Brazing is a process that involves joining two or more metal pieces using a filler metal with a melting point above 450°C but below the melting point of the base metals. However, certain factors can make brazing a joint impossible or result in a poor-quality joint. These factors include improper material selection, inadequate surface preparation, insufficient heating, poor joint design, and contamination. Understanding these challenges is crucial for achieving a successful brazed joint.
Key Points Explained:
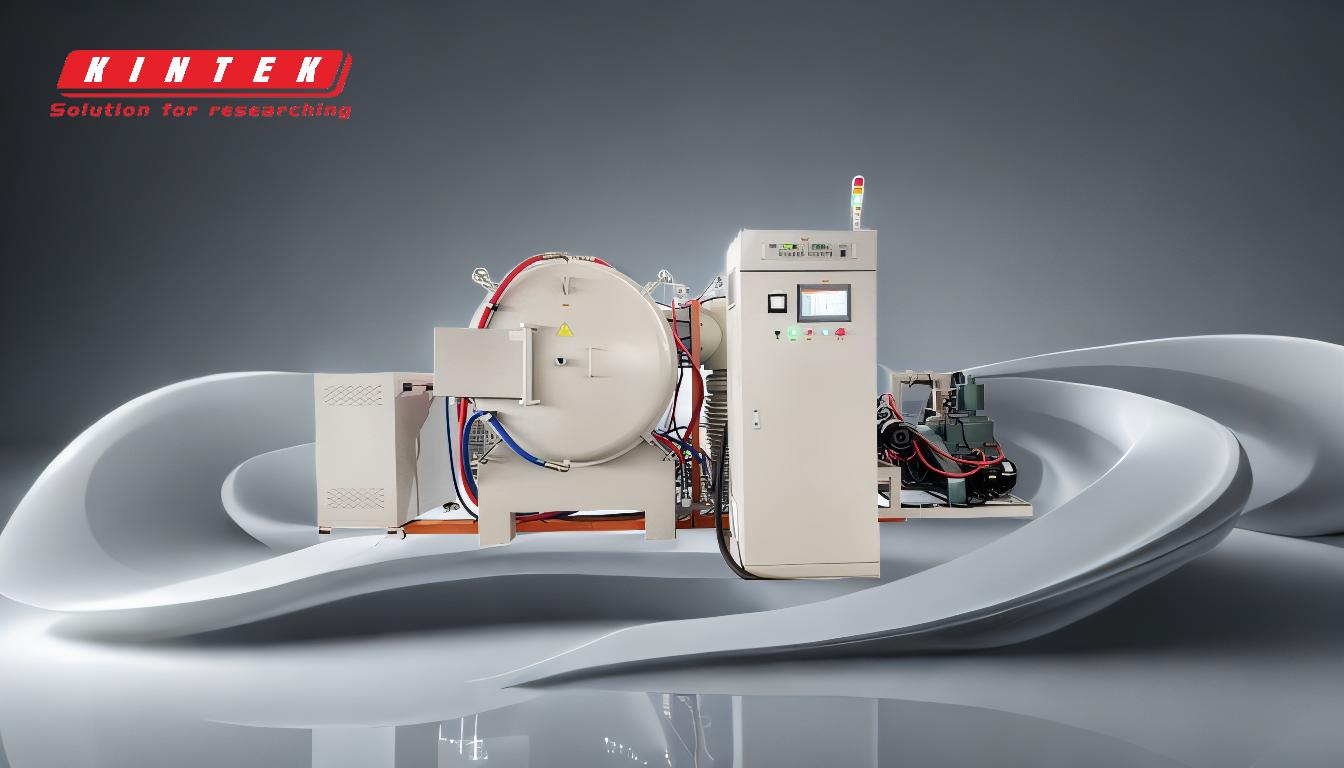
-
Improper Material Selection:
- Mismatched Metals: If the base metals and the filler metal have incompatible properties, such as differing melting points or thermal expansion rates, brazing may fail. For example, attempting to braze aluminum to steel without a suitable filler metal can lead to joint failure.
- Unsuitable Filler Metal: The filler metal must have the right melting point and wetting characteristics to flow properly and bond with the base metals. Using a filler metal that doesn't wet the surfaces or has a melting point too close to the base metals can make brazing impossible.
-
Inadequate Surface Preparation:
- Oxide Layers: Metals often form oxide layers on their surfaces, which can prevent the filler metal from bonding. Proper cleaning and removal of oxides through mechanical or chemical means are essential.
- Contaminants: Oils, grease, or other contaminants on the metal surfaces can interfere with the brazing process. Thorough cleaning is necessary to ensure a strong bond.
-
Insufficient Heating:
- Uneven Heating: If the joint is not heated uniformly, the filler metal may not flow properly, leading to incomplete bonding. This can occur due to improper torch technique or inadequate furnace settings.
- Inadequate Temperature: The brazing temperature must be high enough to melt the filler metal but not so high as to damage the base metals. If the temperature is too low, the filler metal won't flow, and if it's too high, the base metals may warp or melt.
-
Poor Joint Design:
- Inadequate Clearance: The gap between the two metal pieces being brazed must be precise. If the gap is too small, the filler metal may not flow into the joint. If it's too large, the filler metal may not form a strong bond.
- Complex Geometry: Joints with complex shapes or tight corners can be challenging to braze because the filler metal may not flow evenly into all areas.
-
Contamination During Brazing:
- Atmospheric Contamination: Exposure to oxygen or other reactive gases during brazing can lead to oxidation, which prevents the filler metal from bonding. Using a controlled atmosphere or flux can mitigate this issue.
- Flux Residue: While flux is used to remove oxides and improve wetting, excessive or improperly applied flux can leave residues that weaken the joint.
-
Thermal Expansion Mismatch:
- Differential Expansion: If the base metals have significantly different thermal expansion rates, the joint may experience stress during heating and cooling, leading to cracks or failure. This is particularly problematic in dissimilar metal joints.
-
Incorrect Cooling Rate:
- Rapid Cooling: Cooling the joint too quickly can cause thermal stresses, leading to cracks or a weak bond. Controlled cooling is essential to ensure a strong, durable joint.
-
Operator Error:
- Incorrect Technique: Improper handling of the brazing torch, incorrect application of flux, or misalignment of the joint can all contribute to brazing failure. Proper training and adherence to best practices are crucial.
By addressing these factors, it is possible to overcome the challenges that make brazing a joint impossible and achieve a strong, reliable bond. Proper material selection, surface preparation, heating, joint design, and contamination control are all critical to the success of the brazing process.
Summary Table:
Challenge | Description |
---|---|
Improper Material Selection | Mismatched metals or unsuitable filler metal can prevent bonding. |
Inadequate Surface Prep | Oxide layers or contaminants hinder filler metal flow. |
Insufficient Heating | Uneven or incorrect temperatures lead to poor filler metal flow. |
Poor Joint Design | Inadequate clearance or complex geometry affects filler metal distribution. |
Contamination | Atmospheric exposure or flux residue weakens the joint. |
Thermal Expansion Mismatch | Differing expansion rates cause stress and cracks. |
Incorrect Cooling Rate | Rapid cooling creates thermal stresses, weakening the bond. |
Operator Error | Improper technique or misalignment leads to brazing failure. |
Need help achieving a strong brazed joint? Contact our experts today for tailored solutions!