Temperature plays a critical role in metalworking processes, influencing the mechanical properties, microstructure, and overall performance of metals. It affects processes such as forging, casting, welding, heat treatment, and machining. By controlling temperature, manufacturers can achieve desired material characteristics, such as strength, ductility, hardness, and resistance to wear or corrosion. However, improper temperature management can lead to defects like cracking, warping, or residual stresses. Understanding the effects of temperature is essential for optimizing metalworking operations and ensuring the quality and durability of the final product.
Key Points Explained:
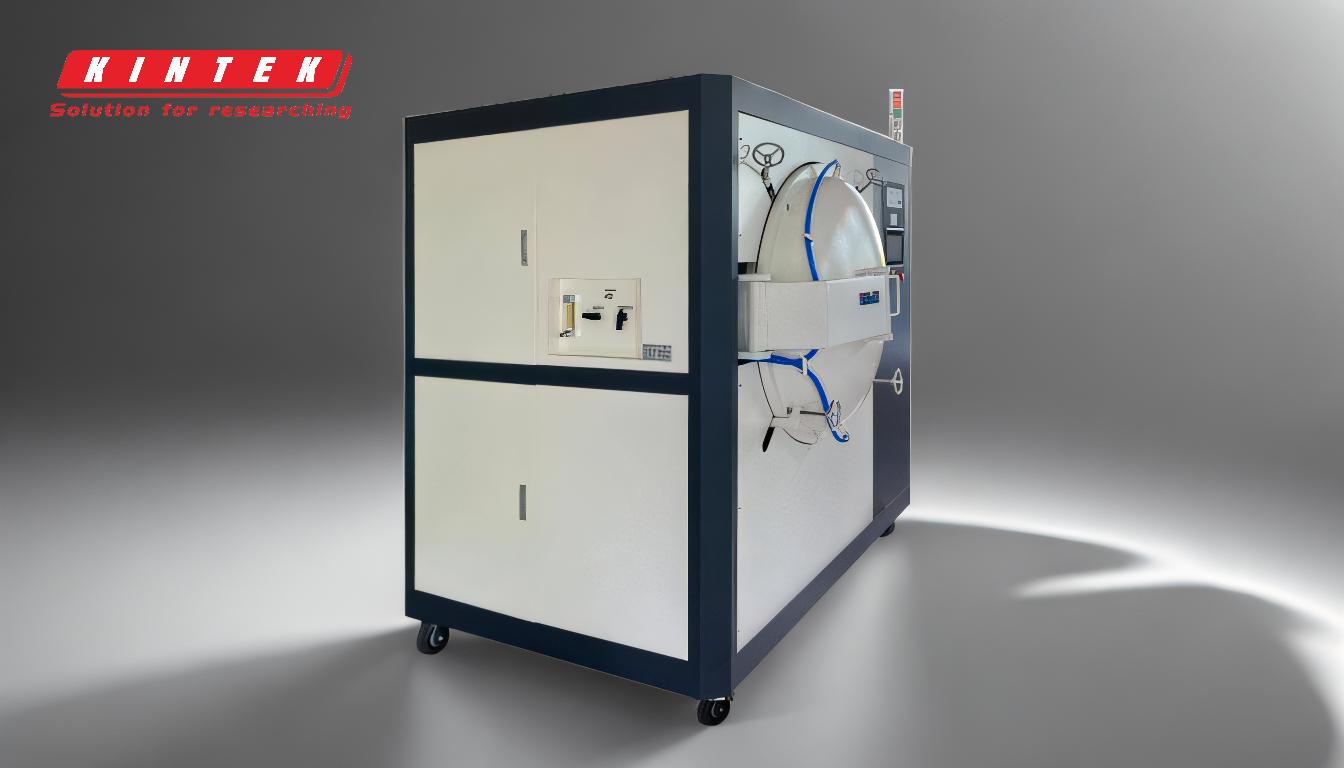
-
Impact on Mechanical Properties:
- Temperature directly affects the mechanical properties of metals, including strength, ductility, and hardness.
- At higher temperatures, metals become more ductile and easier to shape, which is beneficial for processes like forging and rolling.
- Conversely, lower temperatures can increase hardness and strength but may reduce ductility, making the metal more prone to cracking during deformation.
-
Microstructural Changes:
- Temperature influences the microstructure of metals, which in turn affects their performance.
- Heat treatment processes, such as annealing, quenching, and tempering, rely on controlled temperature changes to alter grain size, phase composition, and dislocation density.
- For example, rapid cooling (quenching) can create a hard but brittle martensitic structure, while slow cooling (annealing) promotes softer, more ductile microstructures.
-
Thermal Expansion and Contraction:
- Metals expand when heated and contract when cooled, which can lead to dimensional changes and residual stresses.
- In welding, uneven heating and cooling can cause warping or cracking if not properly managed.
- Preheating and post-weld heat treatment are often used to minimize these effects and ensure dimensional stability.
-
Workability and Formability:
- Temperature affects the ease with which metals can be worked or formed.
- Hot working (above recrystallization temperature) reduces the force required for deformation and allows for greater shape changes without cracking.
- Cold working (below recrystallization temperature) increases strength and hardness but limits the extent of deformation due to reduced ductility.
-
Thermal Fatigue and Creep:
- Repeated heating and cooling cycles can lead to thermal fatigue, causing cracks and failure over time.
- At high temperatures, metals may experience creep, a slow deformation under constant stress, which can compromise structural integrity.
- These effects are particularly important in applications like turbine blades or engine components, where metals are exposed to cyclic thermal loads.
-
Oxidation and Scaling:
- High temperatures can cause metals to react with oxygen, leading to oxidation and the formation of scales on the surface.
- This can result in material loss and surface defects, which may require additional finishing processes.
- Protective atmospheres or coatings are often used to minimize oxidation during high-temperature operations.
-
Energy Efficiency and Process Optimization:
- Controlling temperature is crucial for energy efficiency in metalworking processes.
- Excessive heating can waste energy and increase costs, while insufficient heating may lead to poor-quality products.
- Advanced temperature control systems and monitoring techniques help optimize processes and reduce energy consumption.
-
Defects and Quality Control:
- Improper temperature control can lead to defects such as cracks, voids, or uneven microstructures.
- Non-destructive testing methods, such as ultrasonic or thermal imaging, are used to detect temperature-related defects and ensure product quality.
- Process parameters must be carefully monitored and adjusted to maintain consistent temperatures and avoid defects.
By understanding and managing the effects of temperature in metalworking processes, manufacturers can achieve superior product quality, improve efficiency, and extend the lifespan of metal components. Temperature control is a fundamental aspect of modern metalworking, enabling the production of high-performance materials for a wide range of applications.
Summary Table:
Aspect | Impact of Temperature |
---|---|
Mechanical Properties | Affects strength, ductility, and hardness; higher temps increase ductility, lower temps increase hardness. |
Microstructural Changes | Alters grain size, phase composition, and dislocation density through heat treatment. |
Thermal Expansion | Causes dimensional changes and residual stresses; managed via preheating and post-weld treatments. |
Workability | Hot working reduces deformation force; cold working increases strength but limits ductility. |
Thermal Fatigue & Creep | Repeated cycles cause cracks; high temps lead to creep, affecting structural integrity. |
Oxidation & Scaling | High temps cause oxidation, leading to material loss and surface defects. |
Energy Efficiency | Proper temperature control optimizes energy use and reduces costs. |
Defects & Quality Control | Improper temps cause cracks, voids, or uneven microstructures; testing ensures quality. |
Want to optimize your metalworking processes with precise temperature control? Contact our experts today for tailored solutions!