Heat treatment processes are essential in modifying the physical and mechanical properties of materials, particularly metals, to achieve desired characteristics such as hardness, toughness, ductility, and strength. These processes involve controlled heating and cooling of materials to alter their microstructure. The main types of heat treatment include annealing, quenching, tempering, normalizing, and case hardening, among others. Each process serves a specific purpose, such as softening metal for machining, hardening it for durability, or relieving internal stresses. Additionally, vacuum heat treatment offers a controlled environment to prevent oxidation and contamination, ensuring high-quality results. Below, we explore the key types of heat treatment processes in detail.
Key Points Explained:
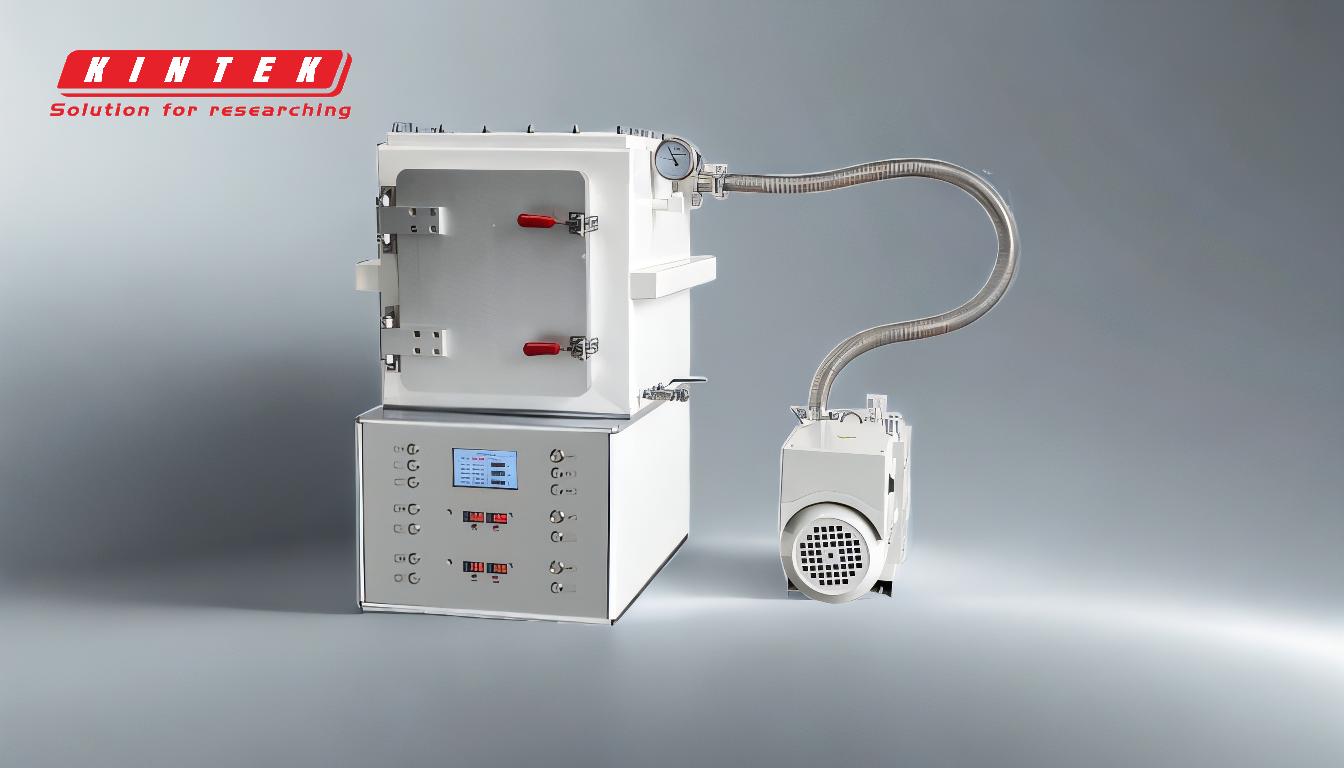
-
Annealing:
- Purpose: Annealing is used to soften metals, improve ductility, and relieve internal stresses. It involves heating the material to a specific temperature and then cooling it slowly, often in a furnace.
