Cold working is a metalworking process that involves shaping metal at temperatures below its recrystallization point, typically at room temperature. While it offers several advantages, such as improved strength, surface finish, and dimensional accuracy, it also comes with notable disadvantages. These include increased material hardness, which can lead to brittleness, limited formability, and the need for intermediate annealing processes. Additionally, cold working can cause residual stresses, reduce ductility, and require higher forces and energy, making it less suitable for certain materials and applications. Understanding these drawbacks is crucial for selecting the appropriate manufacturing process for specific materials and desired outcomes.
Key Points Explained:
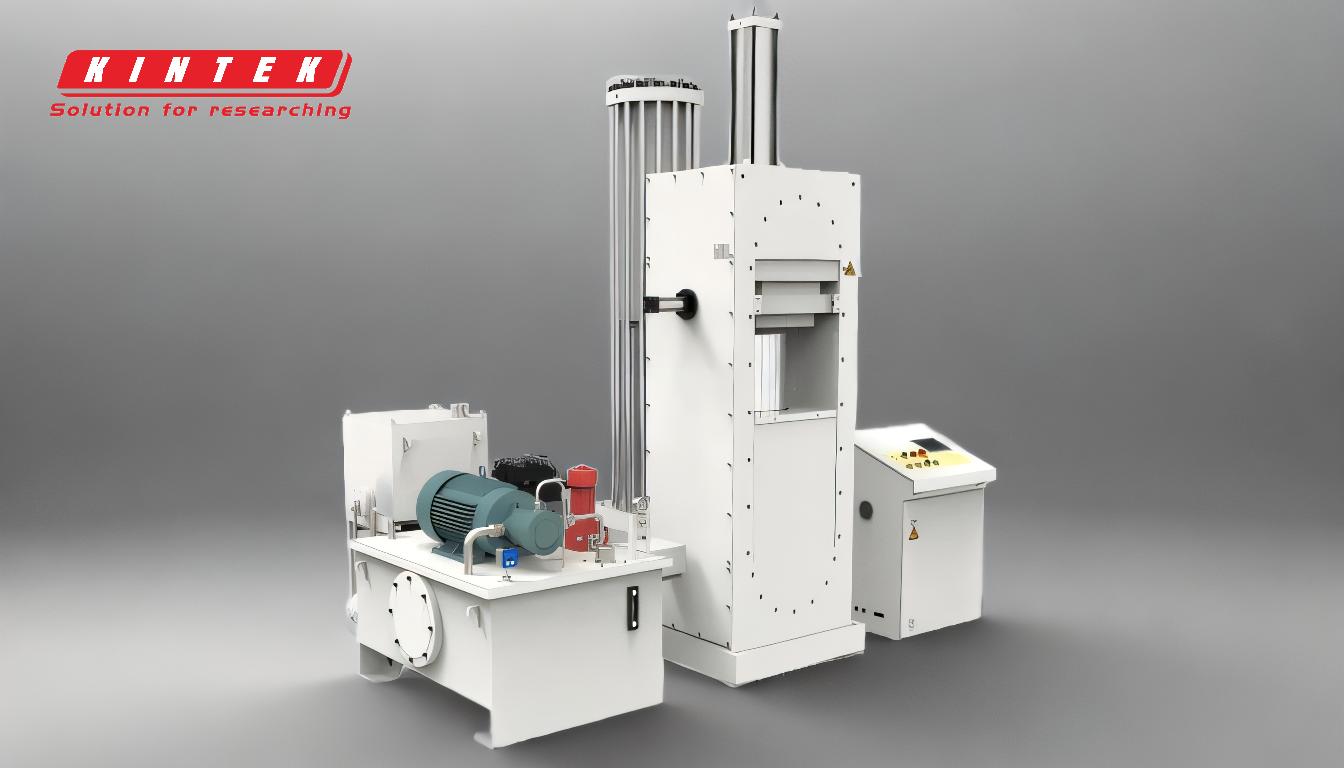
-
Increased Material Hardness and Brittleness
- Cold working strengthens metals by introducing dislocations in the crystal structure, but this also increases hardness and reduces ductility.
- Over time, the material may become too brittle, making it prone to cracking or failure under stress.
- This limitation makes cold working unsuitable for applications requiring high toughness or impact resistance.
-
Limited Formability
- Cold working reduces the ability of a material to undergo further deformation without cracking.
- Complex shapes or deep draws may require multiple stages of cold working, increasing production time and cost.
- Some materials, such as high-carbon steels or certain alloys, are particularly challenging to cold work due to their low ductility.
-
Residual Stresses
- Cold working introduces internal stresses within the material, which can lead to distortion or warping over time.
- These residual stresses may require additional processes, such as heat treatment or stress-relieving annealing, to stabilize the material.
- Without proper treatment, residual stresses can compromise the structural integrity of the final product.
-
Higher Forces and Energy Requirements
- Cold working requires significantly higher forces compared to hot working, as the material is less pliable at lower temperatures.
- This increases energy consumption and tool wear, raising operational costs.
- Specialized equipment and tooling may be needed to handle the increased forces, further adding to expenses.
-
Reduced Ductility
- The process reduces the material's ability to stretch or deform without breaking, which can limit its application in dynamic or high-stress environments.
- Materials with reduced ductility are less forgiving during manufacturing, increasing the likelihood of defects or scrap.
-
Need for Intermediate Annealing
- To counteract the effects of work hardening, intermediate annealing is often required to restore ductility and allow further deformation.
- This additional step increases production time, energy usage, and costs.
- Annealing must be carefully controlled to avoid altering the material's properties unintentionally.
-
Surface Imperfections
- While cold working improves surface finish in many cases, it can also introduce surface defects such as scratches, cracks, or uneven textures.
- These imperfections may require secondary finishing processes, adding to the overall cost and complexity.
-
Material Limitations
- Not all materials are suitable for cold working. For example, brittle materials like cast iron or certain ceramics cannot undergo significant cold deformation without cracking.
- Even ductile materials like aluminum or copper may have limitations depending on their alloy composition and initial condition.
-
Environmental and Safety Concerns
- The higher forces and energy requirements of cold working contribute to increased carbon emissions and environmental impact.
- Workers may also face safety risks due to the high pressures and forces involved, necessitating strict safety protocols and equipment.
By understanding these disadvantages, manufacturers can make informed decisions about when to use cold working and when alternative processes, such as hot working or casting, might be more appropriate.
Summary Table:
Disadvantage | Description |
---|---|
Increased Hardness & Brittleness | Strengthens metal but reduces ductility, leading to potential cracking or failure. |
Limited Formability | Reduces ability to deform without cracking, increasing production time and cost. |
Residual Stresses | Causes internal stresses, requiring heat treatment to stabilize the material. |
Higher Forces & Energy | Requires more force and energy, increasing operational costs and tool wear. |
Reduced Ductility | Limits material's ability to stretch or deform, increasing defect risks. |
Intermediate Annealing Needed | Restores ductility but adds time, energy, and cost to the process. |
Surface Imperfections | Can introduce scratches, cracks, or uneven textures, requiring secondary finishing. |
Material Limitations | Not suitable for brittle materials like cast iron or certain ceramics. |
Environmental & Safety Concerns | Higher energy use increases emissions; safety risks due to high forces involved. |
Need help choosing the right metalworking process? Contact our experts today for tailored solutions!