Heat treatment is a critical process in metallurgy and materials science, involving controlled heating and cooling to alter the physical and mechanical properties of metals and alloys. The conditions in heat treatment vary depending on the desired outcome, such as hardening, softening, stress relief, or improving resilience. Processes like annealing, hardening, case hardening, and stress relief are commonly used, each requiring specific temperature ranges, cooling rates, and environmental controls to achieve the desired material properties. The conditions must be carefully managed to avoid adverse effects, such as oxidation, while ensuring the material achieves the intended microstructure and mechanical characteristics.
Key Points Explained:
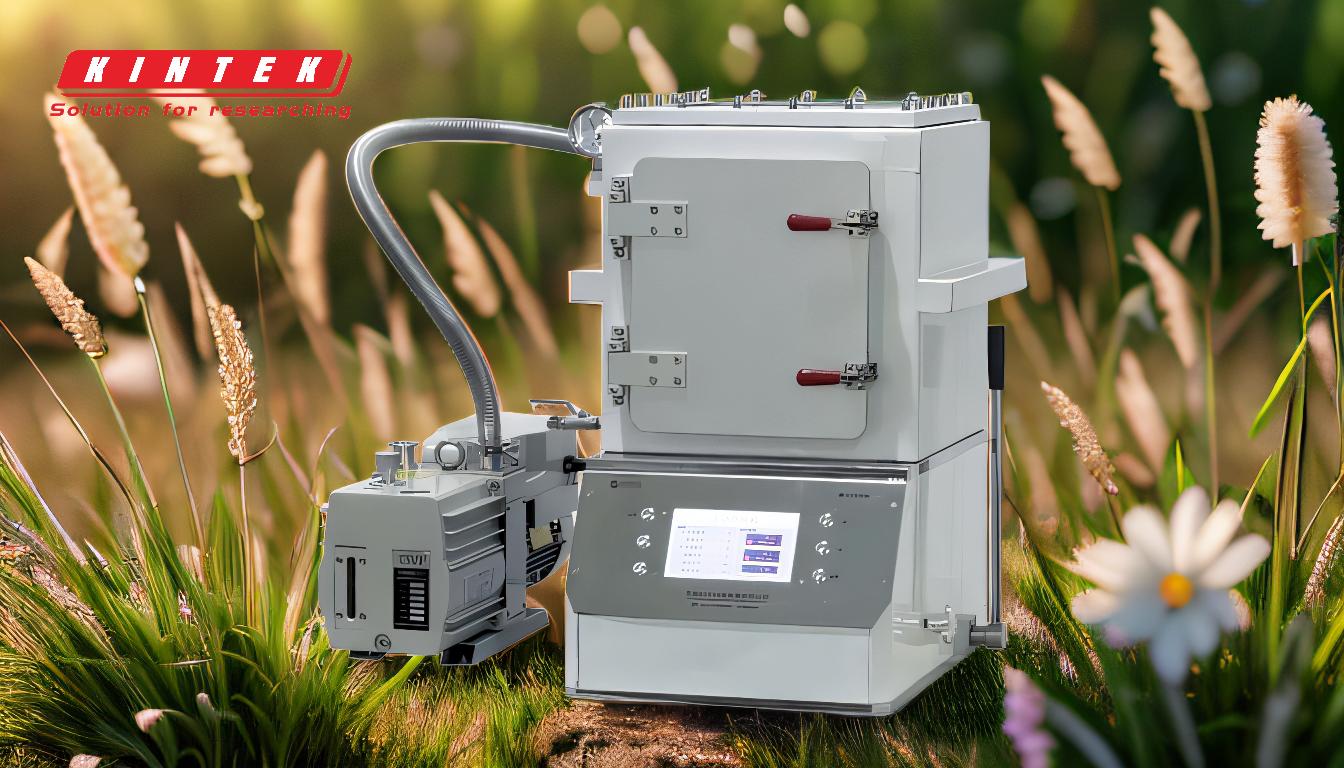
-
Types of Heat Treatment Processes:
- Annealing: This process involves heating the material to a specific temperature and then cooling it slowly to soften the metal, improve ductility, and relieve internal stresses. It is commonly used for metals and plastics.
- Hardening: Through-hardening and case hardening are methods to increase the hardness of metals. Through-hardening involves heating the entire material and then quenching it, while case hardening only hardens the surface layer.
- Stress Relief: This process is used to remove internal stresses caused by machining, forming, or welding. It involves heating the material to a lower temperature than annealing and then cooling it slowly.
- Specialized Processes: Techniques like austempering and marquenching are used to add resilience or springiness to metals, while magnetic annealing alters magnetic permeability.
-
Temperature Control:
- Heat treatment processes require precise control of furnace temperatures. For example, annealing typically involves heating the material to a temperature above its recrystallization point but below its melting point.
- High temperatures are necessary for processes like hardening and case hardening, but they must be carefully managed to avoid oxidation or other surface defects.
-
Cooling Rates:
- The rate of cooling significantly impacts the material's final properties. Rapid cooling (quenching) is used in hardening to achieve high hardness, while slow cooling is employed in annealing to improve ductility and relieve stress.
- Specialized cooling methods, such as marquenching, involve interrupted cooling to achieve specific microstructures.
-
Environmental Conditions:
- Heat treatment often requires controlled atmospheres to prevent oxidation or other surface reactions. For example, inert gases or vacuum environments are used in processes like brazing or annealing to protect the material's surface.
- Oxygen exposure during high-temperature processes can lead to scaling or decarburization, which degrades the material's surface quality.
-
Material-Specific Considerations:
- Different materials require tailored heat treatment conditions. For instance, steel alloys have specific temperature ranges for processes like hardening or annealing, while non-ferrous metals like aluminum or copper have different requirements.
- The microstructure of the material, including grain size and phase composition, plays a crucial role in determining the appropriate heat treatment conditions.
-
Mechanical Property Alteration:
- Heat treatment can enhance properties like hardness, strength, toughness, ductility, and elasticity. For example, through-hardening increases hardness and strength, while annealing improves ductility and reduces brittleness.
- The manipulation of diffusion rates and cooling rates within the microstructure is key to achieving these property changes.
-
Applications of Heat Treatment:
- Heat treatment is widely used in industries such as automotive, aerospace, construction, and manufacturing to improve the performance and durability of components.
- Specific applications include hardening gears, annealing injection-molded plastic parts, and stress-relieving welded structures.
By understanding and controlling these conditions, manufacturers can tailor the properties of materials to meet specific application requirements, ensuring optimal performance and longevity.
Summary Table:
Aspect | Details |
---|---|
Processes | Annealing, hardening, case hardening, stress relief, specialized techniques |
Temperature Control | Precise heating above recrystallization point, avoiding oxidation |
Cooling Rates | Rapid (quenching) for hardening, slow for annealing |
Environmental Control | Inert gases, vacuum environments to prevent oxidation |
Material-Specific | Tailored conditions for steel, aluminum, copper, and other alloys |
Property Alteration | Enhances hardness, strength, toughness, ductility, and elasticity |
Applications | Automotive, aerospace, construction, and manufacturing industries |
Discover how heat treatment can transform your materials—contact our experts today!