Air quenching, while commonly used in heat treatment processes, has several disadvantages, particularly when applied to materials like soda lime glass wafer. These drawbacks include uneven cooling rates, potential for thermal stress, and limitations in achieving specific material properties. Below, we explore these disadvantages in detail, focusing on their implications for materials and processes.
Key Points Explained:
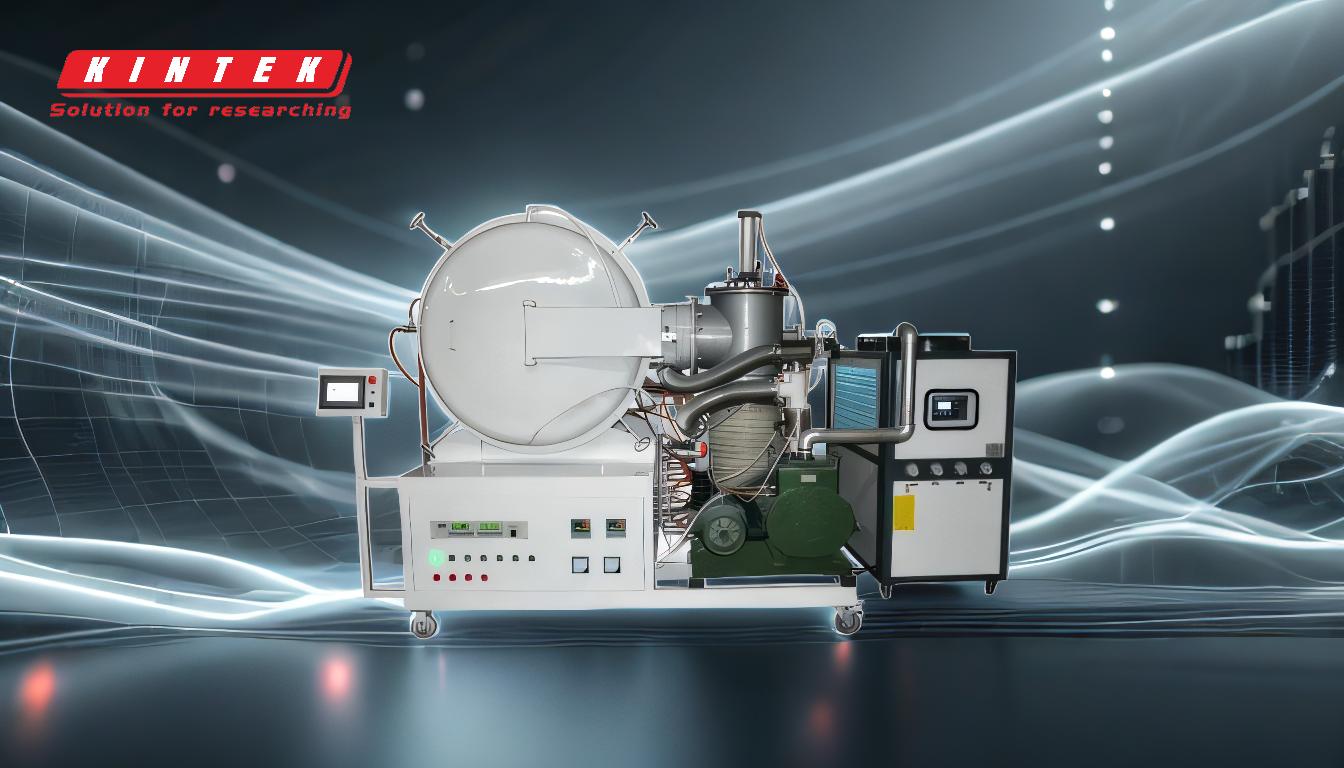
-
Uneven Cooling Rates:
- Air quenching relies on the circulation of air to remove heat from the material. However, air is a poor conductor of heat compared to liquids or gases like nitrogen. This results in uneven cooling rates across the material, especially for complex geometries or thin sections like soda lime glass wafers.
- Uneven cooling can lead to inconsistent material properties, such as hardness or strength, which are critical for applications requiring precision and uniformity.
-
Thermal Stress and Cracking:
- The slower and uneven cooling rates in air quenching can induce thermal stress within the material. This is particularly problematic for brittle materials like soda lime glass wafers, which are prone to cracking under stress.
- Thermal stress can also lead to warping or distortion, making the material unsuitable for applications requiring high dimensional accuracy.
-
Limited Control Over Cooling Rates:
- Unlike liquid quenching or high-pressure gas quenching, air quenching offers limited control over cooling rates. This makes it difficult to achieve specific microstructures or material properties that are critical for advanced applications.
- For example, certain alloys or glass materials may require rapid cooling to achieve desired hardness or transparency, which air quenching cannot reliably provide.
-
Environmental and Contamination Risks:
- Air quenching exposes the material to ambient air, which may contain contaminants like moisture, dust, or oxygen. These contaminants can react with the material surface, leading to oxidation or other undesirable chemical reactions.
- In the case of soda lime glass wafers, exposure to moisture or oxygen can compromise the optical properties or structural integrity of the material.
-
Energy Inefficiency:
- Air quenching often requires longer cooling times compared to other methods, leading to higher energy consumption and increased processing costs.
- The inefficiency of air as a cooling medium also limits its applicability in high-throughput industrial processes where time and energy savings are critical.
-
Incompatibility with Advanced Materials:
- Modern materials, including advanced ceramics, composites, and specialized glass like soda lime glass wafers, often require precise thermal management during cooling. Air quenching may not provide the necessary control or consistency for these materials.
- For instance, achieving the desired optical clarity or mechanical strength in soda lime glass wafers may require more advanced cooling techniques than air quenching can offer.
In summary, while air quenching is a simple and cost-effective method for some applications, its disadvantages—such as uneven cooling, thermal stress, limited control, contamination risks, energy inefficiency, and incompatibility with advanced materials—make it less suitable for precision applications involving materials like soda lime glass wafers. Alternative cooling methods, such as liquid or high-pressure gas quenching, may be more appropriate for achieving the desired material properties and performance.
Summary Table:
Disadvantage | Impact on Materials |
---|---|
Uneven Cooling Rates | Inconsistent hardness, strength, and material properties. |
Thermal Stress and Cracking | Risk of cracking, warping, or distortion in brittle materials. |
Limited Control Over Cooling | Difficulty achieving specific microstructures or properties. |
Environmental Contamination | Oxidation or chemical reactions due to exposure to moisture, dust, or oxygen. |
Energy Inefficiency | Longer cooling times, higher energy consumption, and increased costs. |
Incompatibility with Advanced Materials | Limited suitability for modern materials requiring precise thermal management. |
Discover better cooling solutions for your materials—contact our experts today!