An induction melting furnace is a highly efficient and clean method for melting metals, widely used in metal casting and foundry operations. Its core components include a power supply, an induction coil (or ring), and a crucible made of refractory materials. The furnace operates by generating a rapidly reversing magnetic field through an alternating electric current, inducing eddy currents in the metal charge. These currents heat the metal through Joule heating, ensuring uniform temperature and mixing. Additional systems, such as vacuum, water-cooling, hydraulic, and electrical control systems, may also be integrated depending on the furnace's design and application. The furnace's structure can vary, with vertical and horizontal configurations offering different discharge methods.
Key Points Explained:
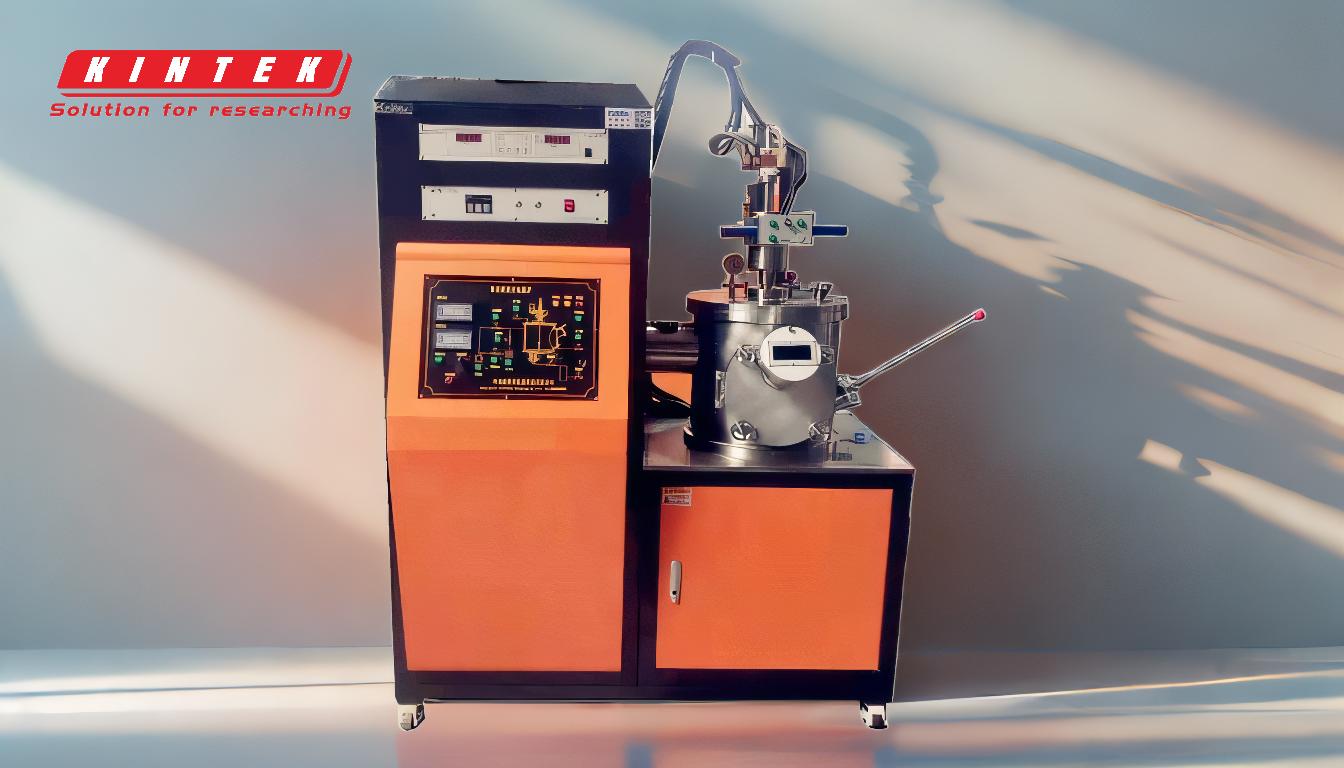
-
Power Supply:
- The power supply is the heart of the induction melting furnace, providing the alternating current (AC) necessary to generate the magnetic field.
- It typically operates at medium to high frequencies, depending on the desired penetration depth and heating efficiency.
- Higher frequencies result in shallower penetration, suitable for smaller or more precise melting applications.
-
Induction Coil (Induction Ring):
- The induction coil, often made of hollow copper tubing, surrounds the crucible and carries the alternating current.
- When energized, the coil generates a rapidly reversing magnetic field that penetrates the metal charge.
- The magnetic field induces eddy currents within the metal, which generate heat through resistance (Joule heating).
-
Crucible:
- The crucible is a container made of refractory materials, designed to withstand high temperatures and hold the metal charge.
- It acts as the secondary winding of a transformer, with the metal charge serving as the conductive medium.
- The choice of refractory material depends on the type of metal being melted and the operating temperature.
-
Metal Charge:
- The metal charge is the material to be melted, placed inside the crucible.
- It acts as the secondary winding of the transformer, where eddy currents are induced, generating heat and melting the metal.
- The stirring effect of the eddy currents ensures uniform temperature distribution and mixing.
-
Additional Systems (Optional, Depending on Design):
- Vacuum System: Used in vacuum induction melting furnaces to create a controlled atmosphere, preventing oxidation and contamination.
- Water-Cooling System: Cools the induction coil and other components to prevent overheating and ensure stable operation.
- Hydraulic and Pneumatic Systems: Facilitate the movement of components, such as tilting the furnace for pouring molten metal.
- Electrical Control System: Manages the power supply, frequency, and other operational parameters for precise control.
- Medium Frequency Power Supply: Provides the necessary frequency for efficient induction heating.
-
Structural Variations:
- Induction melting furnaces can be designed in vertical or horizontal configurations.
- Vertical Furnaces: Further divided into top-discharging, bottom-discharging, and side-discharging forms, depending on how the molten metal is removed.
- Horizontal Furnaces: Include bottom-discharging and top-discharging designs, offering flexibility in operation and integration with casting processes.
- Induction melting furnaces can be designed in vertical or horizontal configurations.
-
Working Principle:
- The furnace operates on the principle of electromagnetic induction, where an alternating current in the induction coil generates a magnetic field.
- This magnetic field induces eddy currents in the metal charge, which heat the metal through resistance.
- The heat is generated internally within the metal, making the process efficient and reducing external heat losses.
-
Advantages of Induction Melting:
- Clean and Efficient: Heat is generated directly within the metal, minimizing energy waste and reducing environmental impact.
- Precise Control: The frequency and power of the induction current can be adjusted for specific melting requirements.
- Uniform Heating: Eddy currents ensure consistent temperature distribution and thorough mixing of the molten metal.
By understanding these components and their functions, a purchaser can make informed decisions about the type of induction melting furnace that best suits their needs, whether for small-scale precision work or large-scale industrial applications.
Summary Table:
Component | Function |
---|---|
Power Supply | Provides alternating current (AC) to generate the magnetic field. |
Induction Coil | Generates a magnetic field to induce eddy currents in the metal charge. |
Crucible | Holds the metal charge and withstands high temperatures. |
Metal Charge | Acts as the secondary winding, where eddy currents generate heat. |
Additional Systems | Includes vacuum, water-cooling, hydraulic, and electrical control systems. |
Structural Variations | Vertical or horizontal configurations with different discharge methods. |
Advantages | Clean, efficient, precise control, and uniform heating. |
Discover the perfect induction melting furnace for your needs—contact our experts today!