A press forming machine, particularly a hot press machine, is a complex piece of equipment designed for shaping materials under heat and pressure. It consists of several key components that work together to ensure efficient and precise operation. These components include the base, hydraulic cylinders, columns, frames, platens, and various systems for heating, cooling, and control. Understanding each part's function is crucial for selecting the right machine for specific industrial applications.
Key Points Explained:
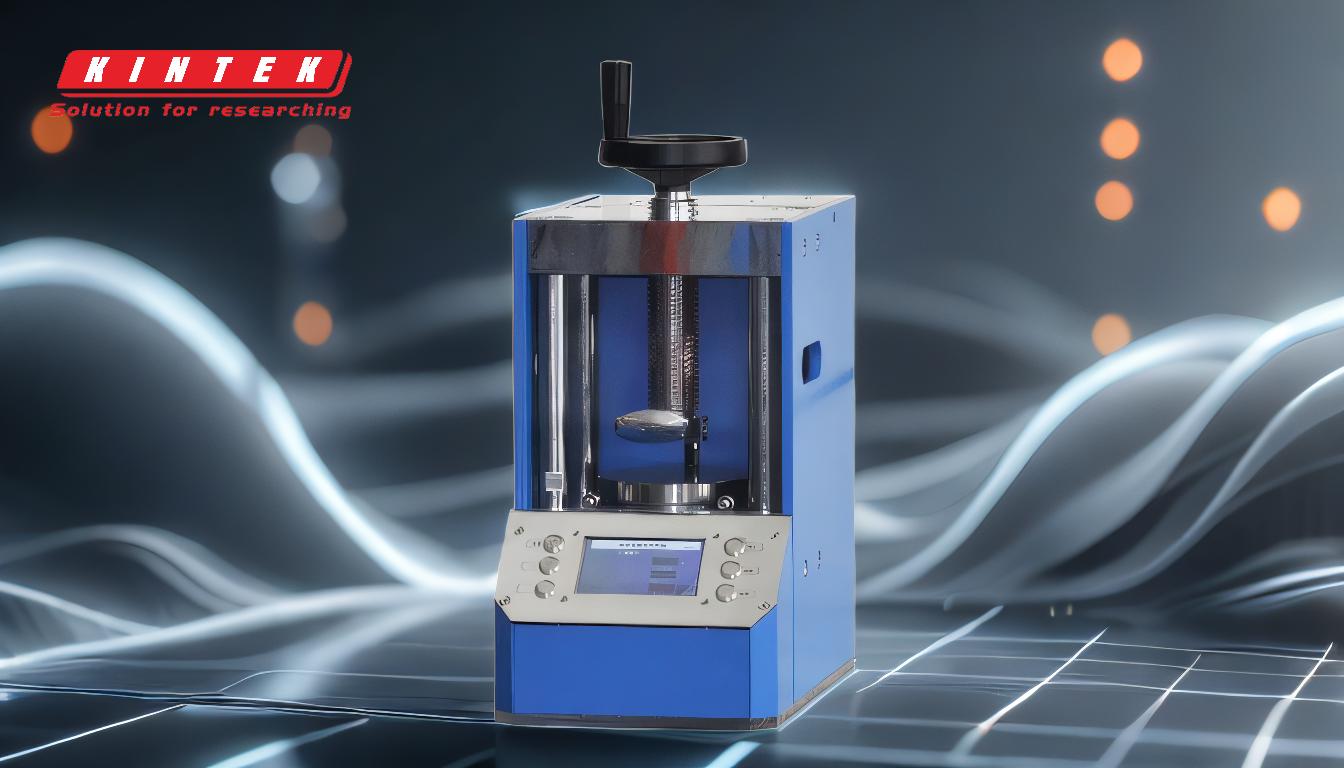
-
Base and Hydraulic Cylinders:
- The base of the hot press machine houses one or several hydraulic cylinders. These cylinders are responsible for the up and down movement necessary for the pressing action. The hydraulic system provides the force needed to compress and shape materials, making it a critical component of the machine.
-
Columns, Frames, and Steel Sheets:
- The head of the press is connected to the base by columns and frames, which provide structural support. Solid steel sheets are used to reinforce the structure, ensuring stability and durability during operation. These components are essential for maintaining the integrity of the machine under high pressure and temperature.
-
Platens:
- Platens are thick steel plates, usually 40 to 50 mm thick, with holes drilled for the passage of hot oil or steam. These platens are cast in one piece, ground, and chromium-plated to prevent glue from sticking and to improve surface finish and prevent corrosion. The platens play a crucial role in distributing heat and pressure evenly across the material being processed.
-
Heating and Temperature Control System:
- The heating system, often integrated with the platens, ensures that the material is heated to the required temperature for forming. The temperature measurement system monitors and controls the heat, ensuring consistent and precise processing conditions. This system is vital for achieving the desired material properties and quality.
-
Vacuum and Air Charging Systems:
- In some hot press machines, a vacuum system is used to remove air from the pressing chamber, preventing oxidation and ensuring a clean environment for the material. The air charging system can introduce inert gases to further protect the material during processing. These systems are particularly important in applications requiring high purity and precision.
-
Water Cooling System:
- The water cooling system helps regulate the temperature of the machine, preventing overheating and ensuring safe operation. It is especially important in maintaining the longevity of the machine components and ensuring consistent performance.
-
Control System:
- The control system manages the operation of the hot press machine, including the hydraulic pressure, temperature, and timing. Advanced control systems can be programmed for specific processes, allowing for automation and repeatability. This system is crucial for achieving precise and consistent results in industrial applications.
-
Pressure System:
- The pressure system, often hydraulic, provides the force needed for the pressing action. It works in conjunction with the control system to apply the correct amount of pressure at the right time, ensuring optimal forming of the material.
Understanding these components and their functions is essential for selecting and operating a hot press machine effectively. Each part plays a vital role in ensuring the machine's performance, durability, and the quality of the final product.
Summary Table:
Component | Function |
---|---|
Base and Hydraulic Cylinders | Provides force for pressing action and supports the machine's structure. |
Columns, Frames, and Steel Sheets | Ensures structural stability and durability under high pressure and heat. |
Platens | Distributes heat and pressure evenly; prevents corrosion and glue sticking. |
Heating and Temperature Control System | Maintains precise temperature for material forming. |
Vacuum and Air Charging Systems | Removes air and introduces inert gases for high-purity applications. |
Water Cooling System | Regulates temperature to prevent overheating and ensure safe operation. |
Control System | Manages hydraulic pressure, temperature, and timing for consistent results. |
Pressure System | Applies the correct force at the right time for optimal material forming. |
Ready to optimize your press forming process? Contact our experts today to find the perfect machine for your needs!