Continuous furnaces, while efficient for large-scale production, come with several disadvantages that can affect their suitability for certain applications. They are more complex and expensive than batch furnaces, requiring frequent maintenance and specialized knowledge. Their operation at a constant temperature limits flexibility, making them unsuitable for processes requiring varied temperatures and durations. Additionally, they are less adaptable for small batches or complex geometries, consume more energy during continuous operation, and may not be ideal for melting large quantities of metal. These factors make continuous furnaces less versatile and more resource-intensive compared to other furnace types.
Key Points Explained:
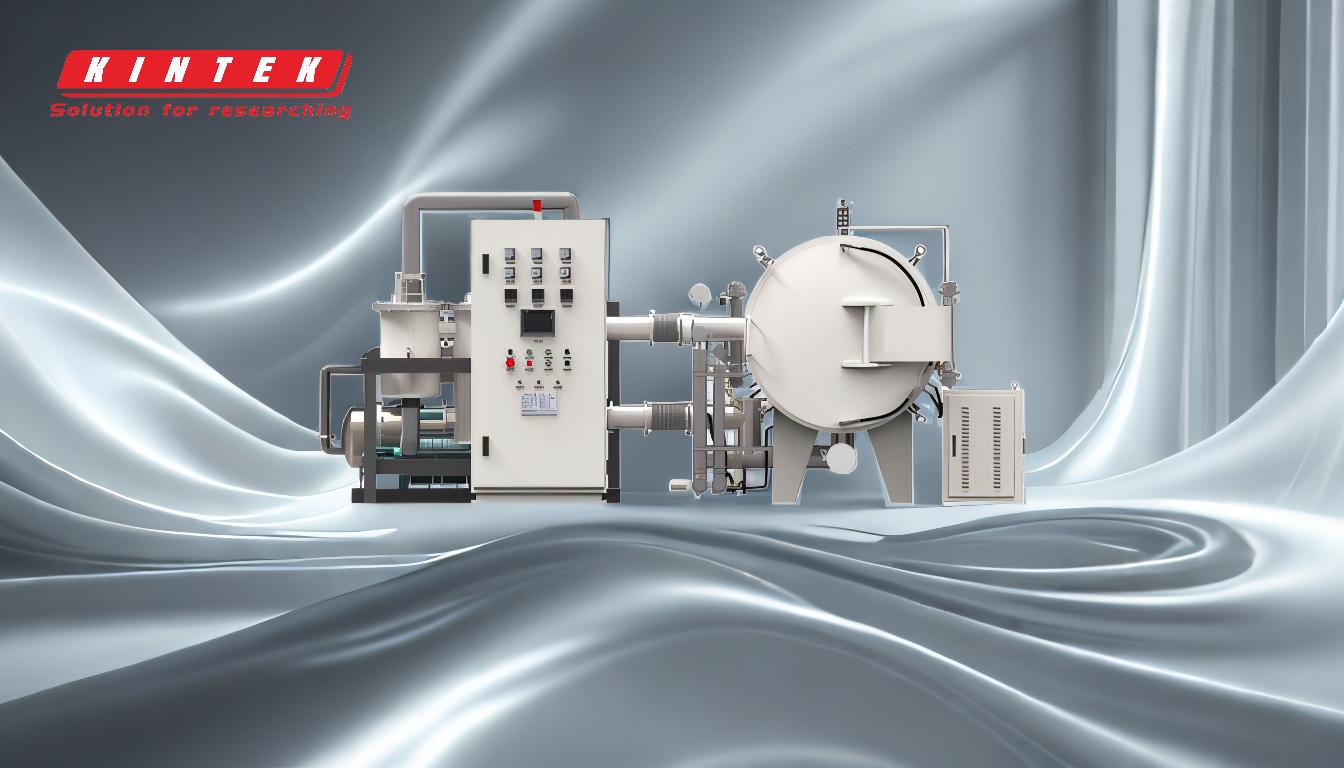
-
Higher Complexity and Cost:
- Continuous furnaces are more complex in design and operation compared to batch furnaces. This complexity translates to higher initial costs and ongoing expenses.
- The intricate mechanisms required for continuous operation, such as conveyor systems and temperature controls, contribute to the increased cost.
-
Frequent Maintenance Requirements:
- Due to their continuous operation, these furnaces experience more wear and tear, necessitating more frequent maintenance.
- The need for specialized knowledge and resources for maintenance adds to the operational costs and can lead to downtime if not properly managed.
-
Limited Temperature Flexibility:
- Continuous furnaces operate at a constant temperature, which cannot be easily adjusted. This rigidity means all items processed must be heated at the same temperature.
- This limitation can be a significant drawback for processes that require a range of temperatures or varying heat treatment durations.
-
Inflexibility with Small Batches and Complex Geometries:
- Continuous furnaces are designed for large-scale, uniform production and are less adaptable to small batches or items with complex shapes.
- The need for consistent speed and temperature makes it challenging to accommodate variations in product size or geometry.
-
Higher Energy Consumption:
- The continuous operation of these furnaces leads to higher energy consumption, especially during periods of low production or when idling.
- This increased energy use can result in higher operational costs and a larger environmental footprint.
-
Unsuitability for Large-Scale Metal Melting:
- Continuous furnaces, particularly resistance types, take longer to reach the necessary temperatures for melting metals.
- They are often unsuitable for melting large quantities of metal, making them less effective for certain mining or large-scale industrial applications.
-
Specialized Knowledge and Resources:
- The operation and maintenance of continuous furnaces require specialized knowledge and resources, which can be a barrier for smaller operations or those without access to expert personnel.
- This requirement can lead to increased training costs and reliance on external experts for troubleshooting and repairs.
In summary, while continuous furnaces offer advantages in terms of efficiency and throughput for large-scale production, their disadvantages in terms of cost, maintenance, flexibility, and energy consumption make them less suitable for certain applications. Understanding these limitations is crucial for making informed decisions when selecting a furnace type for specific industrial processes.
Summary Table:
Disadvantage | Description |
---|---|
Higher Complexity and Cost | More complex design and operation, leading to higher initial and ongoing costs. |
Frequent Maintenance | Requires more maintenance due to continuous operation, increasing downtime. |
Limited Temperature Flexibility | Operates at a constant temperature, unsuitable for varied heat treatment needs. |
Inflexibility with Small Batches | Less adaptable for small batches or complex geometries. |
Higher Energy Consumption | Continuous operation leads to increased energy use and operational costs. |
Unsuitable for Metal Melting | Not ideal for melting large quantities of metal, especially in resistance types. |
Specialized Knowledge Required | Demands expert personnel for operation and maintenance, raising training costs. |
Need help choosing the right furnace for your needs? Contact our experts today for tailored solutions!