Direct core type induction furnaces, while efficient for certain applications, have several disadvantages that can impact their performance and suitability for specific industrial needs. These drawbacks include issues related to uneven heating, energy consumption, and the need for additional fixtures, which can complicate the process and increase costs. Below, we explore these disadvantages in detail.
Key Points Explained:
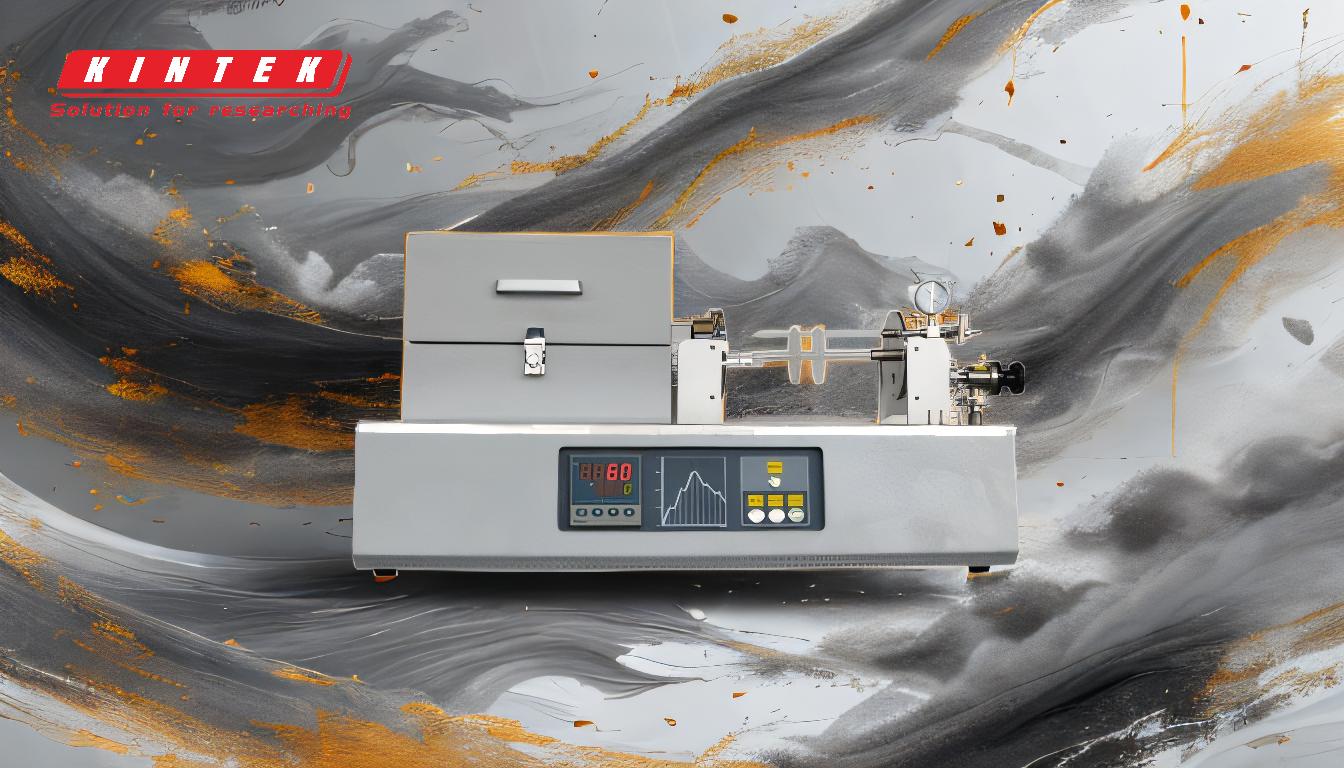
-
Uneven Heating:
- Direct core type induction furnaces often struggle with uneven heating, especially when dealing with large or irregularly shaped loads. The parts closest to the heat source will heat faster, leading to temperature inconsistencies across the load. This can result in uneven material properties, such as hardness or microstructure, which can be detrimental in applications requiring precise thermal treatment.
-
Increased Energy Consumption:
- The need to heat not only the parts but also the fixtures (like baskets or racks) used to hold them increases the overall heat load. This additional energy requirement can significantly raise operational costs, making the process less energy-efficient compared to other furnace types that might not require such fixtures.
-
Work in Process (WIP) Complexity:
- Batch furnaces, including direct core type induction furnaces, require more work in process to form groups for loading. This involves organizing parts into batches, which can be time-consuming and labor-intensive. The need for fixtures to group parts together adds another layer of complexity, requiring additional handling and preparation before the heating process can begin.
-
Fixtures and Their Impact:
- The use of carts, baskets, or racks to group parts together is necessary in batch furnaces, but these fixtures must also be heated along with the parts. This not only increases the energy consumption but also adds to the wear and tear of the fixtures, leading to higher maintenance costs and potential downtime for repairs or replacements.
-
Limited Flexibility:
- Direct core type induction furnaces are generally less flexible when it comes to handling different types of materials or varying load sizes. The need for specific fixtures and the potential for uneven heating can limit the furnace's ability to adapt to different production requirements, making it less versatile compared to other furnace types.
-
Operational Challenges:
- The process of loading and unloading parts, along with the need to manage and maintain fixtures, can introduce operational challenges. These include longer cycle times, increased labor requirements, and the potential for errors or inconsistencies in the heating process, all of which can impact overall productivity and efficiency.
In summary, while direct core type induction furnaces offer certain advantages, such as rapid heating and precise temperature control, their disadvantages—such as uneven heating, increased energy consumption, and the complexity of managing fixtures—can make them less suitable for some industrial applications. Understanding these drawbacks is crucial for making informed decisions about furnace selection and ensuring optimal performance in specific manufacturing processes.
Summary Table:
Disadvantage | Impact |
---|---|
Uneven Heating | Leads to inconsistent material properties and poor thermal treatment. |
Increased Energy Consumption | Higher operational costs due to heating fixtures and parts. |
Work in Process Complexity | Time-consuming batch preparation and labor-intensive handling. |
Fixtures and Their Impact | Increases energy use, maintenance costs, and potential downtime. |
Limited Flexibility | Less adaptable to varying materials or load sizes. |
Operational Challenges | Longer cycle times, higher labor needs, and potential errors. |
Struggling with furnace inefficiencies? Let our experts help you find the right solution—contact us today!