Heat treatment is a critical process in metallurgy and materials science, involving the controlled heating and cooling of metals and alloys to alter their physical and mechanical properties. The equipment used for heat treatment varies depending on the specific requirements of the process, such as temperature range, cooling rate, and the type of material being treated. Common equipment includes furnaces, quenching systems, and tempering ovens, each designed to achieve precise thermal conditions. The goal is to achieve desired microstructural changes, such as hardness, ductility, or toughness, by carefully controlling the heating and cooling cycles.
Key Points Explained:
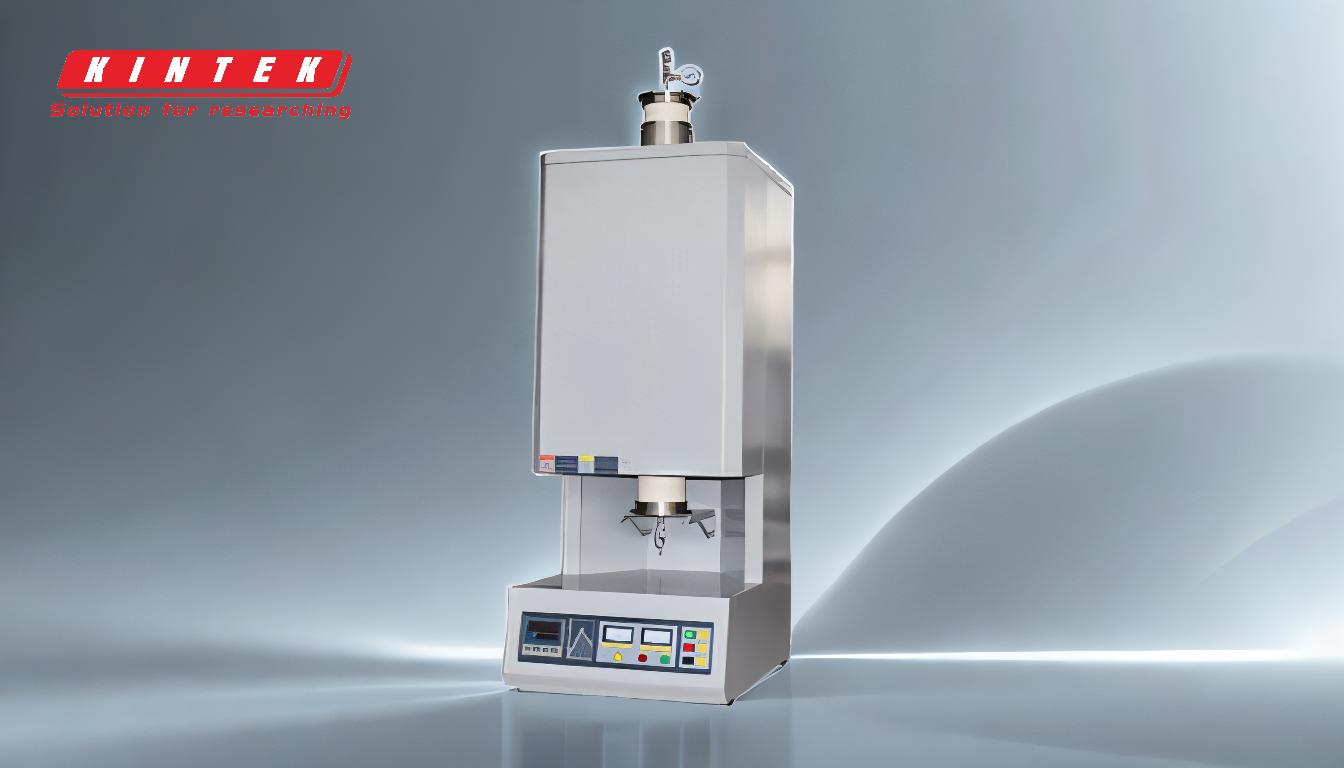
-
Heat Treatment Process Overview:
- Heat treatment involves heating metals or alloys to specific temperatures and holding them there for a set period, followed by controlled cooling.
- The process aims to achieve desired properties like improved hardness, strength, or ductility.
- For example, heating an alloy to a suitable temperature allows a desired constituent to enter into a solid solution, which is then rapidly cooled to maintain the supersaturated state.
-
Common Equipment for Heat Treatment:
-
Furnaces: These are the primary equipment used for heating metals. They come in various types, such as:
- Muffle Furnaces: These are commonly used for heat treatment due to their ability to provide uniform heating and precise temperature control. They are particularly useful for processes like annealing, hardening, and tempering.
- Box Furnaces: Suitable for batch processing, these furnaces are used for processes like annealing, normalizing, and stress relieving.
- Vacuum Furnaces: Used for heat treatment in a vacuum or inert atmosphere to prevent oxidation and contamination.
- Quenching Systems: After heating, metals are often rapidly cooled (quenched) to achieve the desired properties. Quenching can be done using water, oil, or air, depending on the material and the required cooling rate.
- Tempering Ovens: These are used to reduce the brittleness of metals after quenching by reheating them to a lower temperature and then cooling them slowly.
-
Furnaces: These are the primary equipment used for heating metals. They come in various types, such as:
-
Specific Applications of Heat Treatment Equipment:
- Annealing: This process involves heating the metal to a specific temperature and then slowly cooling it to soften the material and improve its machinability.
- Hardening: Metals are heated to a high temperature and then rapidly cooled to increase their hardness and strength.
- Tempering: After hardening, metals are reheated to a lower temperature to reduce brittleness and improve toughness.
- Normalizing: Similar to annealing, but the cooling process is done in air, resulting in a more uniform microstructure.
-
Importance of Temperature Control:
- Precise temperature control is crucial in heat treatment to ensure that the desired microstructural changes occur.
- Furnaces used for heat treatment are equipped with advanced temperature control systems, including thermocouples and digital controllers, to maintain the required temperature within tight tolerances.
-
Cooling Methods:
- The cooling rate after heating is a critical factor in determining the final properties of the metal.
- Different cooling methods, such as water quenching, oil quenching, or air cooling, are used depending on the material and the desired outcome.
-
Safety and Environmental Considerations:
- Heat treatment processes often involve high temperatures and potentially hazardous materials, so safety measures, such as proper ventilation and protective equipment, are essential.
- Environmental considerations, such as energy efficiency and emissions control, are also important when selecting heat treatment equipment.
In summary, the equipment used for heat treatment, such as furnaces, quenching systems, and tempering ovens, plays a crucial role in achieving the desired properties in metals and alloys. Each piece of equipment is designed to provide precise control over the heating and cooling processes, ensuring that the material undergoes the necessary microstructural changes to meet specific performance requirements.
Summary Table:
Equipment | Key Features | Applications |
---|---|---|
Muffle Furnaces | Uniform heating, precise temperature control | Annealing, hardening, tempering |
Box Furnaces | Batch processing, versatile | Annealing, normalizing, stress relieving |
Vacuum Furnaces | Prevents oxidation, inert atmosphere | High-precision heat treatment |
Quenching Systems | Rapid cooling (water, oil, or air) | Hardening, achieving desired material properties |
Tempering Ovens | Reduces brittleness, improves toughness | Post-quenching tempering |
Need the right heat treatment equipment for your lab? Contact us today to find the perfect solution!