Annealing, while beneficial for improving material properties like ductility and reducing internal stresses, does come with certain disadvantages. One significant drawback is its impact on mechanical properties, particularly in materials like X80 pipeline steel. For instance, low hydrogen annealing at 200 °C for 12 hours alters the stress-strain curve, leading to increased yield strength but reduced elongation. This occurs due to carbon atoms diffusing into interstitial sites of dislocations, forming a Cottrell atmosphere that pins dislocations, thereby reducing the density of movable dislocations. Such changes can compromise the material's performance in specific applications, highlighting the need for careful consideration of annealing parameters.
Key Points Explained:
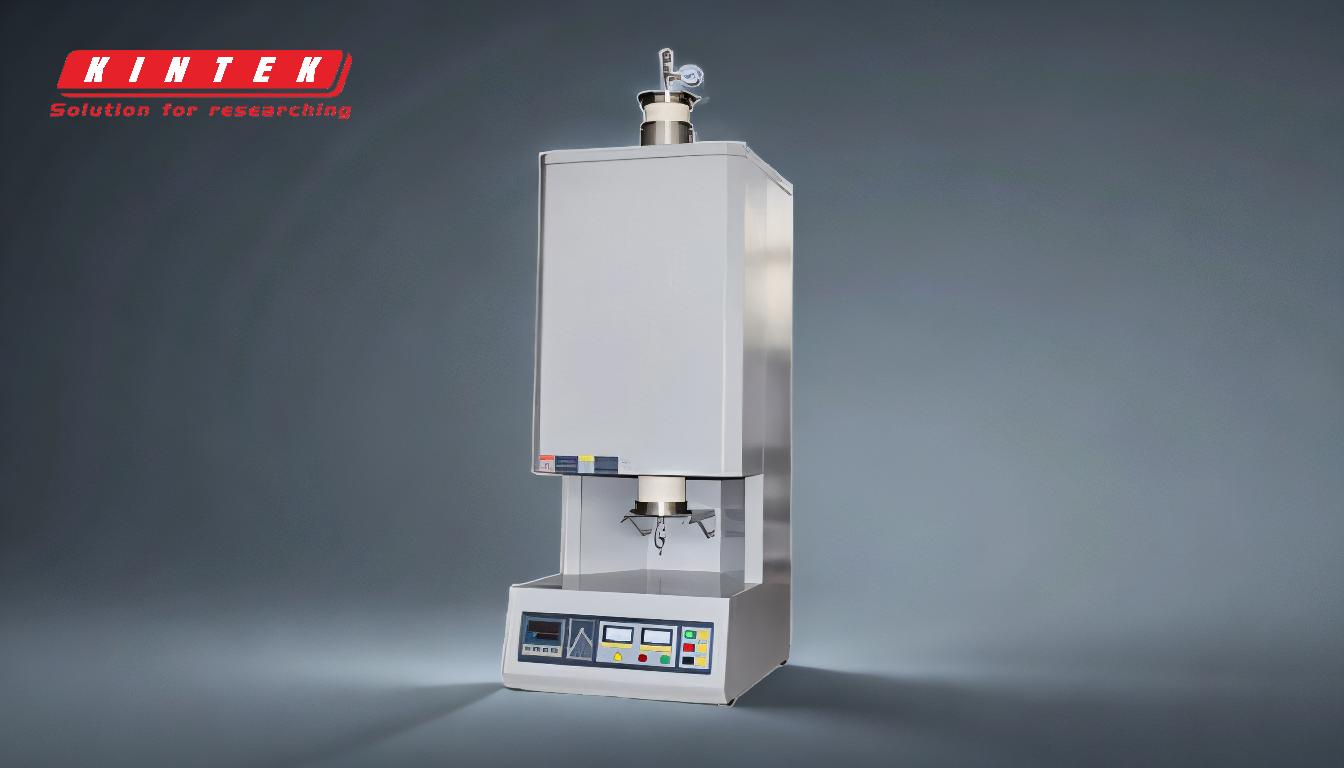
-
Alteration of Mechanical Properties:
- Yield Strength Increase: Annealing can lead to an increase in yield strength, as seen in X80 pipeline steel, where it rises by approximately 10%. This might seem beneficial, but it can also make the material more brittle.
- Reduction in Elongation: The elongation of the material decreases by about 20%, indicating a loss in ductility. This reduction can be detrimental in applications requiring material flexibility.
-
Formation of Cottrell Atmosphere:
- Carbon Atom Diffusion: During annealing, carbon atoms diffuse into the interstitial sites of dislocations. This process forms what is known as a Cottrell atmosphere.
- Pinning of Dislocations: The Cottrell atmosphere pins dislocations in place, which reduces the density of movable dislocations. This pinning effect is responsible for the observed changes in mechanical properties.
-
Impact on Material Performance:
- Reduced Ductility: The decrease in elongation signifies a reduction in the material's ability to deform plastically before fracturing, which can be a critical disadvantage in many engineering applications.
- Potential Brittleness: While increased yield strength might be desirable in some contexts, it often comes at the cost of increased brittleness, making the material more prone to cracking under stress.
-
Considerations for Application:
- Application-Specific Requirements: The disadvantages of annealing must be weighed against the specific requirements of the application. For instance, in applications where ductility is crucial, the reduction in elongation might be unacceptable.
- Optimization of Annealing Parameters: To mitigate these disadvantages, it is essential to optimize annealing parameters such as temperature and duration. This optimization can help achieve a balance between improved mechanical properties and minimal adverse effects.
In summary, while annealing can enhance certain material properties, it also poses significant disadvantages, particularly concerning mechanical performance. Understanding these drawbacks is crucial for making informed decisions in material processing and application.
Summary Table:
Disadvantage | Description |
---|---|
Increased Yield Strength | Yield strength rises by ~10%, but may lead to brittleness. |
Reduced Elongation | Elongation decreases by ~20%, reducing ductility and flexibility. |
Cottrell Atmosphere | Carbon atoms pin dislocations, reducing movable dislocations and altering properties. |
Potential Brittleness | Higher yield strength can make materials prone to cracking under stress. |
Application Limitations | Reduced ductility may be unsuitable for applications requiring material flexibility. |
Need help optimizing annealing processes for your materials? Contact our experts today for tailored solutions!