Brazing is a widely used joining process that involves heating a filler metal above its melting point and distributing it between two or more close-fitting parts by capillary action. While brazing is generally considered safer than welding due to lower temperatures, it still requires strict safety precautions to prevent accidents, injuries, and health hazards. Key safety measures include proper ventilation, personal protective equipment (PPE), fire safety protocols, and handling of hazardous materials. This answer outlines the essential safety precautions for brazing, ensuring a safe working environment for operators and compliance with safety standards.
Key Points Explained:
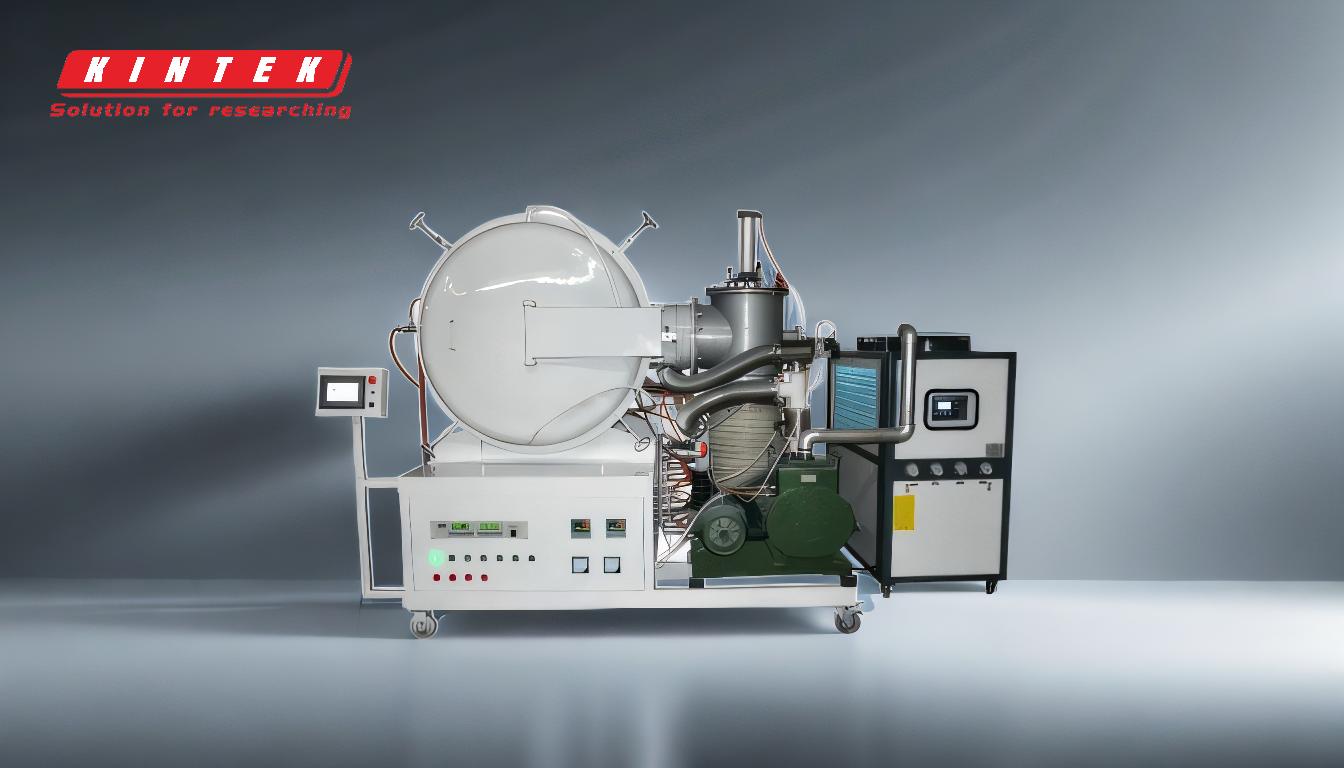
-
Proper Ventilation and Fume Extraction
- Brazing produces fumes and gases, including zinc oxide, cadmium oxide, and fluorides, which can be harmful if inhaled. Ensure the workspace is well-ventilated or use local exhaust ventilation systems to remove fumes at the source.
- Use fume extraction systems or hoods to capture and filter hazardous particles, especially when working in confined spaces.
-
Personal Protective Equipment (PPE)
- Wear appropriate PPE, including safety glasses or face shields to protect eyes from sparks and UV radiation.
- Use heat-resistant gloves to handle hot materials and tools.
- Wear flame-resistant clothing to prevent burns and injuries from molten metal or sparks.
- Respiratory protection, such as masks or respirators, may be necessary when working with materials that emit toxic fumes.
-
Fire Safety
- Keep flammable materials, such as paper, cloth, or solvents, away from the brazing area.
- Have fire extinguishers readily available and ensure they are suitable for metal fires (Class D extinguishers).
- Use fire-resistant barriers or screens to contain sparks and prevent accidental ignition of nearby materials.
-
Handling Hazardous Materials
- Brazing filler metals and fluxes may contain hazardous substances like cadmium or lead. Handle these materials with care, and avoid skin contact by wearing gloves.
- Store hazardous materials in properly labeled containers and dispose of waste according to local regulations.
-
Equipment Safety
- Inspect brazing equipment, such as torches, regulators, and hoses, for leaks or damage before use.
- Use equipment rated for the specific brazing process and ensure it is properly maintained.
- Follow manufacturer guidelines for operating temperatures and pressures to avoid equipment failure.
-
Training and Awareness
- Ensure all operators are trained in brazing safety procedures and understand the risks associated with the process.
- Conduct regular safety briefings and drills to reinforce safe practices and emergency response protocols.
-
Work Area Organization
- Maintain a clean and organized workspace to minimize tripping hazards and ensure easy access to safety equipment.
- Clearly mark hot work areas and restrict access to unauthorized personnel.
By following these safety precautions, brazing operations can be conducted safely and efficiently, reducing the risk of accidents and ensuring compliance with occupational health and safety standards.
Summary Table:
Safety Category | Key Precautions |
---|---|
Ventilation | Use fume extraction systems and ensure proper workspace ventilation. |
PPE | Wear safety glasses, heat-resistant gloves, flame-resistant clothing, and respirators. |
Fire Safety | Keep flammable materials away, use Class D extinguishers, and install fire barriers. |
Hazardous Materials | Handle and store hazardous substances carefully; dispose of waste properly. |
Equipment Safety | Inspect equipment for leaks or damage; follow manufacturer guidelines. |
Training | Train operators in safety procedures and conduct regular safety drills. |
Work Area Organization | Maintain a clean workspace, mark hot work areas, and restrict unauthorized access. |
Ensure your brazing operations are safe and compliant—contact us today for expert guidance!