Calcination is a thermal treatment process used to induce chemical or physical changes in materials by heating them below their melting point, typically in the absence or limited supply of air. This process is widely used in industries such as metallurgy, ceramics, and chemical manufacturing to extract metals, remove volatile substances, or achieve phase transitions. The types of calcination vary based on the materials being processed, the desired outcomes, and the equipment used. Common calcination methods include thermal decomposition, oxidation, reduction, and phase transition calcination. The equipment used for calcination, such as muffle, reverberatory, or shaft furnaces, plays a critical role in achieving the required temperature and atmospheric conditions.
Key Points Explained:
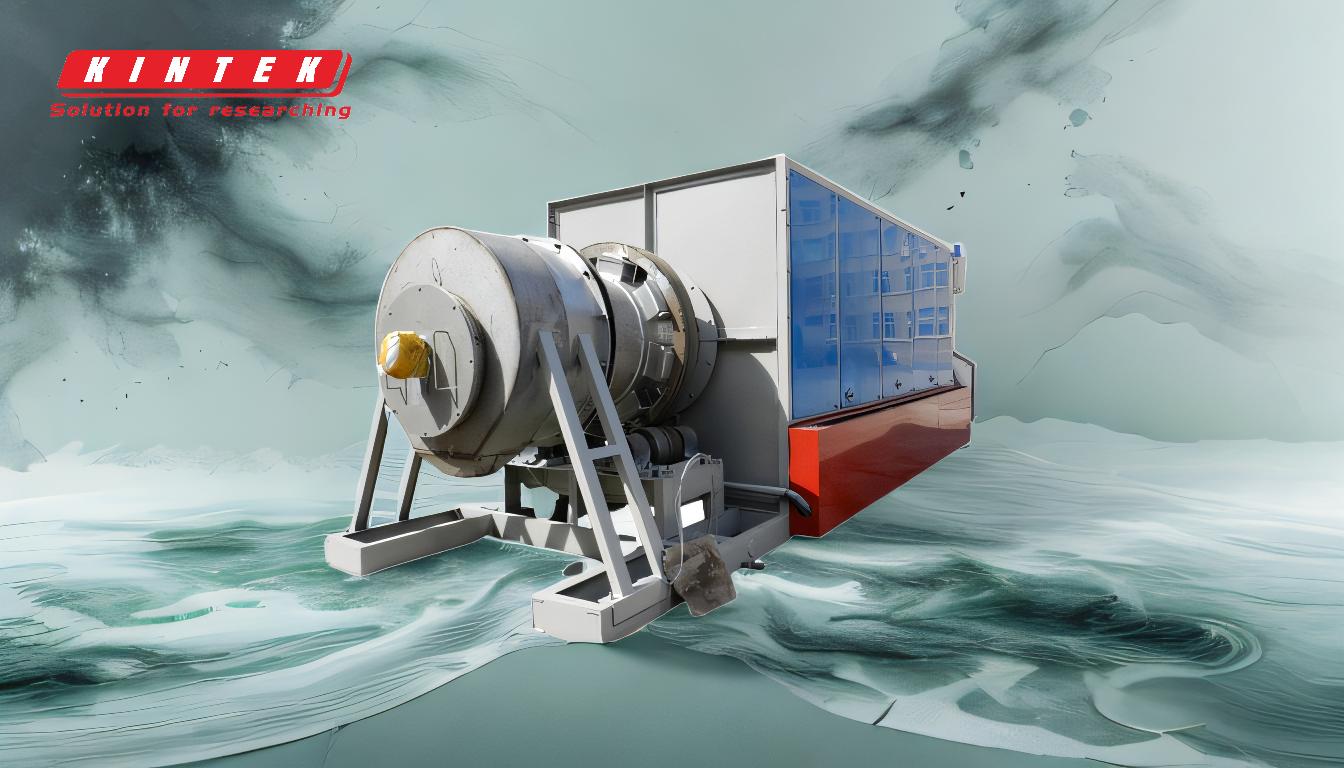
-
Thermal Decomposition Calcination:
- This type of calcination involves heating a material to break it down into simpler compounds or elements. For example, calcium carbonate (CaCO₃) decomposes into calcium oxide (CaO) and carbon dioxide (CO₂) when heated.
