The rate of the melting process is influenced by several factors, including the material's properties, the heat source's characteristics, and environmental conditions. Key factors include the material's melting point, thermal conductivity, and specific heat capacity, which determine how efficiently heat is transferred and absorbed. The heat source's temperature, intensity, and distribution also play a critical role, as higher temperatures and uniform heating accelerate melting. Additionally, external factors like ambient temperature, pressure, and the presence of impurities can either speed up or slow down the process. Understanding these factors is essential for optimizing melting processes in industrial and laboratory settings.
Key Points Explained:
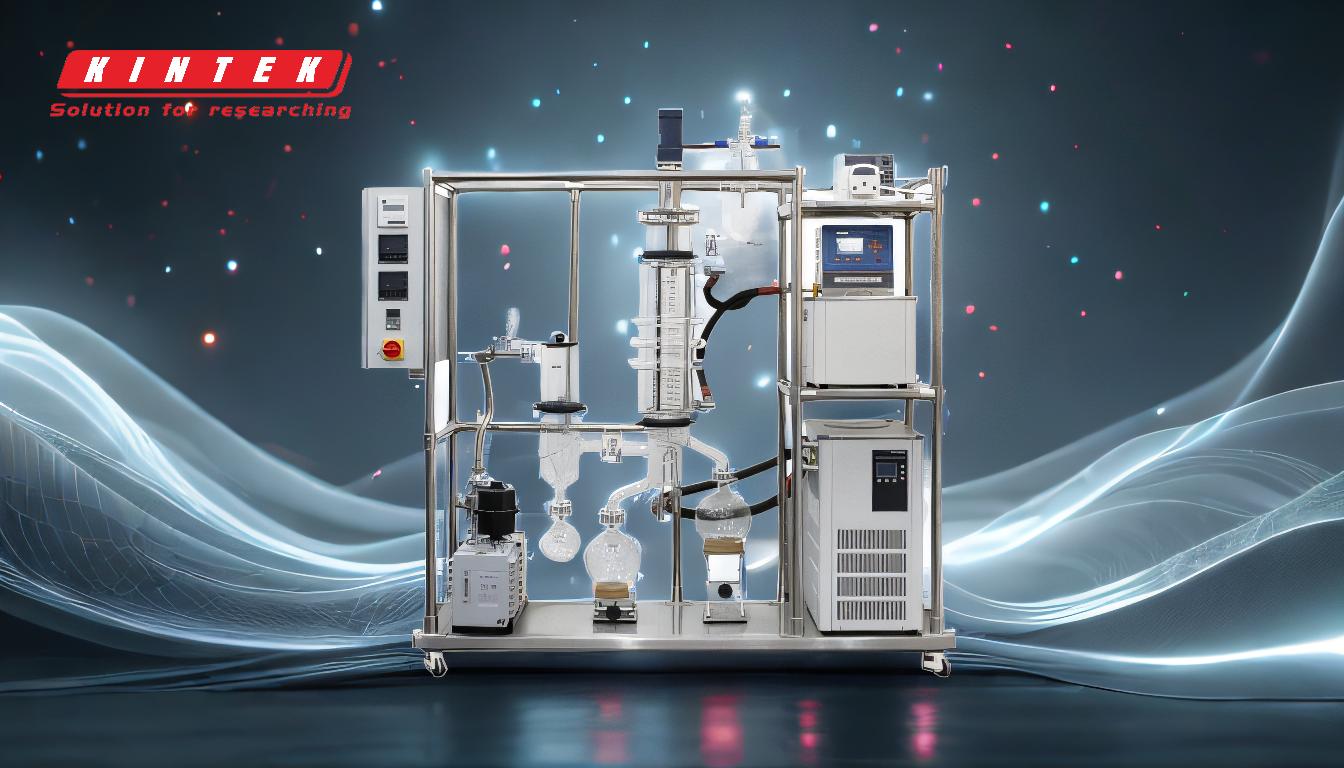
-
Material Properties:
- Melting Point: The temperature at which a material transitions from solid to liquid. Materials with lower melting points generally melt faster.
- Thermal Conductivity: Determines how efficiently heat is transferred through the material. Higher thermal conductivity allows heat to spread more quickly, speeding up the melting process.
- Specific Heat Capacity: The amount of heat required to raise the temperature of a unit mass of the material by one degree. Materials with lower specific heat capacities require less energy to melt, leading to faster melting rates.
-
Heat Source Characteristics:
- Temperature: Higher temperatures provide more energy to the material, accelerating the melting process. However, excessively high temperatures can lead to material degradation or evaporation.
- Intensity and Distribution: The uniformity and intensity of the heat source affect how evenly and quickly the material melts. A concentrated heat source may cause localized melting, while a distributed heat source ensures uniform melting.
-
Environmental Conditions:
- Ambient Temperature: The surrounding temperature can influence the rate of melting. Higher ambient temperatures reduce the energy required to reach the melting point.
- Pressure: Changes in pressure can alter the melting point of materials. For example, increased pressure generally raises the melting point, slowing the process.
- Presence of Impurities: Impurities can either lower or raise the melting point, depending on their nature. They can also affect thermal conductivity and heat distribution, impacting the overall melting rate.
-
Phase Transitions and Latent Heat:
- During melting, energy is absorbed as latent heat, which is used to break the bonds between molecules rather than increasing temperature. The amount of latent heat required varies by material and affects the time needed to complete the melting process.
-
Surface Area and Geometry:
- Materials with larger surface areas relative to their volume melt faster because more of the material is exposed to the heat source. The shape and geometry of the material also influence heat absorption and distribution.
-
Heat Transfer Mechanisms:
- Conduction, convection, and radiation are the primary mechanisms of heat transfer. The efficiency of these mechanisms depends on the material and the environment. For example, convection is more effective in liquids, while conduction dominates in solids.
By understanding and controlling these factors, it is possible to optimize the melting process for specific applications, whether in manufacturing, metallurgy, or laboratory research. Adjusting variables like heat source intensity, material composition, and environmental conditions can lead to faster, more efficient melting with minimal energy waste.
Summary Table:
Category | Key Factors |
---|---|
Material Properties | Melting Point, Thermal Conductivity, Specific Heat Capacity |
Heat Source | Temperature, Intensity, Distribution |
Environmental Conditions | Ambient Temperature, Pressure, Presence of Impurities |
Other Influences | Phase Transitions, Surface Area, Geometry, Heat Transfer Mechanisms |
Need help optimizing your melting process? Contact our experts today for tailored solutions!