- Applications: Commonly used for materials that need to be machined or formed, as it makes them easier to work with.
- Types: Includes full annealing, process annealing, and stress relief annealing.
-
Quenching:
- Purpose: Quenching rapidly cools a heated metal to harden it. This process locks the material's microstructure in a hardened state.
- Cooling Media: Water, oil, brine, polymer solutions, and gases are commonly used as quenching media. About 90% of parts are quenched in water, oil, or polymers.
- Applications: Used for parts that require high hardness and wear resistance, such as gears and tools.
-
Tempering:
- Purpose: Tempering reduces the brittleness of quenched metals by reheating them to a lower temperature and then cooling them. This process improves toughness while maintaining hardness.
- Applications: Often used after quenching to achieve a balance between hardness and toughness in tools and structural components.
-
Normalizing:
- Purpose: Normalizing refines the grain structure of metals, improving their mechanical properties. It involves heating the material to a high temperature and then cooling it in air.
- Applications: Used to improve the machinability and strength of steel components.
-
Case Hardening:
- Purpose: Case hardening creates a hard outer layer while maintaining a softer, tougher core. Techniques include carburizing, nitriding, and induction hardening.
- Applications: Ideal for parts that require a wear-resistant surface, such as gears and shafts.
-
Vacuum Heat Treatment:
- Purpose: This method involves heat treating metals in a vacuum environment to prevent oxidation and contamination. It includes processes like vacuum annealing, vacuum quenching, and vacuum tempering.
- Applications: Used for high-precision components, such as aerospace and medical devices, where surface quality and consistency are critical.
-
Stress Relief:
- Purpose: Stress relief heat treatment removes internal stresses caused by machining, welding, or forming. It involves heating the material to a moderate temperature and then cooling it slowly.
- Applications: Essential for preventing distortion or cracking in machined or welded components.
-
Austempering and Marquenching:
- Purpose: These are specialized quenching processes that improve toughness and reduce distortion. Austempering involves quenching in a molten salt bath, while marquenching uses interrupted quenching to minimize thermal stress.
- Applications: Used for parts requiring high strength and minimal distortion, such as springs and automotive components.
-
Magnetic Annealing:
- Purpose: Magnetic annealing alters the magnetic properties of materials, such as mu metal, to achieve specific permeability characteristics.
- Applications: Used in the production of electrical and magnetic components.
-
Dehydroxylation:
- Purpose: This process removes hydroxyl groups from materials, often used in vacuum heat treatment to improve material properties.
- Applications: Common in advanced materials processing for electronics and optics.
By understanding these heat treatment processes, manufacturers can select the appropriate method to achieve the desired material properties for specific applications. Each process offers unique benefits and is tailored to meet the demands of various industries, from automotive to aerospace.
Summary Table:
Process | Purpose | Applications |
---|---|---|
Annealing | Softens metals, improves ductility, relieves internal stresses | Machining, forming materials |
Quenching | Rapidly cools metals to harden them | Gears, tools requiring high hardness |
Tempering | Reduces brittleness, improves toughness while maintaining hardness | Tools, structural components |
Normalizing | Refines grain structure, improves mechanical properties | Steel components requiring strength and machinability |
Case Hardening | Creates a hard outer layer with a tough core | Gears, shafts requiring wear resistance |
Vacuum Heat Treatment | Prevents oxidation and contamination in a vacuum environment | Aerospace, medical devices requiring high precision |
Stress Relief | Removes internal stresses from machining or welding | Machined or welded components to prevent distortion |
Austempering/Marquenching | Improves toughness, reduces distortion | Springs, automotive components requiring high strength |
Magnetic Annealing | Alters magnetic properties for specific permeability | Electrical and magnetic components |
Dehydroxylation | Removes hydroxyl groups to improve material properties | Electronics, optics, and advanced materials processing |
Need help selecting the right heat treatment process for your application? Contact our experts today for tailored solutions!