Sintering materials exhibit a range of properties that are influenced by various factors such as temperature, pressure, particle size, and composition. The process aims to reduce porosity and enhance properties like strength, electrical conductivity, translucency, and thermal conductivity. Key variables affecting sintering include the atmosphere, temperature, and cooling rate. High-temperature sintering can improve tensile strength, bending fatigue strength, and impact energy. The binding area associated with particle size is crucial for determining properties such as strength and conductivity. Additionally, the final porosity of sintered ceramics depends on the initial porosity of the green compact, as well as the temperature and duration of the sintering process. Optimal sintering is achieved by carefully controlling parameters like sintering temperature, applied pressure, average grain size, and gaseous atmosphere.
Key Points Explained:
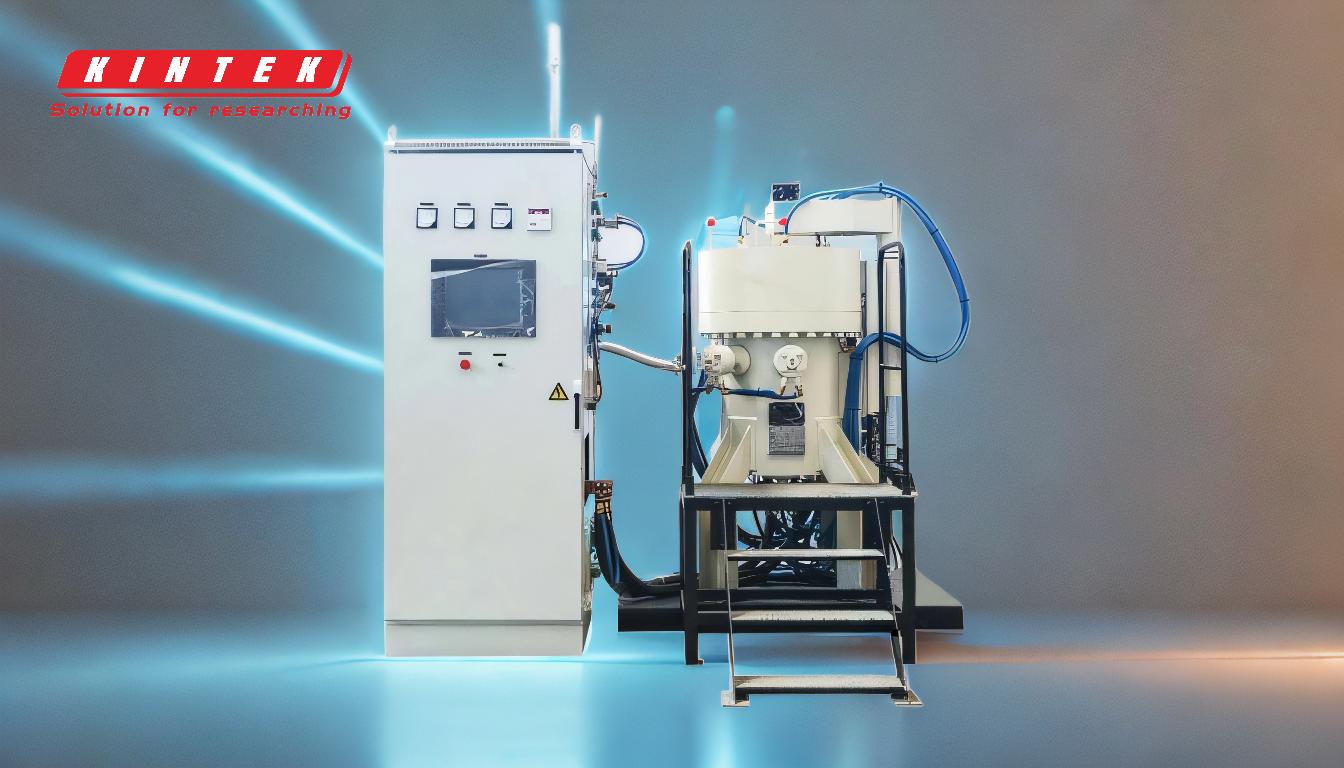
-
Reduction of Porosity and Enhancement of Properties:
- Sintering is considered successful when it reduces porosity and enhances properties such as strength, electrical conductivity, translucency, and thermal conductivity. This is achieved through the controlled application of heat and pressure, which promotes particle bonding and densification.
-
Influence of Temperature and Atmosphere:
- The sintering atmosphere (air, vacuum, or inert gases like argon/nitrogen) and temperature are critical variables. High-temperature sintering can increase tensile strength, bending fatigue strength, and impact energy. The choice of atmosphere can also affect the final properties of the sintered material.
-
Particle Size and Binding Area:
- The binding area associated with particle size is a determining factor for properties such as strength and conductivity. Smaller particles generally provide a larger binding area, which can lead to better densification and improved material properties. The initial grain size and temperature are controllable variables that influence vapor pressure and sintering kinetics.
-
Solid-State Sintering Parameters:
- In solid-state sintering, parameters such as temperature, time, and pressure are carefully controlled to achieve the desired material properties. This process involves the diffusion of particles in the solid state, which can be enhanced by higher temperatures and longer sintering times.
-
Final Porosity and Sintering Conditions:
- The final porosity of sintered ceramics depends on the initial porosity of the green compact, as well as the temperature and duration of the sintering process. Pure oxide ceramics, for example, require longer sintering times and higher temperatures due to the nature of particle diffusion in the solid state. Applying pressure can also reduce sintering time and porosity.
-
Techniques and Process Control:
- Different sintering techniques depend on factors such as the use of electrical currents, pressure, heat sources, and the materials being sintered. Process control parameters include air volume, vacuum, layer thickness, speed, and sintering endpoint. For instance, the air volume is typically 3200m³ per ton of sintering ore, and the sintering area is calculated as 70-90 m³/(cm²·min).
-
Optimal Sintering Process:
- The optimal sintering process is influenced by parameters such as sintering temperature, applied pressure, average grain size, and gaseous atmosphere. Finer powders and higher temperatures can increase compaction, but the amount of liquid phase must be carefully controlled to avoid defects. The choice of process depends on the expected product properties and limiting parameters.
-
Factors Influencing Sintering:
- Several factors influence the sintering process, including temperature, heating rate, pressure, particle size, and composition. Temperature determines sintering kinetics and material properties, while the heating rate affects densification. Pressure enhances particle rearrangement and eliminates porosity. Particle size and composition impact sintering behavior, with smaller particles and homogeneous compositions promoting better densification.
By understanding and controlling these key factors, manufacturers can tailor the sintering process to produce materials with specific desired properties, making it a versatile and essential technique in materials science and engineering.
Summary Table:
Key Factor | Impact on Sintering |
---|---|
Temperature | High temperatures improve tensile strength, bending fatigue strength, and impact energy. |
Atmosphere | Influences final material properties (air, vacuum, or inert gases). |
Particle Size | Smaller particles enhance densification, strength, and conductivity. |
Pressure | Reduces porosity and sintering time, improves particle rearrangement. |
Composition | Homogeneous compositions promote better densification. |
Cooling Rate | Affects final porosity and material properties. |
Sintering Time | Longer times increase densification, especially for pure oxide ceramics. |
Optimize your sintering process for superior material properties—contact our experts today!