The porosity of ceramic ware is influenced by several factors, including the initial porosity of the green compact, the sintering temperature, the duration of the sintering process, and the application of pressure during sintering. Pure oxide ceramics, in particular, require higher temperatures and longer sintering times due to solid-state particle diffusion. Understanding these factors is crucial for controlling the final porosity of ceramic products, which directly impacts their mechanical, thermal, and electrical properties.
Key Points Explained:
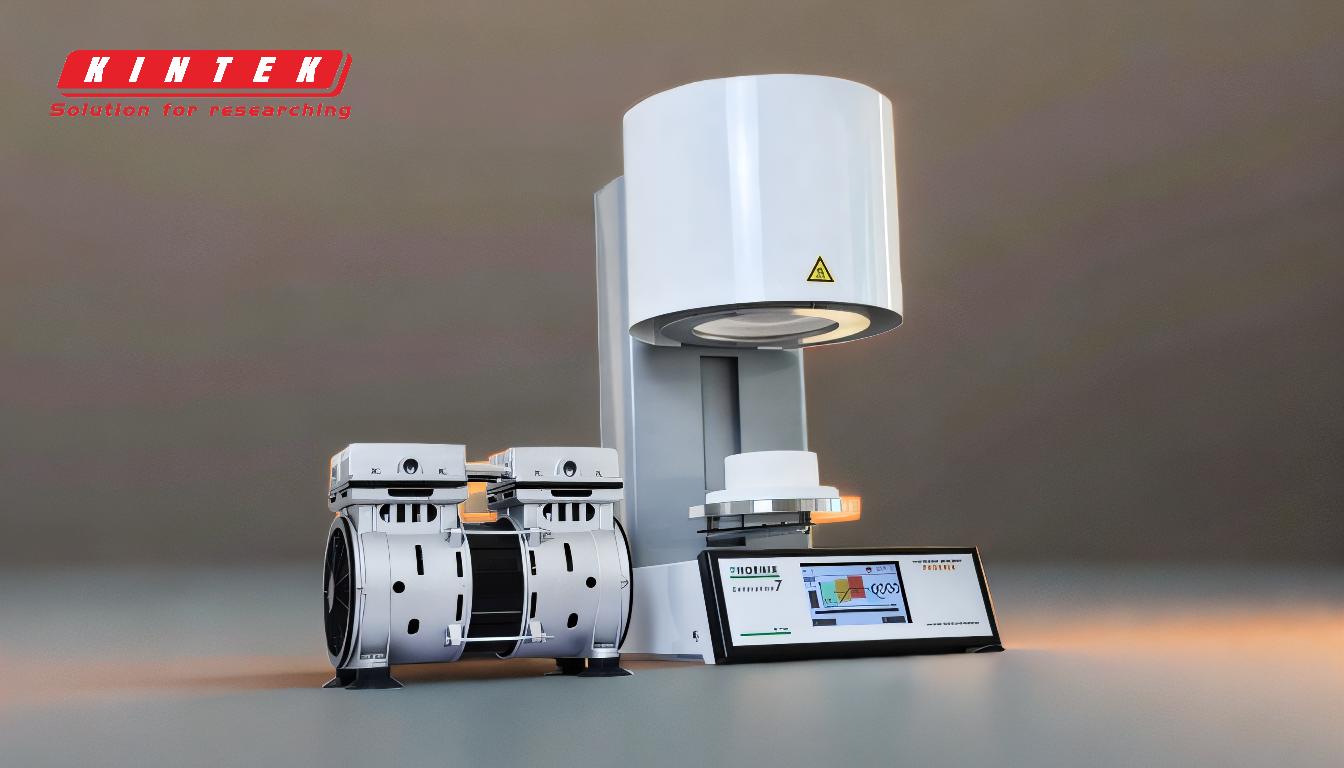
-
Initial Porosity of the Green Compact:
- The green compact refers to the ceramic material before it undergoes sintering. The initial porosity of this compact plays a significant role in determining the final porosity of the sintered ceramic.
- Higher initial porosity generally leads to higher final porosity unless the sintering process effectively reduces it.
- The density and uniformity of the green compact are critical. A more densely packed green compact with fewer voids will result in lower final porosity after sintering.
-
Sintering Temperature:
- Sintering temperature is a critical factor in reducing porosity. Higher temperatures facilitate the diffusion of particles, leading to denser ceramic structures.
- For pure oxide ceramics, higher sintering temperatures are necessary because particle diffusion occurs in the solid state, which is slower compared to liquid-phase sintering.
- However, excessively high temperatures can lead to undesirable effects such as grain growth, which might negatively impact the mechanical properties of the ceramic.
-
Duration of the Sintering Process:
- The time duration of the sintering process also affects the final porosity. Longer sintering times allow for more complete particle diffusion and densification.
- In the case of pure oxide ceramics, longer sintering times are required to achieve the desired reduction in porosity due to the slower solid-state diffusion.
- Balancing the sintering time with temperature is essential to achieve optimal porosity without causing excessive grain growth or other defects.
-
Application of Pressure:
- Applying pressure during the sintering process can significantly reduce both the sintering time and the final porosity. This technique is known as pressure-assisted sintering or hot pressing.
- Pressure helps in closing the pores and enhancing particle rearrangement, leading to a denser ceramic structure.
- This method is particularly useful for materials that are difficult to sinter under normal conditions, such as certain pure oxide ceramics.
-
Material Composition:
- The type of ceramic material also influences porosity. Pure oxide ceramics, for example, have different sintering behaviors compared to composite ceramics.
- Additives or dopants can be used to modify the sintering behavior and reduce porosity. These additives can lower the sintering temperature or enhance diffusion rates.
-
Particle Size and Distribution:
- The size and distribution of the ceramic particles in the green compact affect the sintering process and final porosity.
- Smaller particles have a higher surface area to volume ratio, which promotes faster sintering and densification.
- A uniform particle size distribution helps in achieving a more homogeneous microstructure with controlled porosity.
By carefully controlling these factors, manufacturers can tailor the porosity of ceramic ware to meet specific application requirements, whether for structural components, thermal insulators, or electronic substrates.
Summary Table:
Factor | Impact on Porosity |
---|---|
Initial Porosity of Green Compact | Higher initial porosity leads to higher final porosity unless sintering reduces it. |
Sintering Temperature | Higher temperatures reduce porosity but excessive heat can cause grain growth. |
Sintering Duration | Longer sintering times reduce porosity, especially for pure oxide ceramics. |
Application of Pressure | Pressure-assisted sintering reduces porosity and sintering time. |
Material Composition | Pure oxide ceramics require higher temperatures and longer sintering times. |
Particle Size and Distribution | Smaller, uniform particles promote faster sintering and controlled porosity. |
Need help optimizing ceramic porosity for your project? Contact our experts today!