Carburization is a heat treatment process that introduces carbon into the surface of low-carbon steel, enhancing its hardness while maintaining a softer, more ductile core. While this process offers significant benefits, such as improved wear resistance and surface hardness, it can also lead to several types of damage if not properly controlled. These damages include embrittlement, reduced fatigue strength, and potential cracking or distortion of the material. Understanding these risks is crucial for ensuring the longevity and performance of carburized components.
Key Points Explained:
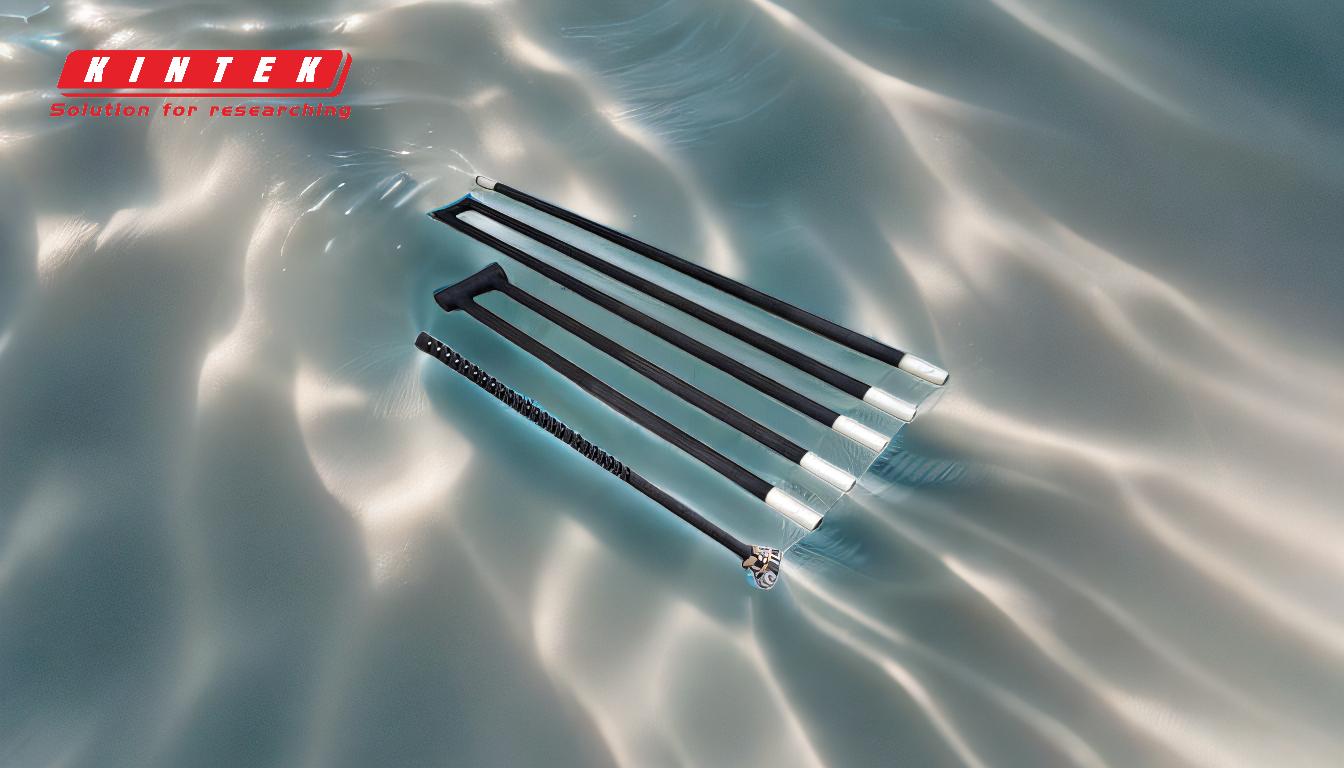
-
Embrittlement:
- Explanation: Carburization increases the carbon content at the surface, which can lead to the formation of brittle phases such as martensite. While martensite is hard, it is also prone to cracking under stress.
