Brazing is a versatile joining process used across various industries to create strong, durable, and leak-proof bonds between metal components. It involves melting a filler metal, which flows into the joint by capillary action, and then solidifies to form a robust connection. The purposes of brazing include joining dissimilar metals, creating complex assemblies, and achieving high-strength bonds without melting the base materials. It is widely used in applications ranging from automotive and aerospace to electronics and plumbing, offering advantages such as precision, cost-effectiveness, and the ability to join materials with different thermal properties.
Key Points Explained:
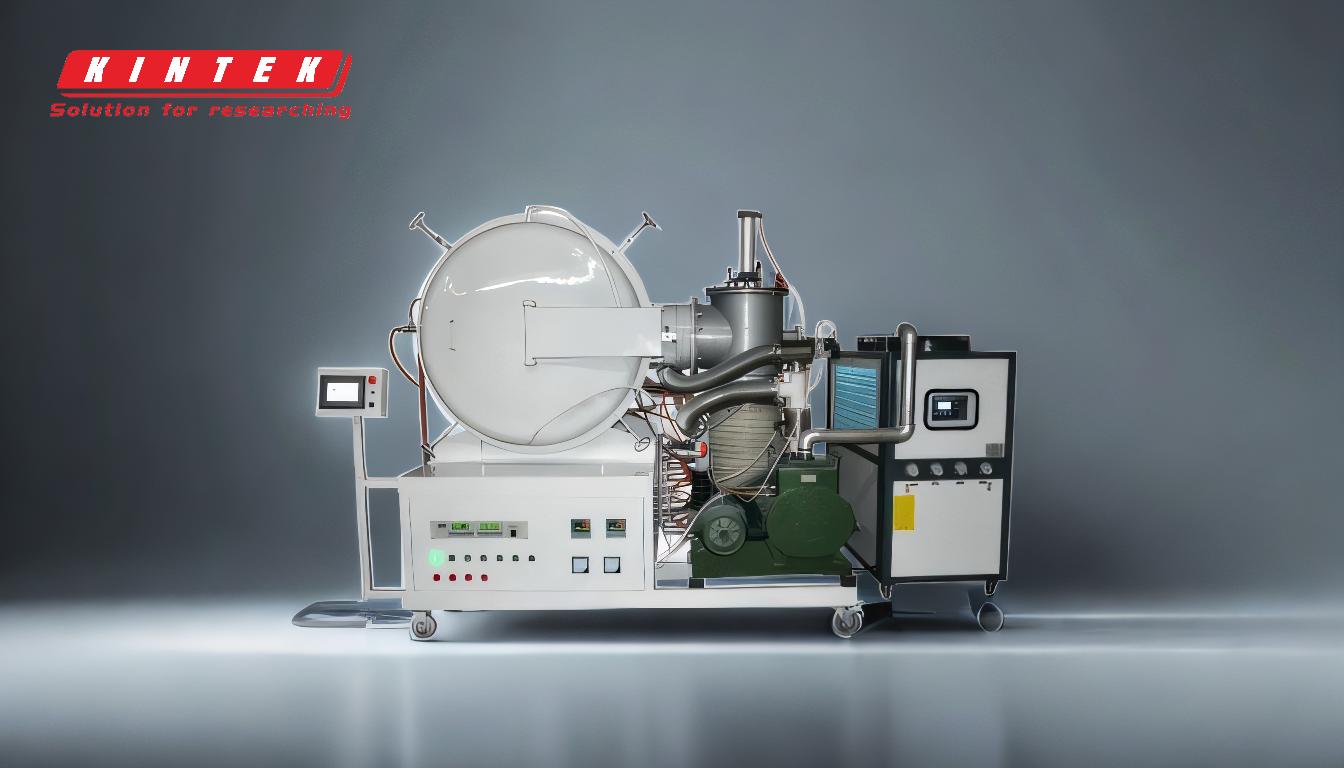
-
Joining Dissimilar Metals:
- Brazing is particularly effective for joining dissimilar metals, such as copper to steel or aluminum to stainless steel. This is because the filler metal used in brazing can bond with multiple base materials, creating a strong joint even when the metals have different melting points or thermal expansion rates. This capability is crucial in industries like HVAC, where copper tubing is often joined to steel components.
-
Creating Complex Assemblies:
- Brazing allows for the creation of intricate and complex assemblies that would be difficult or impossible to achieve with other joining methods like welding. The process is ideal for assembling components with tight tolerances or delicate structures, such as heat exchangers, electronics, and aerospace components.
-
High-Strength Joints:
- Brazed joints are known for their high strength and durability. The filler metal forms a metallurgical bond with the base materials, resulting in a joint that can withstand significant mechanical stress and thermal cycling. This makes brazing suitable for applications in demanding environments, such as automotive engines and industrial machinery.
-
Leak-Proof Seals:
- One of the primary purposes of brazing is to create leak-proof seals, which are essential in applications like plumbing, refrigeration, and hydraulic systems. The capillary action of the filler metal ensures that the joint is fully sealed, preventing leaks even under high pressure or temperature conditions.
-
Cost-Effectiveness:
- Brazing is often more cost-effective than other joining methods, such as welding or mechanical fastening. It requires less energy, reduces material waste, and can be automated for high-volume production. Additionally, the ability to join dissimilar metals and create complex assemblies in a single step further enhances its cost efficiency.
-
Minimal Thermal Distortion:
- Unlike welding, brazing does not melt the base materials, which minimizes thermal distortion and preserves the integrity of the components. This is particularly important for precision applications, such as in the electronics and aerospace industries, where even minor distortions can compromise performance.
-
Versatility Across Industries:
- Brazing is widely used in industries such as automotive, aerospace, electronics, plumbing, and HVAC. Its ability to join a wide range of materials and create strong, durable, and leak-proof joints makes it a preferred method for many applications.
-
Environmental and Safety Benefits:
- Brazing is generally considered a cleaner and safer process compared to welding, as it produces fewer fumes and requires lower temperatures. This reduces the risk of workplace hazards and environmental impact, making it a more sustainable choice for many manufacturers.
By understanding these key purposes of brazing, equipment and consumable purchasers can make informed decisions about when and how to use this versatile joining process to meet their specific needs.
Summary Table:
Purpose of Brazing | Key Benefits |
---|---|
Joining Dissimilar Metals | Bonds metals with different melting points and thermal properties. |
Creating Complex Assemblies | Ideal for intricate designs and tight tolerances. |
High-Strength Joints | Forms durable, stress-resistant metallurgical bonds. |
Leak-Proof Seals | Ensures fully sealed joints for plumbing and refrigeration. |
Cost-Effectiveness | Reduces energy use, material waste, and enables automation. |
Minimal Thermal Distortion | Preserves component integrity in precision applications. |
Versatility Across Industries | Widely used in automotive, aerospace, electronics, and HVAC. |
Environmental and Safety Benefits | Cleaner, safer, and more sustainable than welding. |
Ready to leverage brazing for your projects? Contact us today to learn more!