Crucibles are essential tools in metallurgy and material processing, but they come with several disadvantages that can impact their performance, cost, and safety. These include limitations in temperature range, material degradation, contamination risks, capacity constraints, and energy inefficiencies. Additionally, crucibles often require frequent replacement due to wear and tear, and certain types, like pure graphite or alumina crucibles, have specific vulnerabilities such as oxidation or high costs. Understanding these drawbacks is crucial for selecting the right crucible for specific applications and ensuring efficient and safe operations.
Key Points Explained:
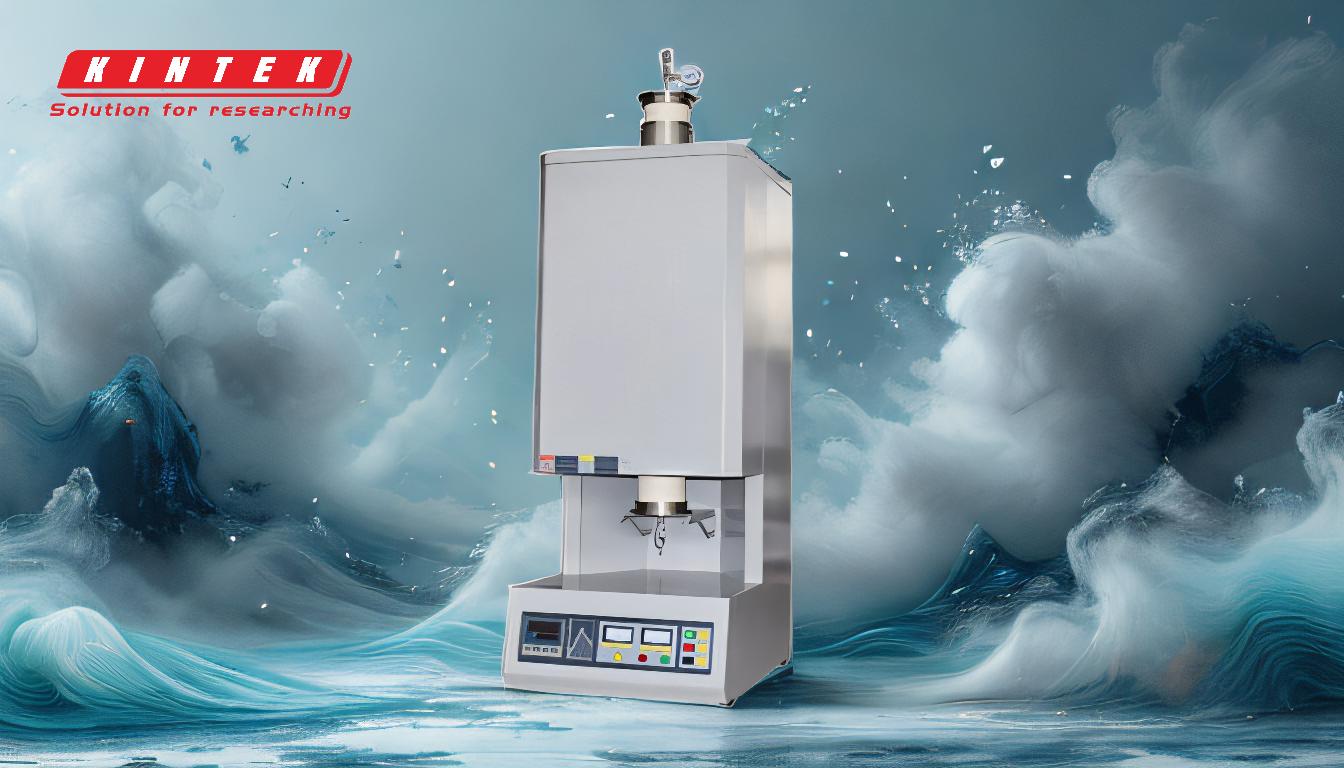
-
Temperature Limitations:
- High-Temperature Risks: Operating crucibles above their maximum temperature can lead to dangerous failures, such as cracking or melting of the crucible material.
- Low-Temperature Risks: Conversely, using crucibles below their lower temperature limit can cause issues like oxidation, especially when melting metals with lower melting points (e.g., zinc in a crucible designed for copper-based alloys).
-
Material Degradation and Contamination:
- Flaking and Scaling: Steel crucibles, while suitable for melting metals like aluminum and zinc, can experience flaking of the interior surface. This not only contaminates the melt but also thins the crucible walls, reducing its lifespan.
- Oxidation of Graphite: Pure graphite crucibles cannot be used in charcoal or carbon ovens as they begin to oxidize at temperatures as low as 400°C (752°F), leading to rusting and pausing.
-
Capacity Constraints:
- Limited Production Scale: Crucible furnaces have a limited capacity, making them unsuitable for industries requiring large-scale production. This limitation can hinder productivity and efficiency in high-volume operations.
-
Energy Inefficiency:
- Heat Loss in Water-Cooled Crucibles: Water-cooled crucibles suffer from significant heat losses through the crucible and melt contact areas. This limits the ability to achieve higher melt temperatures and results in low energy efficiency.
- High Energy Costs: The energy costs associated with floatation technology, often used with crucibles, represent a significant portion of the total cost of metal production.
-
High Costs and Low Thermal Conductivity:
- Alumina Crucibles: These crucibles are expensive compared to other materials and have a lower melting point, which can lead to alloy contamination. Additionally, their lower thermal conductivity can result in slower heating times and reduced efficiency.
-
Frequent Replacement and Maintenance:
- Wear and Tear: Crucibles are subject to wear and tear from high temperatures and repeated use, necessitating frequent replacement. This adds to operational costs and downtime.
- Coating Requirements: To mitigate some issues, such as flaking in steel crucibles, additional protective coatings like marcote-7 may be required, further increasing maintenance efforts and costs.
-
Oxidation and Rusting:
- Graphite Crucibles: Pure graphite crucibles are prone to oxidation at relatively low temperatures, making them unsuitable for certain environments and requiring careful handling and storage.
By considering these disadvantages, users can make informed decisions about the type of crucible to use, taking into account the specific requirements of their application and the potential trade-offs in terms of cost, efficiency, and safety.
Summary Table:
Disadvantage | Description |
---|---|
Temperature Limitations | High or low temperatures can cause cracking, melting, or oxidation. |
Material Degradation | Flaking, scaling, and oxidation reduce lifespan and contaminate materials. |
Capacity Constraints | Limited production scale hinders large-scale operations. |
Energy Inefficiency | Heat loss and high energy costs reduce efficiency. |
High Costs | Expensive materials like alumina and graphite increase operational expenses. |
Frequent Replacement | Wear and tear from high temperatures necessitate regular maintenance. |
Oxidation and Rusting | Graphite crucibles oxidize at low temperatures, requiring careful handling. |
Need help selecting the right crucible for your application? Contact our experts today for tailored solutions!