Thin film coatings are specialized layers applied to substrates to enhance their properties, such as durability, conductivity, or optical performance. These coatings are created using various deposition techniques, primarily categorized into physical vapor deposition (PVD) and chemical vapor deposition (CVD). The materials used for thin film coatings range from pure atomic elements (metals and non-metals) to complex molecules like nitrides and oxides. Thin film coating systems also vary in design, including batch systems, cluster tools, and laboratory-scale setups, each tailored for specific production volumes and applications. The choice of coating type and deposition method depends on the desired characteristics, such as transparency, scratch resistance, or electrical conductivity.
Key Points Explained:
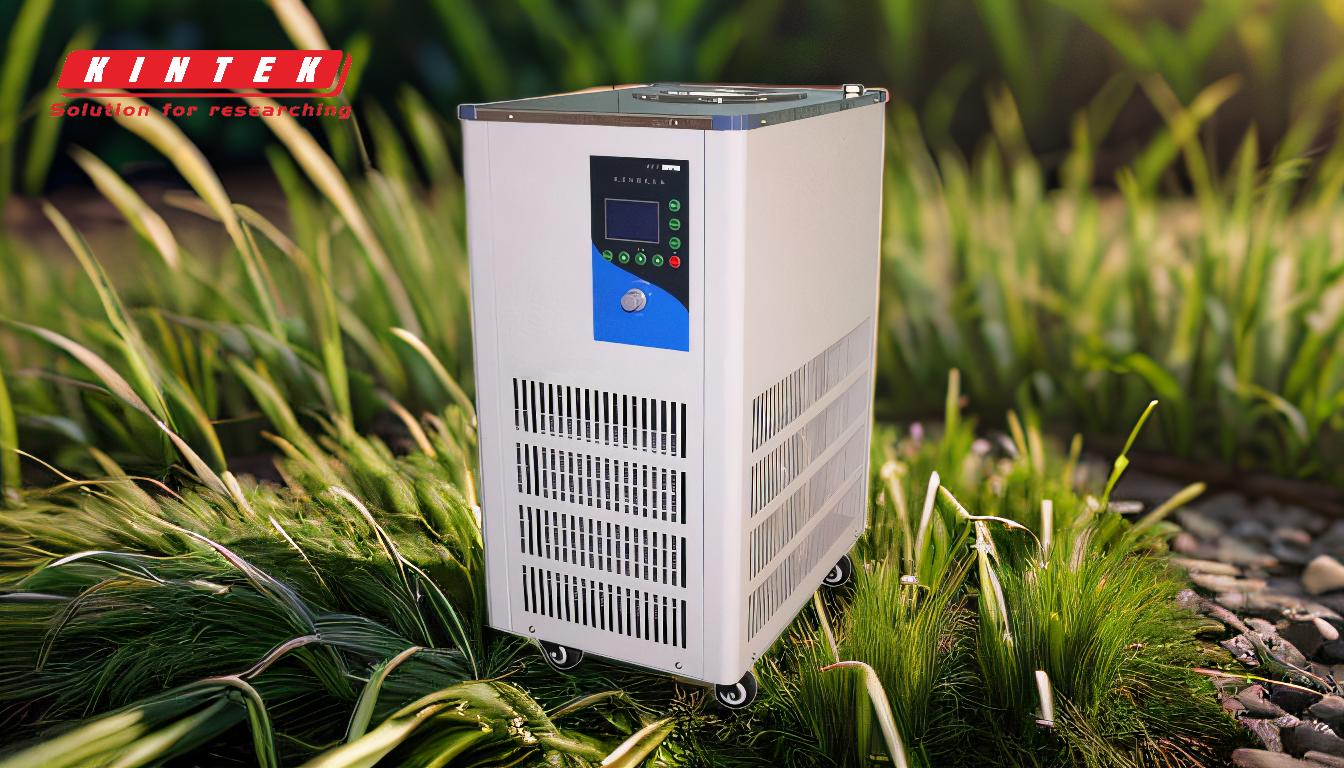
-
Categories of Thin Film Deposition Techniques:
- Thin film deposition methods are broadly classified into two main categories:
- Physical Vapor Deposition (PVD): This involves vaporizing a solid material in a vacuum and depositing it onto a substrate. Common PVD techniques include sputtering and evaporation.
