Rotary kilns, while versatile and effective for various industrial processes, come with several disadvantages that can impact their efficiency, safety, and overall cost-effectiveness. Key issues include high capital and operating costs, low heat conversion efficiency, poor temperature control, safety hazards, environmental concerns, and challenges related to maintenance and material handling. These drawbacks can lead to reduced product quality, increased operational complexity, and higher regulatory scrutiny.
Key Points Explained:
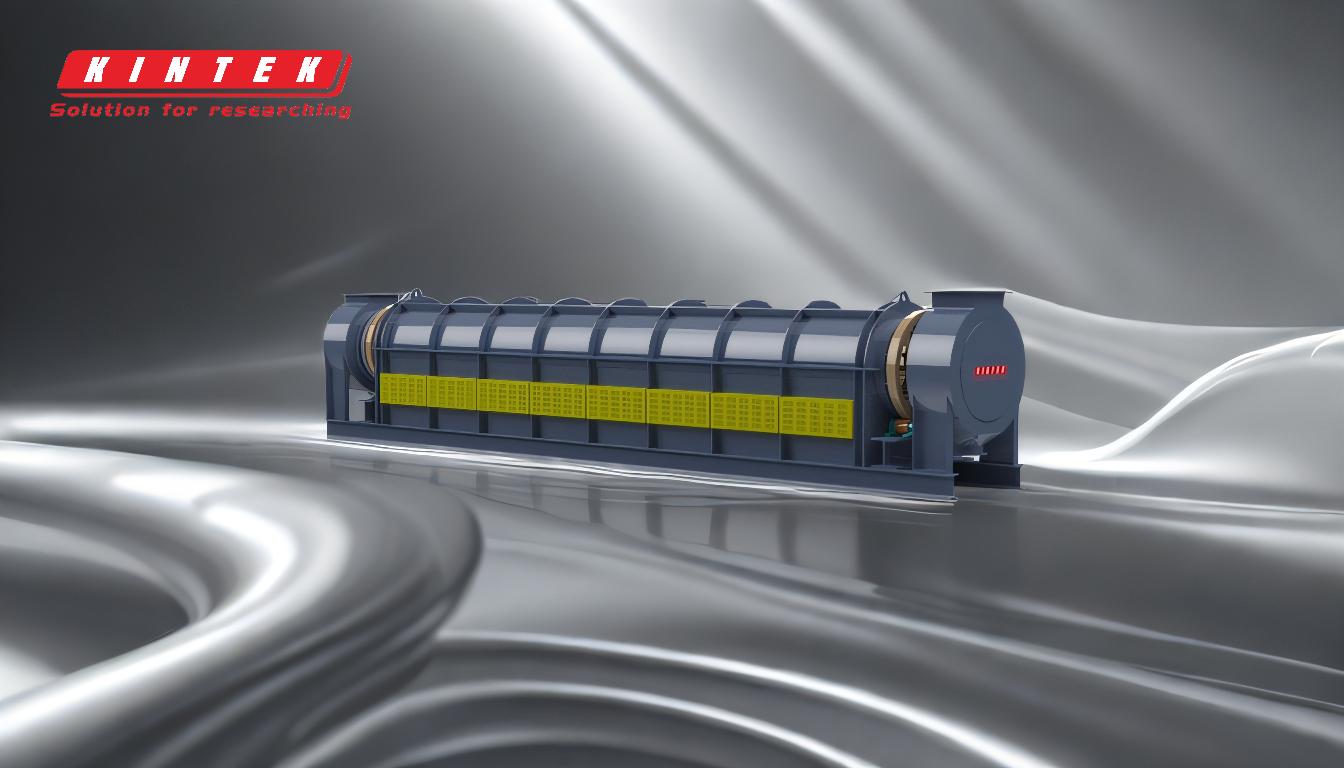
-
High Capital and Operating Costs:
- Capital Costs: Rotary kilns require significant initial investment due to their complex design and the need for high-quality materials to withstand extreme temperatures and mechanical stress.
- Operating Costs: The ongoing costs of running a rotary kiln are also high, including energy consumption, maintenance, and the need for skilled personnel to operate and maintain the equipment.
-
Low Heat Conversion Efficiency:
- Efficiency Issues: Traditional rotary kilns have a heat conversion efficiency of only 30%-70%, meaning a significant portion of the energy input is wasted.
- Impact on Operations: This inefficiency leads to higher fuel consumption and increased operational costs, making the process less economical.
-
Poor Temperature Control:
- Control Challenges: Maintaining precise temperature control in a rotary kiln is difficult, which can result in inconsistent product quality.
- Product Yield: Poor temperature control can lead to low product yield and color variations, affecting the overall quality and marketability of the final product.
-
Safety Hazards:
- Electrical and Gas Risks: Rotary kilns pose significant safety risks, including electric leakage, electric shock, and gas leakage fires.
- Operational Safety: These hazards require stringent safety measures and regular inspections to prevent accidents, adding to the operational complexity and cost.
-
Environmental Concerns:
- Pollution: Rotary kilns can produce significant environmental pollution, including dust and off-gases that require treatment.
- Regulatory Compliance: The environmental impact makes rotary kilns subject to strict environmental and safety regulations, which can increase compliance costs and operational challenges.
-
Maintenance and Lifespan Issues:
- Maintenance Intensity: Rotary kilns require frequent and intensive maintenance due to the harsh operating conditions, leading to high labor intensity and difficult maintenance procedures.
- Lifespan: The lifespan of rotary kilns can be relatively short, necessitating frequent replacements or major overhauls, which can be costly and disruptive.
-
Material Handling Challenges:
- Tumbling Issues: Not all materials tumble well in a rotary kiln, leading to poor mixing and large temperature variations.
- Efficiency Reduction: These material handling challenges can reduce the overall efficiency of the kiln, affecting the quality and consistency of the final product.
-
Installation and Alignment Problems:
- Installation Errors: Poor installation can result in damage to critical components such as wheels, tires, and the drum shell.
- Warranty and Re-work: Installation errors can lead to the need for re-work or voided warranties, adding to the overall cost and complexity of operating a rotary kiln.
In summary, while rotary kilns offer several advantages, their disadvantages—ranging from high costs and inefficiencies to safety and environmental concerns—make them a challenging choice for certain applications. Potential users must carefully weigh these drawbacks against the benefits to determine if a rotary kiln is the right solution for their needs.
Summary Table:
Disadvantage | Key Issues |
---|---|
High Capital and Operating Costs | Significant initial investment and ongoing energy, maintenance, and labor costs |
Low Heat Conversion Efficiency | 30%-70% efficiency, leading to wasted energy and higher operational costs |
Poor Temperature Control | Inconsistent product quality, low yield, and color variations |
Safety Hazards | Electric leakage, electric shock, and gas leakage fires |
Environmental Concerns | Dust and off-gas pollution, strict regulatory compliance |
Maintenance and Lifespan Issues | Frequent, intensive maintenance and short lifespan |
Material Handling Challenges | Poor mixing, temperature variations, and reduced efficiency |
Installation and Alignment Problems | Damage to components, re-work, and voided warranties |
Need help deciding if a rotary kiln is right for your application? Contact our experts today for tailored advice and solutions!