- Applications: Used in the production of lime (CaO) from limestone (CaCO₃) and in the extraction of metals from ores.
- Equipment: Typically carried out in muffle furnaces or rotary kilns, which provide controlled heating environments.
-
Oxidation Calcination:
- In this process, materials are heated in the presence of oxygen or air to induce oxidation reactions. For instance, sulfide ores are calcined to convert metal sulfides into metal oxides.
- Applications: Commonly used in metallurgy to extract metals like zinc and copper from their sulfide ores.
- Equipment: Reverberatory furnaces are often used due to their ability to handle high temperatures and provide an oxidizing atmosphere.
-
Reduction Calcination:
- Reduction calcination involves heating materials in a reducing atmosphere (e.g., hydrogen or carbon monoxide) to remove oxygen or other volatile components. This process is used to produce metals or metal oxides in a reduced state.
- Applications: Used in the production of iron from iron ores and in the refining of metals.
- Equipment: Shaft furnaces or rotary kilns with controlled gas atmospheres are typically employed.
-
Phase Transition Calcination:
- This type of calcination aims to induce a phase change in the material, such as transforming a crystalline structure into an amorphous form or vice versa. It does not necessarily involve chemical decomposition.
- Applications: Used in the production of ceramics, where phase transitions improve material properties like hardness and thermal stability.
- Equipment: Muffle furnaces are commonly used for precise temperature control.
-
Equipment Used in Calcination:
- Muffle Furnaces: Provide a controlled environment for calcination, isolating the material from direct contact with combustion gases. Ideal for small-scale or precise applications.
- Reverberatory Furnaces: Designed for large-scale operations, these furnaces use reflected heat to achieve high temperatures and are suitable for oxidation calcination.
- Shaft Furnaces: Vertical furnaces used for continuous processing, often employed in reduction calcination.
- Rotary Kilns: Cylindrical furnaces that rotate to ensure uniform heating, commonly used for thermal decomposition and large-scale industrial processes.
-
Applications of Calcination:
- Metallurgy: Extracting metals from ores, such as producing lime for steelmaking or refining aluminum.
- Ceramics and Cement Production: Transforming raw materials like clay and limestone into usable forms.
- Chemical Industry: Producing catalysts, pigments, and other chemical compounds.
- Environmental Applications: Treating waste materials to remove harmful substances or recover valuable components.
In summary, calcination is a versatile process with various types tailored to specific industrial needs. The choice of calcination method and equipment depends on the material being processed and the desired outcome, making it a critical step in many manufacturing and extraction processes.
Summary Table:
Type of Calcination | Description | Applications | Equipment |
---|---|---|---|
Thermal Decomposition | Heating to break down materials into simpler compounds (e.g., CaCO₃ → CaO + CO₂). | Lime production, metal extraction | Muffle furnaces, rotary kilns |
Oxidation Calcination | Heating in the presence of oxygen to induce oxidation (e.g., metal sulfides → oxides). | Metallurgy (zinc, copper extraction) | Reverberatory furnaces |
Reduction Calcination | Heating in a reducing atmosphere to remove oxygen or volatile components. | Iron production, metal refining | Shaft furnaces, rotary kilns |
Phase Transition Calcination | Inducing phase changes in materials (e.g., crystalline to amorphous). | Ceramics production | Muffle furnaces |
Equipment | Key Features | Applications | |
Muffle Furnaces | Controlled environment, precise heating. | Small-scale, precise calcination | |
Reverberatory Furnaces | High temperatures, oxidizing atmosphere. | Large-scale oxidation calcination | |
Shaft Furnaces | Continuous processing, reducing atmosphere. | Reduction calcination | |
Rotary Kilns | Uniform heating, large-scale operations. | Thermal decomposition, industrial use |
Discover how calcination can optimize your industrial processes—contact our experts today!