- Chemical Vapor Deposition (CVD): This process uses chemical reactions to deposit a thin film on a substrate. CVD is often used for creating high-purity and high-performance coatings.
- A third category, liquid coating deposition, is also sometimes mentioned, which involves applying a liquid precursor to the substrate and then solidifying it.
- Thin film deposition methods are broadly classified into two main categories:
-
Materials Used in Thin Film Coatings:
- Thin film coatings can be made from a wide range of materials, including:
- Metals and Alloys: Used for conductive or reflective coatings.
- Inorganic Compounds: Such as nitrides and oxides, which provide hardness, corrosion resistance, or optical properties.
- Cermets and Intermetallics: These are composite materials combining ceramics and metals, often used for their unique mechanical and thermal properties.
- Interstitial Compounds: These materials are used for specialized applications requiring high strength and thermal stability.
- Thin film coatings can be made from a wide range of materials, including:
-
Characteristics of Thin Film Coatings:
- Thin film coatings are designed to impart specific properties to the substrate, such as:
- Transparency: Often used in optical applications like anti-reflective coatings.
- Durability and Scratch Resistance: Essential for protective coatings on surfaces exposed to wear.
- Electrical Conductivity or Insulation: Used in electronic and semiconductor applications.
- Signal Transmission Enhancement: Applied in telecommunications and optical devices.
- Thin film coatings are designed to impart specific properties to the substrate, such as:
-
Types of Thin Film Coating Systems:
- Thin film coating systems are designed to meet different production needs:
- Batch Systems: These process multiple wafers or substrates simultaneously, making them suitable for high-volume production.
- Cluster Tools: These systems use multiple chambers for different processes, allowing for sequential processing of single wafers.
- Factory or Freestanding Systems: Large-scale systems designed for high-volume industrial applications.
- Laboratory or Bench-Top Systems: Smaller systems used for research, development, or low-volume experimental applications.
- Thin film coating systems are designed to meet different production needs:
-
Applications of Thin Film Coatings:
- Thin film coatings are used in a variety of industries, including:
- Electronics: For semiconductor devices, sensors, and displays.
- Optics: For anti-reflective coatings, mirrors, and lenses.
- Automotive: For wear-resistant and decorative coatings.
- Aerospace: For thermal barrier coatings and corrosion protection.
- Medical Devices: For biocompatible and antimicrobial coatings.
- Thin film coatings are used in a variety of industries, including:
-
Advantages of Thin Film Coatings:
- Thin film coatings offer several benefits, such as:
- Precision: Ability to deposit very thin and uniform layers.
- Versatility: Can be applied to a wide range of materials and substrates.
- Enhanced Performance: Improves the functional properties of the substrate.
- Cost-Effectiveness: Reduces material usage while achieving desired properties.
- Thin film coatings offer several benefits, such as:
By understanding the different types of thin film coatings, their materials, deposition techniques, and applications, purchasers can make informed decisions about the best coating solutions for their specific needs.
Summary Table:
Category | Details |
---|---|
Deposition Techniques | - Physical Vapor Deposition (PVD): Sputtering, evaporation. |
- Chemical Vapor Deposition (CVD): High-purity, high-performance coatings. | |
- Liquid Coating Deposition: Liquid precursor application and solidifying. | |
Materials | - Metals and Alloys: Conductive or reflective coatings. |
- Inorganic Compounds: Nitrides, oxides for hardness, corrosion resistance. | |
- Cermets and Intermetallics: Ceramic-metal composites. | |
- Interstitial Compounds: High strength, thermal stability. | |
Characteristics | - Transparency, durability, scratch resistance, electrical conductivity. |
Coating Systems | - Batch Systems: High-volume production. |
- Cluster Tools: Sequential processing of single wafers. | |
- Factory Systems: Large-scale industrial applications. | |
- Laboratory Systems: Research and development. | |
Applications | - Electronics, optics, automotive, aerospace, medical devices. |
Advantages | - Precision, versatility, enhanced performance, cost-effectiveness. |
Discover the perfect thin film coating solution for your needs—contact our experts today!