalized guidance!