- Impact: This embrittlement can compromise the component's ability to withstand impact or cyclic loading, making it more susceptible to sudden failure.
- Mitigation: Proper tempering after carburization can reduce brittleness by transforming some martensite into tougher microstructures.
-
Reduced Fatigue Strength:
- Explanation: The high surface hardness achieved through carburization can create a sharp transition zone between the hardened surface and the softer core. This transition zone can act as a stress concentrator.
- Impact: Stress concentrations can initiate fatigue cracks, especially under cyclic loading conditions, reducing the component's overall fatigue life.
- Mitigation: Gradual carbon gradients and post-carburization treatments, such as shot peening, can help distribute stresses more evenly.
-
Cracking and Distortion:
- Explanation: The high temperatures involved in carburization can cause thermal stresses, leading to distortion or warping of the component. Additionally, rapid cooling (quenching) can induce cracking.
- Impact: Cracks and distortions can render the component unusable, requiring costly repairs or replacements.
- Mitigation: Controlled heating and cooling rates, along with proper fixture design, can minimize these risks.
-
Oxidation and Decarburization:
- Explanation: During the carburization process, exposure to oxygen can lead to surface oxidation or decarburization, where carbon is lost from the surface.
- Impact: Oxidation and decarburization can degrade the surface properties, reducing hardness and wear resistance.
- Mitigation: Using protective atmospheres or vacuum carburizing can prevent oxidation and decarburization.
-
Non-Uniform Case Depth:
- Explanation: Inconsistent carburization can result in uneven case depths, where some areas are over-carburized while others are under-carburized.
- Impact: Non-uniform case depths can lead to inconsistent mechanical properties, compromising the component's performance.
- Mitigation: Precise control of process parameters, such as temperature and gas composition, ensures uniform case depth.
-
Residual Stresses:
- Explanation: The carburization process, particularly quenching, can introduce residual stresses in the material.
- Impact: These stresses can lead to dimensional instability or premature failure under load.
- Mitigation: Stress-relief treatments, such as tempering, can alleviate residual stresses.
-
Cost and Complexity:
- Explanation: Carburization requires specialized equipment and precise control of process parameters, increasing production costs and complexity.
- Impact: Higher costs and complexity can make carburization less feasible for certain applications.
- Mitigation: Optimizing process parameters and selecting appropriate materials can help balance cost and performance.
By understanding these potential damages and implementing appropriate mitigation strategies, the benefits of carburization can be maximized while minimizing risks. This ensures that carburized components achieve the desired balance of hardness, durability, and performance.
Summary Table:
Damage Type | Explanation | Impact | Mitigation |
---|---|---|---|
Embrittlement | Increased carbon content forms brittle phases like martensite. | Susceptible to cracking under stress, leading to sudden failure. | Proper tempering to transform martensite into tougher microstructures. |
Reduced Fatigue Strength | Sharp transition zones act as stress concentrators. | Fatigue cracks initiate, reducing component life. | Gradual carbon gradients and shot peening. |
Cracking and Distortion | High temperatures cause thermal stresses; rapid cooling induces cracks. | Component warping or cracking, requiring costly repairs. | Controlled heating/cooling rates and proper fixture design. |
Oxidation and Decarburization | Exposure to oxygen leads to surface oxidation or carbon loss. | Degraded surface properties, reducing hardness and wear resistance. | Protective atmospheres or vacuum carburizing. |
Non-Uniform Case Depth | Inconsistent carburization results in uneven case depths. | Inconsistent mechanical properties, compromising performance. | Precise control of temperature and gas composition. |
Residual Stresses | Quenching introduces residual stresses. | Dimensional instability or premature failure under load. | Stress-relief treatments like tempering. |
Cost and Complexity | Requires specialized equipment and precise process control. | Higher costs and complexity, making it less feasible for some applications. | Optimize process parameters and select appropriate materials. |
Ensure your carburized components perform optimally—contact our experts today for tailored solutions!