Thin film manufacturing involves a variety of methods, broadly categorized into physical and chemical deposition processes. Physical deposition techniques include vacuum evaporation, laser ablation, molecular beam epitaxy (MBE), and sputtering. Chemical deposition methods encompass chemical vapor deposition (CVD), atomic layer epitaxy, spray pyrolysis, sol-gel, spin-coating, and dip-coating. These methods are chosen based on the desired film properties, substrate material, and application requirements. The deposition process typically involves several phases: adsorption, surface diffusion, and nucleation, which are influenced by the material and substrate properties. Common techniques like PVD and CVD are widely used in industries for producing thin films with precise control over thickness and properties.
Key Points Explained:
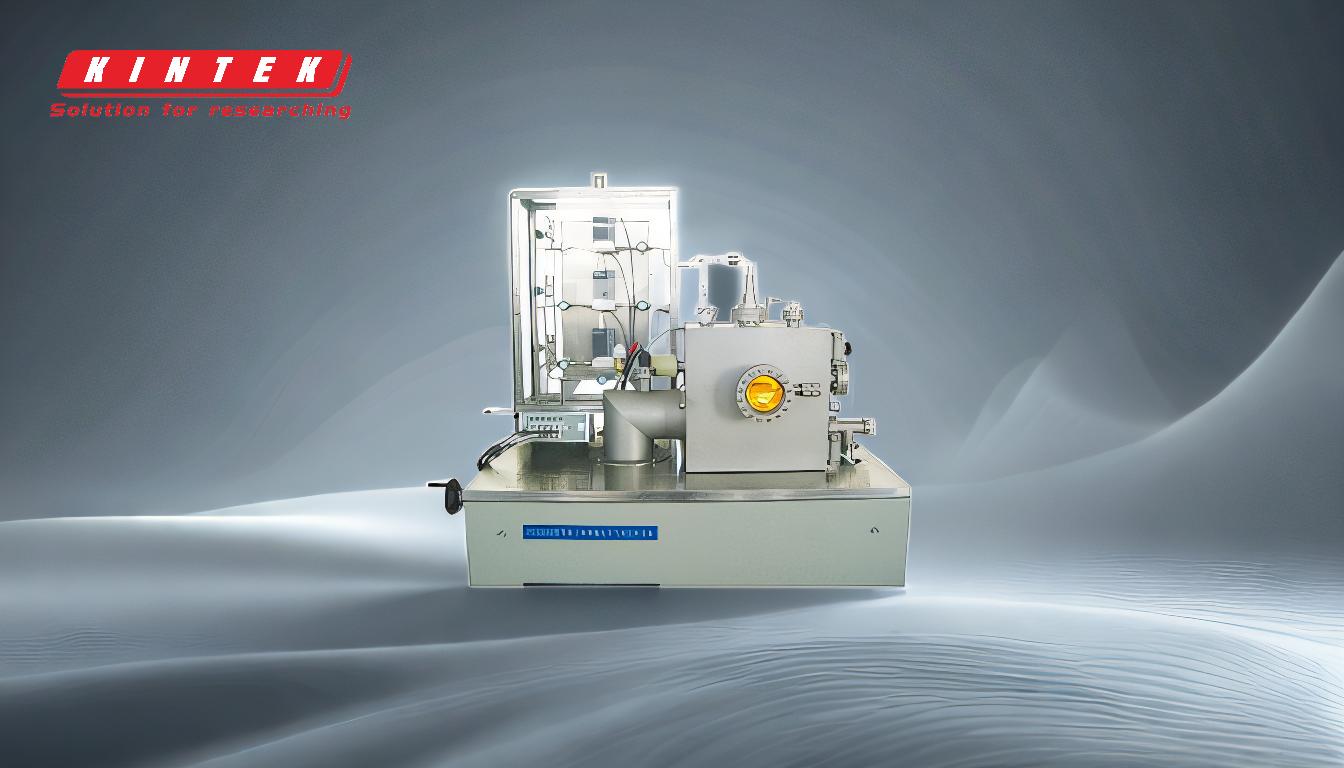
-
Physical Deposition Methods:
- Vacuum Evaporation: A technique where the material is heated in a vacuum until it evaporates and then condenses on a substrate to form a thin film. This method is suitable for materials with high vapor pressure.
