The hardening process, while essential for improving the mechanical properties of materials, has several disadvantages that can impact the quality, cost, and usability of the final product. These disadvantages include the need for skilled operators, potential material loss, and challenges related to surface quality and post-processing. Understanding these drawbacks is crucial for equipment and consumable purchasers to make informed decisions and optimize their processes.
Key Points Explained:
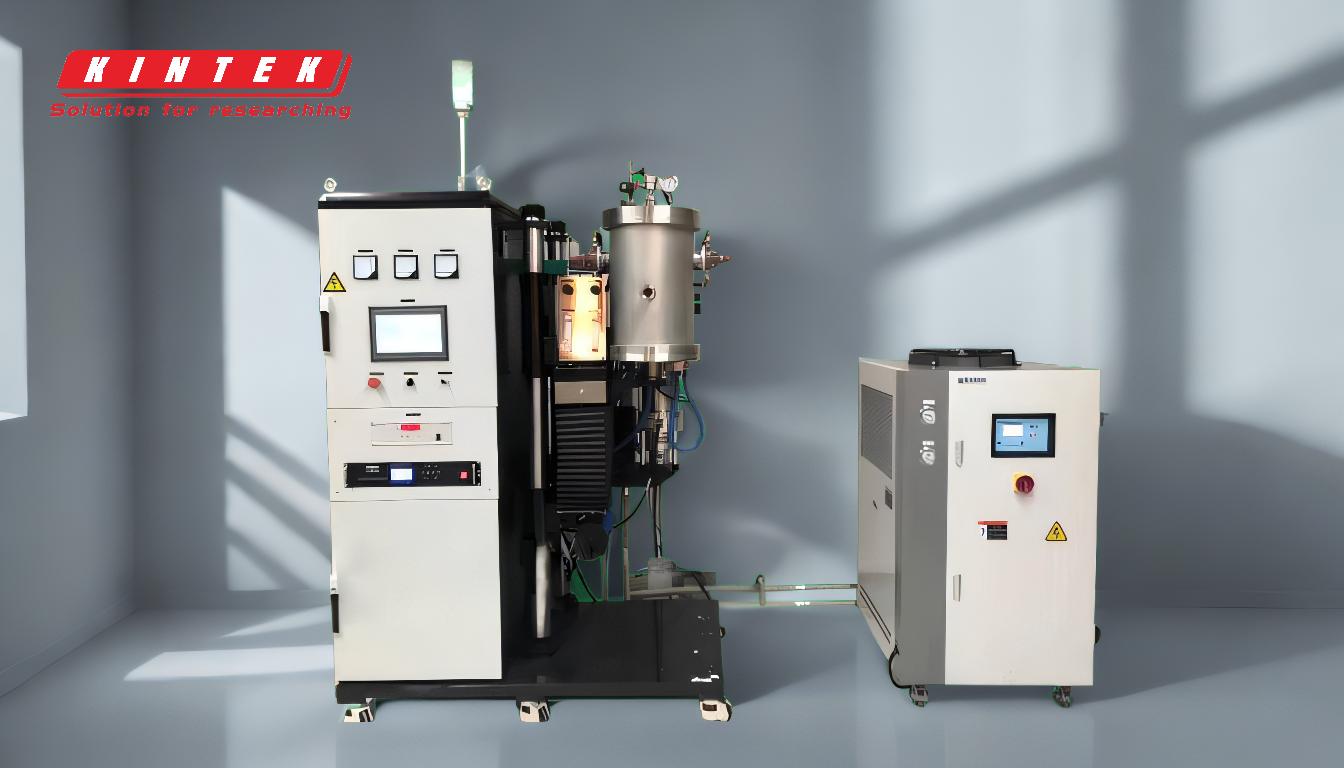
-
High Skill Requirement for Operators:
- The hardening process, particularly in methods like hot pressing, demands a high level of operator skill. This is because the combination of temperature, pressure, heating, and cooling rates must be precisely controlled to achieve the desired material properties.
- Skilled operators are needed to monitor and adjust these parameters in real-time, ensuring that the material does not overheat, cool too quickly, or experience uneven pressure distribution. This level of control is critical to avoid defects such as warping, cracking, or inconsistent hardness.
- For purchasers, this means investing in training programs or hiring experienced personnel, which can increase operational costs.
-
Material Loss and Surface Issues:
- One significant disadvantage of the hardening process is the potential loss of material, such as cobalt, which can be extruded from the product surface during hot pressing. This not only leads to material waste but also affects the surface quality of the final product.
- The extruded material can cause the surface to become rough, making it difficult to clean and process further. This roughness may require additional finishing steps, such as grinding or polishing, to achieve the desired surface smoothness.
- For purchasers, this translates to higher material costs and additional processing steps, which can increase production time and expenses.
-
Challenges in Post-Processing:
- The hardening process can make the material more difficult to machine or shape after treatment. For instance, hardened materials are often harder and more brittle, making them prone to cracking or chipping during machining.
- This brittleness can also limit the types of post-processing techniques that can be applied, as some methods may not be suitable for hardened materials. For example, certain welding or bending processes may not be feasible without risking damage to the material.
- Purchasers need to consider these limitations when planning their production processes, as they may need to invest in specialized equipment or techniques to handle hardened materials effectively.
-
Energy and Equipment Costs:
- The hardening process typically requires significant energy input, especially in methods like hot pressing or heat treatment. High temperatures and prolonged heating cycles can lead to increased energy consumption, which can be costly.
- Additionally, the equipment used for hardening, such as furnaces or presses, can be expensive to purchase and maintain. These machines often require regular maintenance to ensure consistent performance and avoid downtime.
- For purchasers, this means higher capital expenditure and ongoing operational costs, which need to be factored into the overall budget.
-
Potential for Residual Stresses:
- During the hardening process, residual stresses can develop within the material due to uneven cooling or rapid temperature changes. These stresses can lead to dimensional instability, warping, or even cracking over time.
- Residual stresses can also affect the mechanical properties of the material, such as its fatigue resistance or load-bearing capacity. This can be particularly problematic in applications where the material is subjected to cyclic loading or high stress.
- Purchasers must consider the potential impact of residual stresses on the performance and longevity of their products, and may need to implement stress-relief treatments or other corrective measures.
-
Limited Material Compatibility:
- Not all materials are suitable for the hardening process. Some materials may not respond well to heat treatment or may require specific conditions that are difficult to achieve consistently.
- For example, certain alloys or composite materials may have limited hardening capabilities, which can restrict their use in applications requiring high strength or durability.
- Purchasers need to carefully evaluate the compatibility of their chosen materials with the hardening process, and consider alternative treatments or materials if necessary.
In summary, while the hardening process offers significant benefits in terms of material strength and durability, it also presents several challenges that need to be carefully managed. These include the need for skilled operators, potential material loss, surface quality issues, post-processing difficulties, high energy and equipment costs, residual stresses, and limited material compatibility. By understanding these disadvantages, equipment and consumable purchasers can make more informed decisions and optimize their processes to achieve the best possible outcomes.
Summary Table:
Disadvantage | Impact |
---|---|
High Skill Requirement | Increased operational costs due to the need for skilled operators. |
Material Loss & Surface Issues | Higher material costs and additional processing steps. |
Post-Processing Challenges | Difficulty in machining or shaping hardened materials. |
Energy & Equipment Costs | High energy consumption and expensive equipment maintenance. |
Residual Stresses | Risk of dimensional instability, warping, or cracking. |
Limited Material Compatibility | Restricts use of certain materials or requires alternative treatments. |
Need help optimizing your hardening process? Contact our experts today for tailored solutions!