- Laser Ablation: Involves using a high-power laser to vaporize material from a target, which then deposits onto a substrate. This method is useful for complex materials and multi-layer structures.
- Molecular Beam Epitaxy (MBE): A highly controlled process where beams of atoms or molecules are directed onto a substrate to grow thin films layer by layer. MBE is ideal for producing high-quality crystalline films.
- Sputtering: A process where atoms are ejected from a solid target material due to bombardment by energetic ions, and these atoms then deposit onto a substrate. Sputtering is versatile and can be used for a wide range of materials.
-
Chemical Deposition Methods:
- Chemical Vapor Deposition (CVD): Involves the reaction of gaseous precursors on a substrate surface to form a solid thin film. CVD is widely used for depositing high-quality, uniform films and is suitable for a variety of materials.
- Atomic Layer Epitaxy (ALE): A variant of CVD where thin films are deposited one atomic layer at a time, allowing for precise control over film thickness and composition.
- Spray Pyrolysis: A technique where a solution containing the desired material is sprayed onto a heated substrate, causing the solvent to evaporate and the material to decompose, forming a thin film.
- Sol-Gel: Involves the transition of a solution (sol) into a gel-like state, which is then dried and heat-treated to form a thin film. This method is useful for producing oxide films and coatings.
- Spin-Coating: A process where a liquid precursor is applied to a substrate, which is then spun at high speed to spread the liquid into a thin, uniform layer. Spin-coating is commonly used in the semiconductor industry.
- Dip-Coating: Involves immersing a substrate into a liquid precursor and then withdrawing it at a controlled speed to form a thin film. This method is simple and cost-effective for large-area coatings.
-
Deposition Process Phases:
- Adsorption: The initial phase where atoms or molecules from the deposition source adhere to the substrate surface.
- Surface Diffusion: The movement of adsorbed atoms or molecules across the substrate surface, which influences the film's uniformity and structure.
- Nucleation: The formation of small clusters or nuclei on the substrate surface, which grow and coalesce to form a continuous thin film.
-
Common Techniques:
- Physical Vapor Deposition (PVD): Encompasses methods like vacuum evaporation, sputtering, and MBE. PVD is widely used for depositing metals, alloys, and ceramics.
- Chemical Vapor Deposition (CVD): Includes techniques like CVD, ALE, and spray pyrolysis. CVD is preferred for depositing high-quality, uniform films of semiconductors, oxides, and other materials.
-
Applications:
- Semiconductors: Thin films are crucial in the production of semiconductor devices, where precise control over film thickness and properties is essential.
- Flexible Electronics: Techniques like spin-coating and dip-coating are used to produce thin films for flexible solar cells and organic light-emitting diodes (OLEDs).
- Optical Coatings: Thin films are used in anti-reflective coatings, mirrors, and filters, where precise control over optical properties is required.
-
Process Control and Optimization:
- Material Selection: Choosing the right target material and precursor is crucial for achieving the desired film properties.
- Deposition Parameters: Factors like temperature, pressure, and deposition rate must be carefully controlled to ensure uniform and high-quality films.
- Post-Deposition Treatments: Annealing or heat treatment can improve the film's properties, such as crystallinity and adhesion.
In summary, thin film manufacturing encompasses a wide range of physical and chemical deposition methods, each with its own advantages and applications. The choice of method depends on the specific requirements of the film and the substrate, with processes like PVD and CVD being widely used in various industries. Understanding the deposition phases and optimizing the process parameters are essential for producing high-quality thin films with the desired properties.
Summary Table:
Category | Methods | Applications |
---|---|---|
Physical Deposition | Vacuum Evaporation, Laser Ablation, MBE, Sputtering | Metals, Alloys, Ceramics, Multi-layer Structures |
Chemical Deposition | CVD, Atomic Layer Epitaxy, Spray Pyrolysis, Sol-Gel, Spin-Coating, Dip-Coating | Semiconductors, Flexible Electronics, Optical Coatings |
Deposition Phases | Adsorption, Surface Diffusion, Nucleation | Influences film uniformity, structure, and quality |
Common Techniques | PVD (Physical Vapor Deposition), CVD (Chemical Vapor Deposition) | Widely used in industries for high-quality, uniform thin films |
Discover the best thin film manufacturing method for your needs—contact our experts today!